Modern Monozukuri: Building nuclear reactors at MHI’s Kobe plant
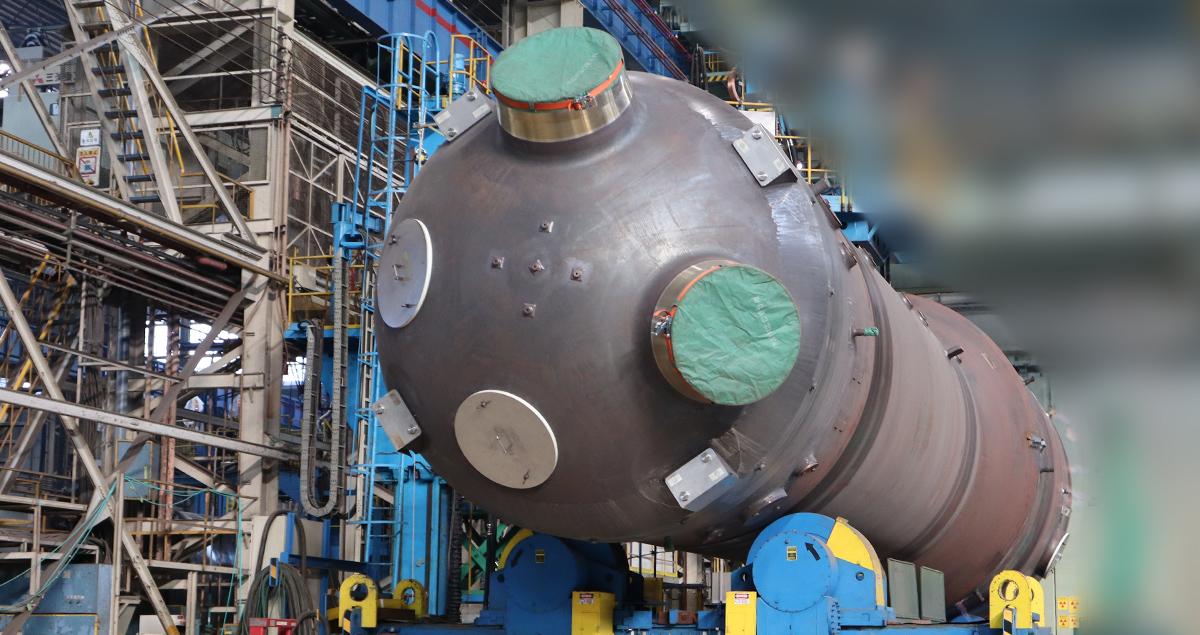
This article was previously published in our newsletter, if you're not already a subscriber, sign up here.
A plain factory building in Kobe, Japan’s western port city, houses a feat of precision engineering that is rare in the world. Inside it, a giant metal shell – 11 meters high, 4 meters in diameter, weighing 130 tons – is moved slowly along a series of machine tools. Each of these is itself as big as a house and each has its purpose: turning, milling or welding parts onto the shell.
Step by step, more than 500 components such as, guide tubes, baffle plates and other components are assembled, many made from corrosion-resistant stainless steel and machined to tolerances of plus/minus 0.1 millimeter. The result, after 40 months, is a reactor pressure vessel internal –the heart of a nuclear reactor -- which contains the uranium reactor fuel and, during operation, is flooded with very hot, highly pressurized and – very soon – radioactive water. The water boils into steam in connected steam generators and is then forced along a separate system of pipes to drive a turbine and generator to produce electricity.
