The Internet of Things will transform our lives
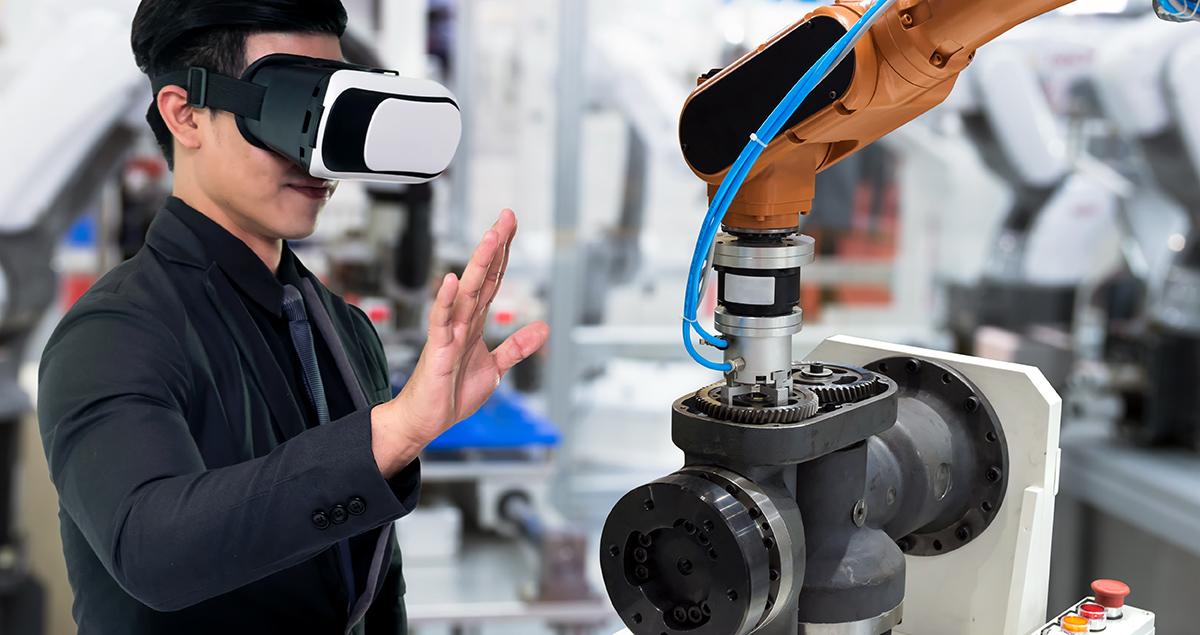
Refrigerators that shop online for groceries, cars you control with your phone and heating systems that learn your temperature preferences.
All of these are technologies that just a few years ago would have seemed like science fiction, but today are commercially available.
The Internet of Things (IoT) is rapidly touching every part of our daily lives – both in the products and services we use every day, and in the industrial processes that get those products to us in the first place.
At its most basic, an IoT device can be simply something equipped with a sensor. That sensor may be as basic as a Radio Frequency Identification (RFID) tag, which simply contains digital data about the product that has been tagged.
Or the sensor may be able to record information – such as mobile phones and smart wristbands that can tell you how many steps you have taken.
More advanced IoT devices, meanwhile, are not simply passive sensors – they can be controlled remotely via mobile phones, and even contain a basic level of artificial intelligence (AI), learning your habits and preferences.
As machine learning and Artificial Intelligence (AI) improves, more and more devices will be truly smart, capable of acting independently of their owners.
This offers the tantalizing prospect of eliminating the need for more and more basic tasks at home, while achieving unprecedented levels of efficiency at work.
