New collar: where to find the next-generation manufacturing workforce?
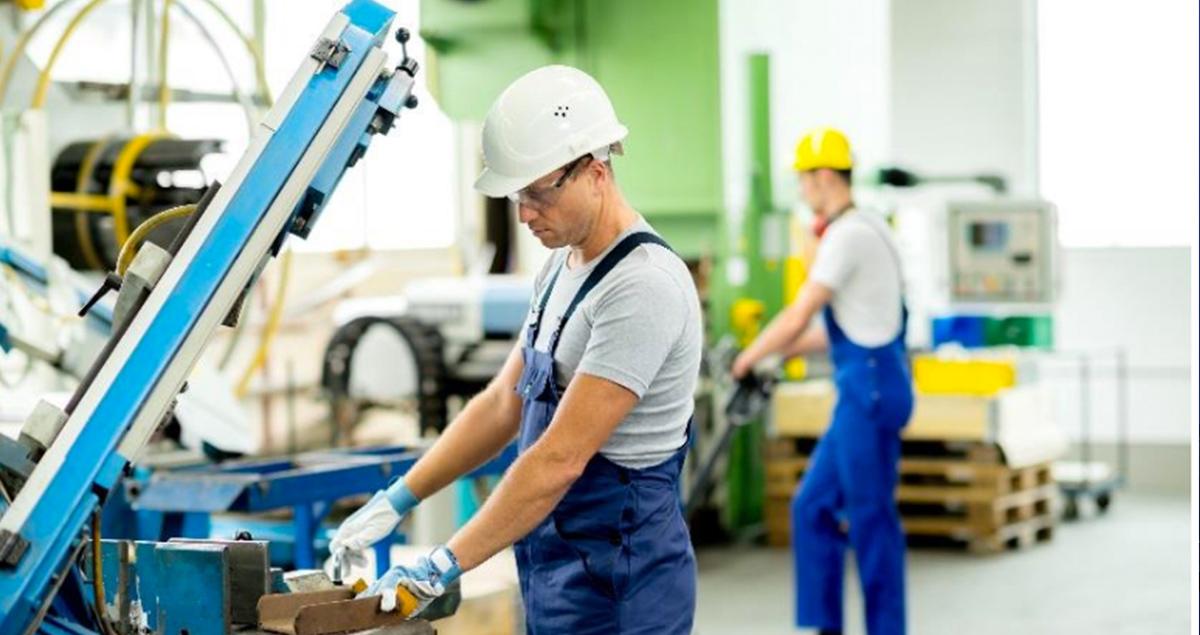
The workplace is changing. Technology is ever-present in virtually every kind of job today, from taxi drivers hired via smartphones, to teachers instructing their classrooms via digital displays.
Some of the most dramatic changes of all are taking place in our factories and other industrial environments.
Gone are the days of grimy production lines manned by hundreds of manual workers. Today the factory is a high-tech environment where automated machinery and robots are overseen by highly-skilled operators.
This is what is meant by the term “new collar”: first coined by IBM CEO Gini Rometty, new collar replaces the old division between “blue-collar” manual labor on the factory floor, and “white-collar” clerical and management jobs.
Industrial Jobs Revolution
Although technology in the workplace is increasing, this doesn’t necessarily mean there that there will be fewer jobs.
A report by the World Economic Forum - Realizing Human Potential in the Fourth Industrial Revolution - claims the number of jobs lost globally to automation could be as little as 9%.
The fourth industrial revolution marks the move away from automated factory processes to intelligent, integrated digital systems such as the Industrial Internet of Things (IoT) that are transforming the way we work.
In this revolution, the robots are not taking away jobs – global factory payrolls hit a five-year high in 2017.
Instead, they are creating new jobs, and changing the nature of those that already exist: the World Economic Forum estimates that by 2020 more than a third of core skills required by occupations will have changed.
This presents a huge opportunity for manufacturing, but also an enormous challenge: globally the industry is already facing a skills gap. In the US alone, between now and 2025 nearly three and half million manufacturing job vacancies will be created.
While 700,000 of these are estimated to be newly-created roles, 2.7 million will be created due to retirements.
This growing gap is partly to blame on ageing populations in North America, Asia and Europe: globally, the number of older people is expected to exceed the number of children for the first time by 2047.
However, manufacturing’s over-reliance on the baby-boomer generation, which may account for up to a fifth of the sector’s workforce, is also due to an image problem.
According to a survey by Deloitte, Americans are apprehensive about a career in manufacturing because they are worried about job security and stability, a weak career path and poor pay.
This negative image is reinforced in many education systems around the world.
The World Economic Forum report claims that “the premium placed on college attainment, in both developed and developing economies, means technical and vocational education and training (TVET) is often viewed as a ‘second-best option’ for learners”.
As a result, students have generally been discouraged from pursuing careers in areas such as manufacturing, and TVET programs have been neglected.
The Next Generation
Finding the next generation of manufacturing workers relies on both the reshaping of public opinion, and equipping the workforce necessary to thrive in the rapidly changing landscape of the fourth industrial revolution.
