Working together to harness manufacturing disruption
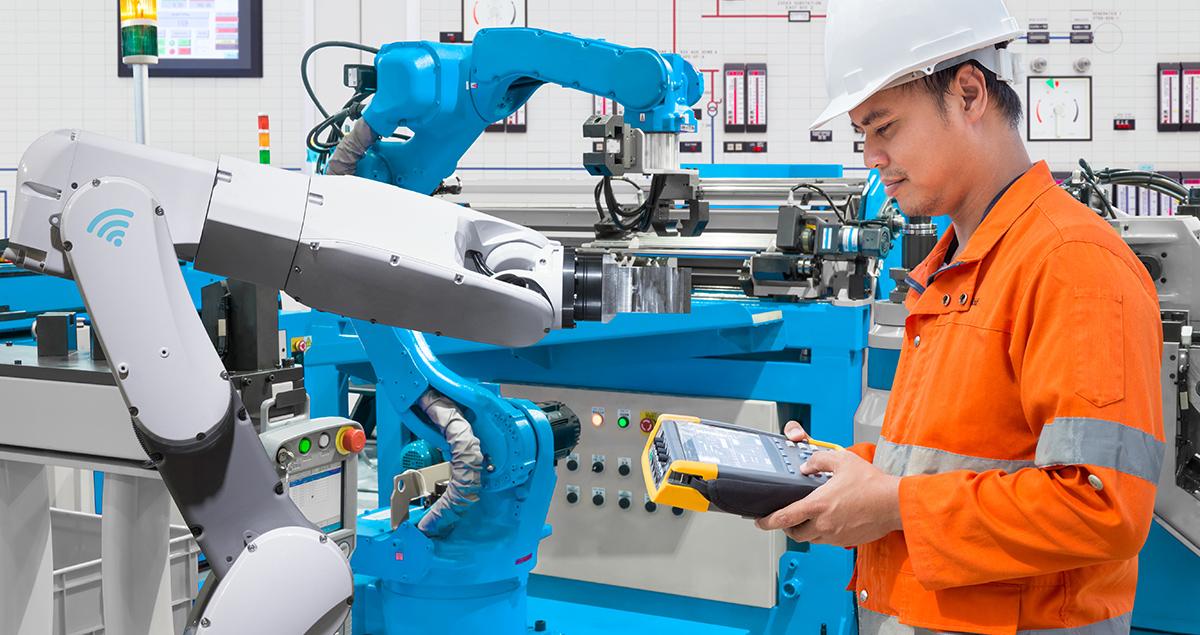
Reports of the end of work have been greatly exaggerated.
Artificial intelligence, robotics, the internet of things and technologies like 3D printing are radically transforming manufacturing in what is becoming known as the fourth industrial revolution.
But fears about machines taking human jobs are both exaggerated and misplaced.
While every previous industrial revolution has mechanised some jobs it has ultimately created many more human roles. And so it is with the latest revolution. Low skilled, repetitive tasks will be taken away from humans. But new more highly skilled roles will appear.
These roles in manufacturing are sometimes called “new collar” jobs, as they are neither the traditional blue or white collar jobs, but a mix of both.
However, as with all industrial revolutions, there will probably be a time lag between these new roles emerging and economies producing enough workers with the right skill sets to fill them.
One way of making the transition to the next era of manufacturing as easy as possible is by embracing the Japanese concept of ‘Chowa’.