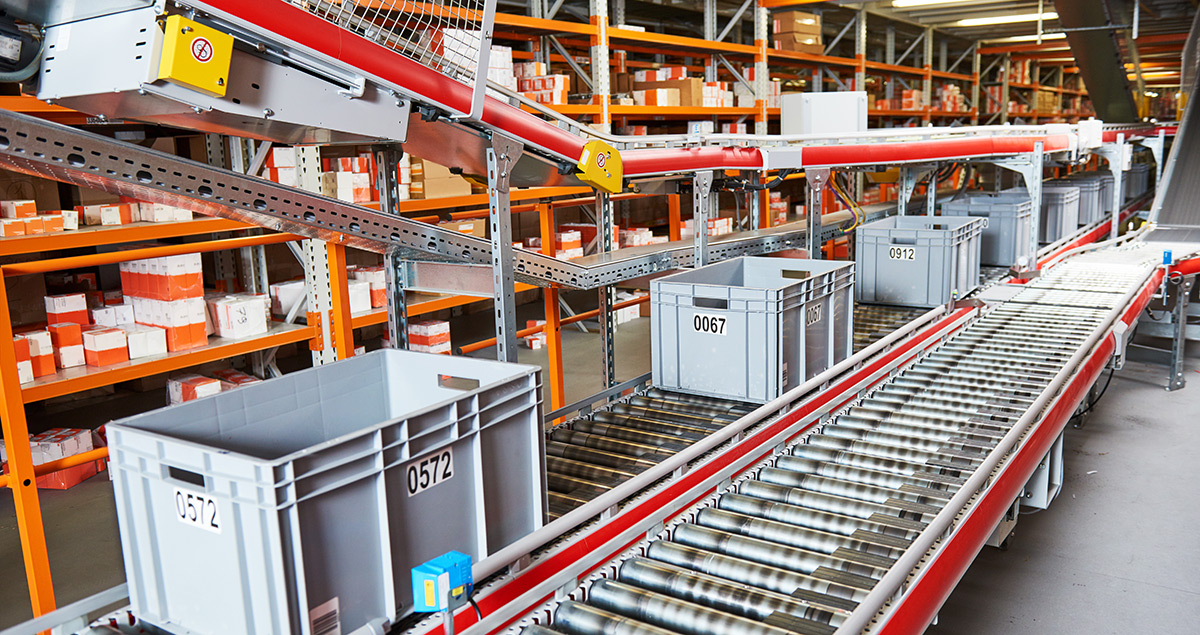
Industrial IoT
In manufacturing, the efficiencies offered by the industrial IoT are already well established.
Over the past decade RFID tags have risen to become the most widely used method of tracking products, giving suppliers and customers accurate information about goods’ journeys from the factory floor to the front door.
They can also drive improvements in quality and efficiency in the manufacturing process.Mitsubishi Heavy Industries Aero Engines Ltd (MHIAEL) makes parts for the jet engines in commercial airliners.
One of the parts it produces the most is a turbine blade, with MHIAEL’s Nagoya plant making as many as 12,000 to 15,000 blades per month.
MHIAEL’s turbine blade customers require a strict traceability of each blade, with a production log for every single stage of the manufacturing process. Since 2008, MHIAEL has been using RFID tags to trace each blade.
Compared to previous manual data logging processes, the use of an RFID tag system has cut product defect rates to a tenth of what they were previously.
This is because the tags enable MHIAEL to know exactly where each blade is in the manufacturing process at any given time.
When combined with measurement instrumentation attached to the manufacturing machines, MHIAEL factory staff can see if there are any variations in the processes, and immediately know which blades are likely to be affected.
Similar efficiency gains are taking place in the world of steel production, where smart electric arc furnaces are replacing traditional blast furnaces for the recycling of scrap metal.
The melting process in electric arc furnaces can be automated and monitored via a smartphone app.
This means that they can review and act on information in real time, from wherever they are, so that issues can be headed off before they affect the operation of the plant.