New collar workers need to be both specialists and multi-skilled. For example, according to UK manufacturers organization EEF, companies preparing for the fourth industrial revolution are switching from single trades to multi trades, such as an electrician who is also a mechanic.
This new collar blend of using multiple skills in an advanced manufacturing environment is typified by Mitsubishi Heavy Industries’ employees such as Kohei Miyoshi.
He oversees production of prototypes for the components of turbochargers, such as turbine rotors.
“Unlike mass-manufactured products, prototypes have no specific manufacturing processes or processing methods as such,” says Miyoshi.
“Also, there are typically about 50 prototypes for turbine rotors on back order on average, but with prototyping, it is only drawings and materials that are actually provided.”
This requires a high level of precision and speed from workers who are highly skilled, but also capable of operating up to 15 different kinds of machines.
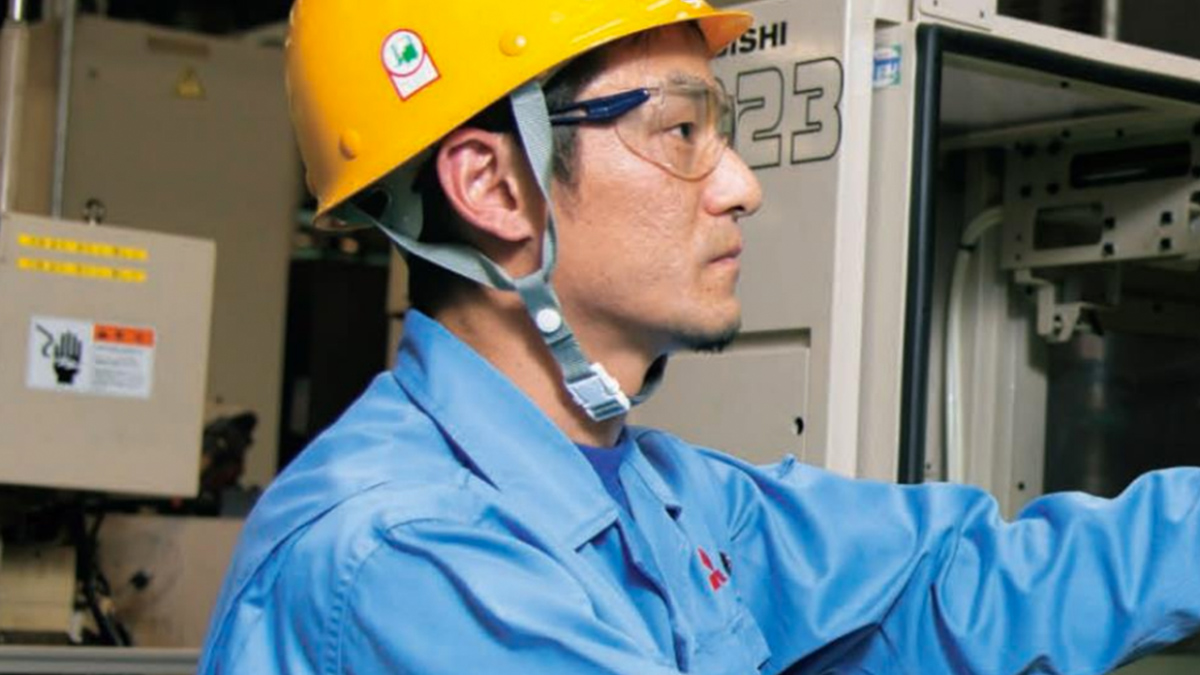
Education
Some studies suggest that 65% of children entering primary school today will have jobs that do not yet exist and for which their education will fail to prepare them, exacerbating skills gaps and unemployment in the future workforce.
To build a workforce ready for the fourth industrial revolution, changes must be made both to the way workers are educated as children at school, and once they are in the workplace.
The World Economic Forum report suggests regular reviews of school curricula to make sure they meet the demands of the ever-changing workplace.
Likewise, the public needs to be informed about the nature of the modern workplace, and that the work available in manufacturing is not the undesirable blue-collar roles of old, but the highly skilled and rewarding new collar roles.
The rapidly changing nature of the workplace also means lifelong learning matters more than ever before.
This has been recognized by Singapore’s government, which is giving every individual aged 25 and over a training credit of US$500, which will be topped up at regular intervals and will not expire. This credit can be used on a number of government-supported courses and is open to both students in school and to workers with years of experience.
Meanwhile, a good example of linking training to the direct needs of employers is taking place in the UK. LinkedIn, the world’s largest professional network, and the Greater Manchester Combined Authority (GMCA) have collaborated to analyze local vacancies and more than 600,000 local LinkedIn users’ skills and employment data. Based on this information, training modules will be developed and delivered by GMCA.
Old and New
While governments must work closely with industry to make sure the next generation of new collar works have the right skills, manufacturers must also play their part.
One way of addressing this is for companies to utilize the vast resource of human experience and expertise that already exists in their workplaces - recognizing the value of veterans in the workplace.
For example, Mitsubishi Heavy Industries has created a new company for workers of retirement age and above. It supports a range of engineering, procurement and construction projects, and also enables veterans to share their knowledge with newer recruits to help develop the next generation of specialists.
Related tags