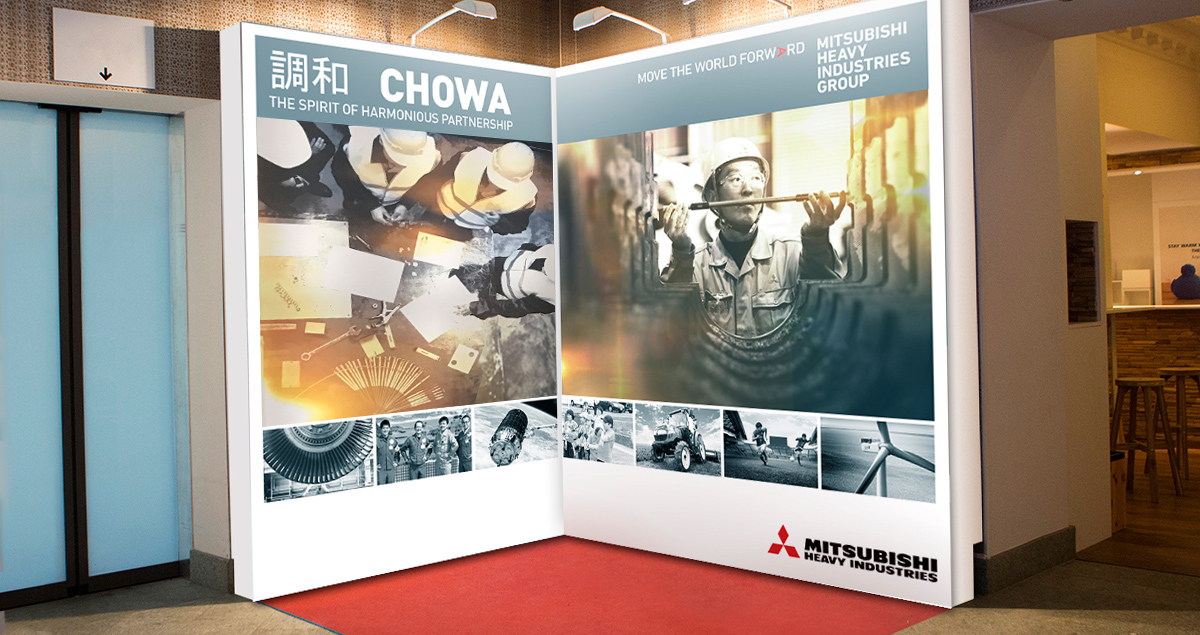
Building harmonious partnerships
Chowa is a Japanese term meaning ‘a spirit of harmonious partnership’.
Mitsubishi Heavy Industries (MHI) Chairman Hideaki Omiya says that by embracing Chowa and working together in partnership, companies – even rivals - can ensure a better future for both their customers and their employees.
And speaking at the World Economic Forum Annual Meeting 2018 in Davos, Omiya highlighted MHI’s own partnership with Siemens to create Primetals Technologies as an example of two global engineering companies working together harmoniously.
“Mitsubishi Heavy Industries believes that, to continue doing business, close relationships and cooperation with our employees, customers, partners, suppliers and government will be fundamental,” Omiya told a session on Global Production Systems. He was speaking as part of a panel featuring industry leaders, academics and politicians.
Omiya added that cooperation across borders would also be vital to ensure the correct skills mix, “Enabling employees to learn from their colleagues in other countries and transfer knowledge across borders is critical to meeting the new challenges in manufacturing”.
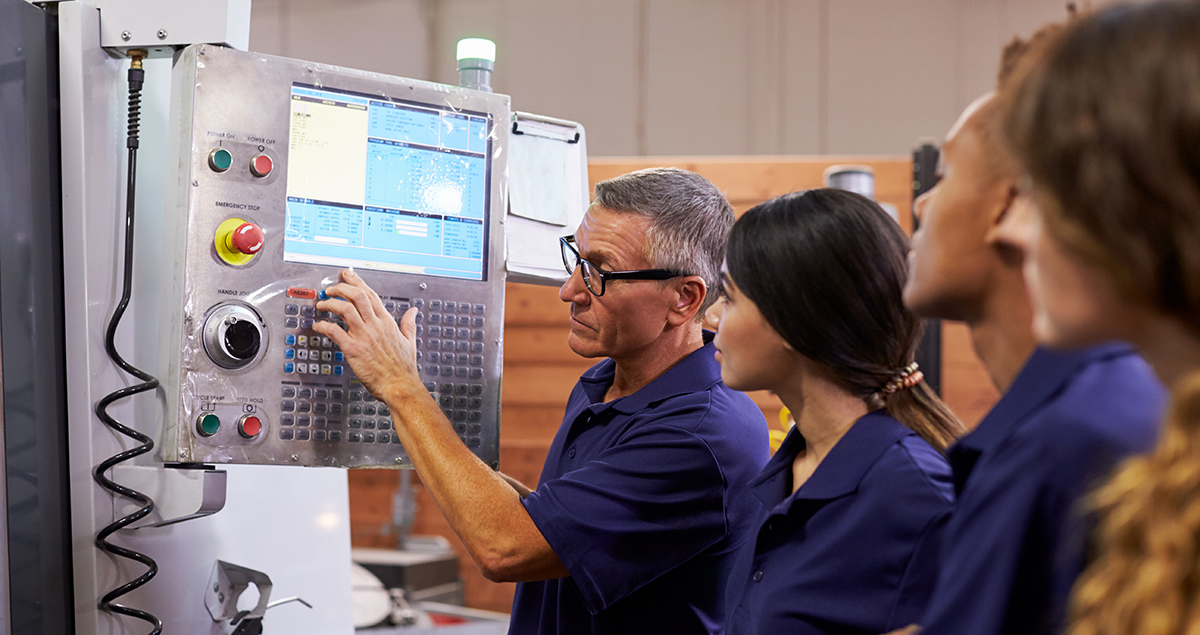
Global and local
International exchanges between employees and partnerships between companies are especially important when considering one key trend of the fourth industrial revolution: distributed manufacturing.