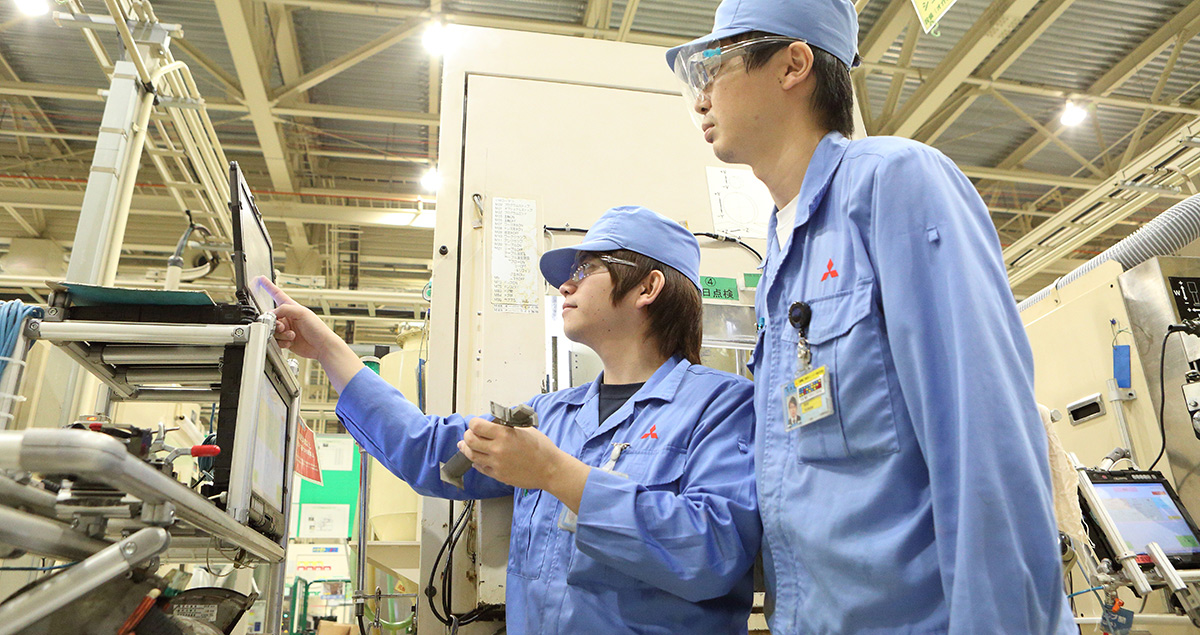
Smart infrastructure
It isn’t just at home and in the factory that the IoT is making life run more smoothly.The vital infrastructure that underpins our daily lives is also benefitting from becoming “smart”.
In cities around the world leaky pipes are being identified as IoT-enabled sensors alert water companies to lost pressure or reduced water flow in a specific location, indicating a potential problem.
And on the railways, the IoT is transforming the way trains are maintained.MHI Group has helped develop a smart maintenance system. Sensors on the train carriages monitor the condition of doors, motors and other parts and, when necessary, alerting operators so that components can be repaired or replaced before they fail – avoiding costly delays and breakdowns.
Condition monitoring and preventative maintenance are increasingly common in industrial environments, and by bringing this technology to the rail sector, MHI hopes that it can help emerging economies with less well-developed rail systems to improve their maintenance regimes.
Big Data, AI and the future
With everything from smartphones to sewage pipes equipped with sensors, we are today living in the world of Big Data.
At present, what we can do with all this data is largely limited to how we as humans understand and interpret it – and how much time we have to wade through it all.Advances in machine learning and AI will change all this, as computers learn how to analyze data and act on it far quicker than we can.
The most high-profile advance in this area is the advent of autonomous vehicles, with some in the motor industry predicting that driverless cars could be commercially available as early as 2020.
MHI itself is working on autonomous technology in an industrial environment.Mitsubishi Caterpillar Forklift America (MCFA), part of Mitsubishi Logisnext, provides its customers with an IoT-enabled system called LiftLink.
This system allows maintenance engineers via a web application to identify forklift trucks anywhere in the US that may be in need of maintenance.
Trucks operations and maintenance history can be accessed at the click of a mouse, helping maintenance engineers to correctly identify sources of breakdown and bring the correct parts before they travel to the forklift truck’s location.
MCFA is now installing more advanced condition monitoring to push forklift truck owners towards predictive maintenance.
Mitsubishi Logisnext is also developing forklift trucks that can operate autonomously, responding to the Big Data generated by all the sensors surrounding it in the factory.In so many aspects of the work and domestic environments, the IoT is already making our lives more convenient, more efficient and safer.
Related tags
