Responsible leadership and collaboration in manufacturing
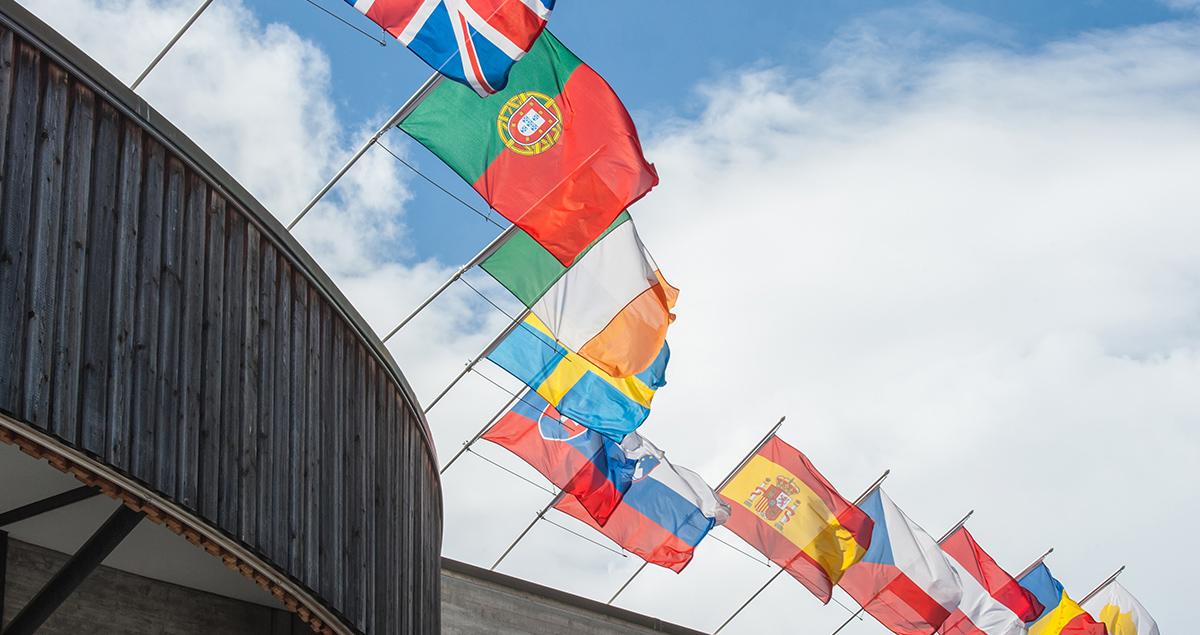
Responsible leaders and strong partnerships will be key for the manufacturing sector to thrive in the digital age.
Digital technology, robotics and artificial intelligence are causing a fundamental shift in how manufacturers operate.
While automation offers the sector an opportunity to lower costs and boost quality, manufacturing leaders need to steer their organizations carefully and responsibly. To allay the risk of humans losing jobs to robots, they need to ensure staff are equipped with the digital skills they, and their companies, need to prosper.
At the same time, the pressure to meet ever more diverse customer needs requires leaders to forge strong partnerships, both within the supply chain and with other complementary businesses - including competitors. Companies can no longer expect to provide ‘end-to-end’ solutions alone.
Putting this vision into practice will be essential for successful digital-age manufacturing.
Responsible leadership
Leading responsibly and working in partnership are not only key themes in the manufacturing sector – they are also guiding principles for world leaders.
Responsible and responsive leadership was the main theme at the World Economic Forum Annual Meeting in Davos in 2017, while the need for working in partnership is the main topic at Davos in 2018.
Being a responsible leader includes preparing workers for the changes ahead and equipping them with the skills they need for them – and their companies – to flourish economically.
The fourth industrial revolution marks a move away from basic and monotonous factory processes as advances in artificial intelligence and robotics automate tasks that previously could only be carried out by humans.
However, this doesn’t mean cutting jobs. A report by the World Economic Forum – Realizing Human Potential in the Fourth Industrial Revolution – quotes research that suggests the number of jobs lost globally to automation could be as little as 9%. Instead, new or transformed manufacturing roles are being created that fit neither traditional blue nor white-collar roles: “new collar workers”, highly-skilled people who work collaboratively with machines.
It will take responsible leaders to balance the benefits of automation with the need to ‘upskill’ people. The aim must be for workers to manage robots rather than be replaced by them - and use their human creativity to ensure continued innovation.
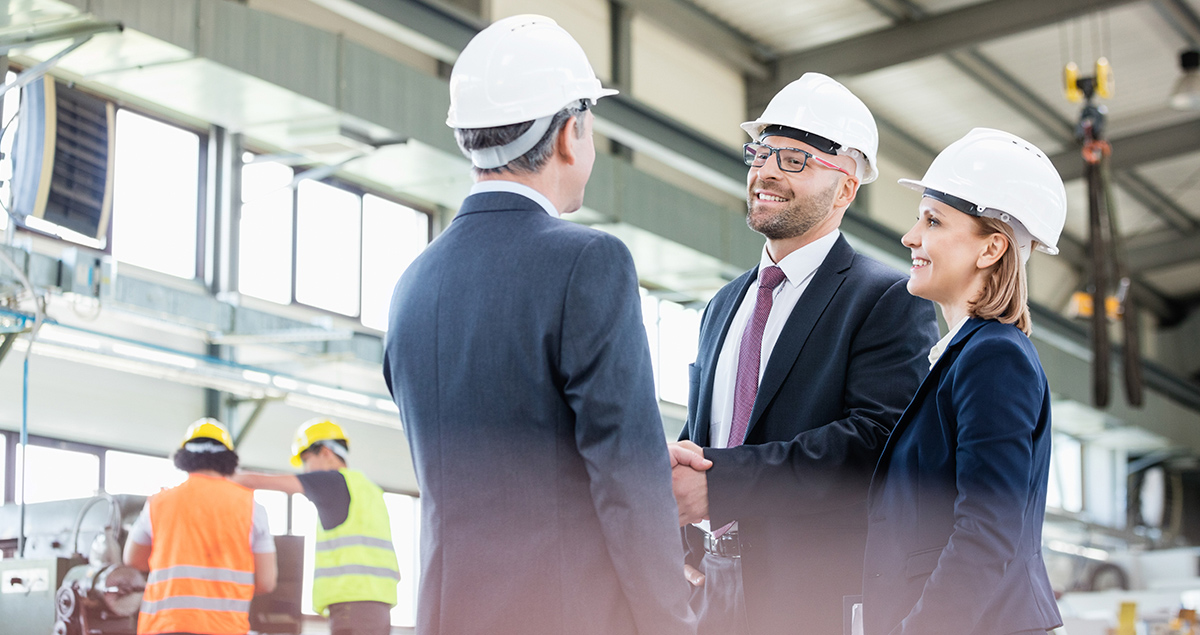
Collaborative partnerships
Digital technology is also likely to allow manufacturers to be far more responsive to customers, with customization predicted to be another key trend.
Being responsive to market demands or an individual customized order will require manufacturers to be experts and to be innovative. This will drive more companies to focus on their core markets and areas of expertise, as Mitsubishi Heavy Industries (MHI) has done.
And more manufacturers becoming specialists will naturally lead greater levels of supply chain collaboration – and to partnerships with those they formerly competed with.
“We are moving from the old model of mass production and global supply chains, towards a world of distributed manufacturing, shared factories and IT service centers,” MHI’s Chief Financial Officer Masanori Koguchi said at the Financial Times Future of Manufacturing Summit 2017 held in London.
The companies that share the most – and commit to life-long learning for their employees – are likely to both drive and thrive in the digital age.
Related tags