Distributed manufacturing uses the power of cloud computing and the internet of things to disrupt the traditional model of large scale factories producing goods and shipping them around the world.
Instead, designs and manufacturing processes can be conceived centrally and then distributed to smaller production facilities closer to customers. This opens up the potential of growth in many developing nations with a previously small manufacturing base, as well as in more advanced economies that have previously seen jobs in this sector disappear.
But simply exchanging manufacturing data will not be enough. New collar workers will need to move from countries with a strong manufacturing base, like Japan, to share their skills and insights with those working in new facilities.
And while the fourth industrial revolution will undoubtedly open up new opportunities in emerging markets, this will not lead to a new wave of offshoring. Geographical and historical manufacturing bases will remain important.
For example, MHI’s fully automated and high value-added facilities will remain in Japan so that the company can build on existing relationships and skills.
Hideaki Omiya said he believed MHI would need to keep fully automated factories in Japan because factory automation is dependent on robotics companies like Fanuc and Kawasaki. Such factories would need to be continuously upgraded and developed on a yearly basis – hence the need for proximity to the robotics companies.
To deliver high-value added products and parts, Omiya said MHI needed the close support of engineers and researchers. If production is spread across multiple countries, this is harder to achieve.
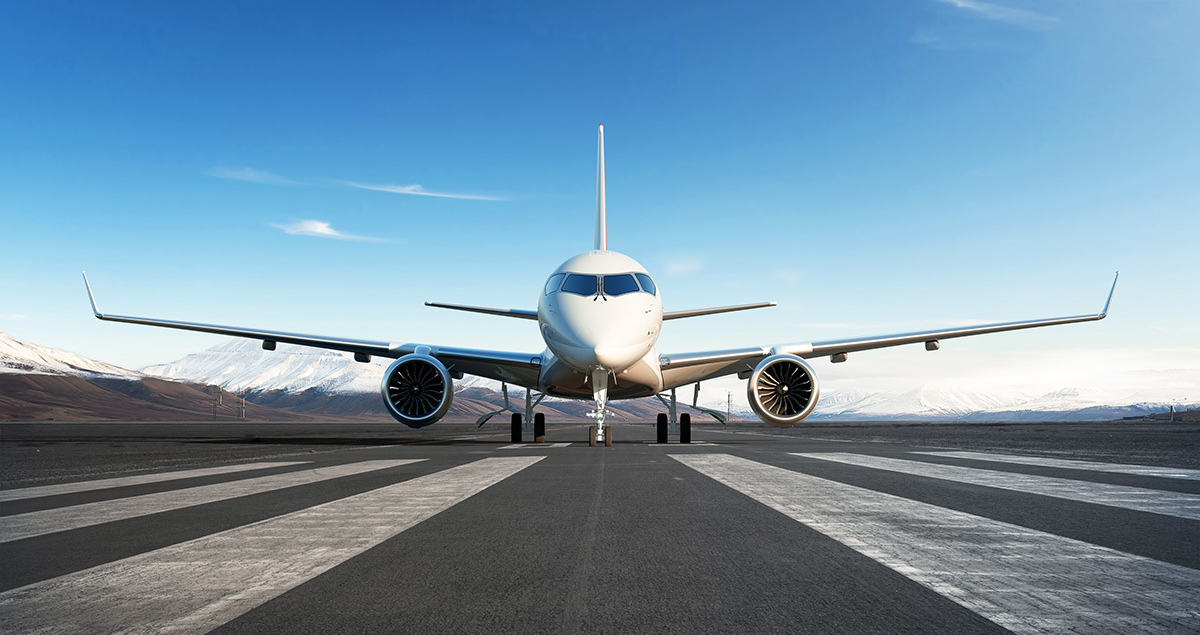
Two futures
The distinction between different types of manufacturing, some that can be replicated easily around the world, and others that will still require a high level of central expertise, can be illustrated by two modes of transport: electric vehicles and commercial aircraft.
“We can see the future trends of production in two products,” said Omiya. “Electric vehicles attract lots of new market entrants as they are easy to produce, instigating dramatic change in the industry. Aircraft are highly complex systems, so we see less drastic change in this market.”
It is clear that manufacturing will be changed in many ways by new technologies but the changes will be different depending on the type of industry. Change will become ever more rapid and both companies and workers must build on their existing skills to keep up.
But manufacturing jobs are not disappearing. They are evolving. And working together, companies can ensure those changes benefit everyone.
Related tags