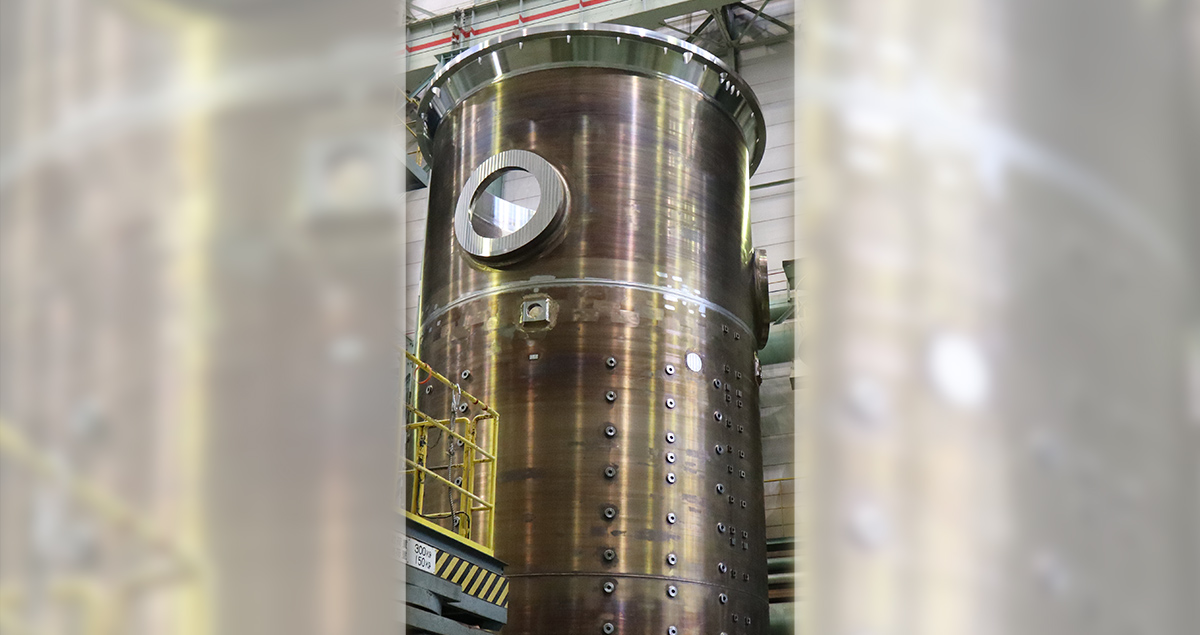
The nuclear industry’s ability to supply large volumes of emission-free, reliable baseload power is a powerful advantage at a time when climate change and energy security have become pressing global concerns. More and more countries are building new nuclear plants, restarting mothballed ones and extending the life of those already in operation. After a long hiatus after the Fukushima Daiichi accident in 2011, orders are starting to flow again, and public opinion is turning supportive – even in Japan.
Back at the forefront
This is a welcome development for Mitsubishi Heavy Industries (MHI) Group, which has been involved in the nuclear business for more than half a century and built Japan’s first nuclear plant, a pressurized water reactor (PWR), in 1970.
Today, MHI is one of a few company from the OECD group of nations that can offer a complete service from R&D, planning and design to manufacture, installation and commissioning, regular inspection and maintenance and overall project management. As a result, it has been involved in the construction of all 24 of Japan’s PWR plants and supplies major components to customers in the US, France and several other European and Asian countries.
As Japan’s leading nuclear manufacturer, the group is also developing the next generation of advanced light water reactors (with enhanced safety features), as well as small modular, micro, fast and high-temperature gas reactors. Internationally, MHI plays a key role in the ITER project that is trying to solve nuclear fusion; domestically, it is currently focused on restarting Japan’s nuclear fleet, both its own PWR plants and the boiling water reactors (BWR) built by others.
The center of this historic expertise and many of its future growth plans is Kobe. Formally known as the Kobe Shipyard and Machinery Works, this giant 670 thousand square meter facility did indeed start life as a shipyard in 1905 and built submarines and – incidentally – Japan’s first car. It also fathered the Takasago factory where MHI builds its world-leading gas turbines, which split off in 1964.
Today, Kobe still makes submarines, as well as aircraft and rocket parts, chillers and other components. However, more than half of its revenue -- some 250 billion yen (1.6 billion dollars) last fiscal year -- came from the nuclear business such as engineering, construction, maintenance services and manufacturing the core components of nuclear plants: reactor pressure vessels, the even bigger steam generators and all the large and small pipes and tubes that connect these or fit inside them.
A quality operation
While the parts are very different, the process by which they are made is similar. There is enormous attention to detail coupled with proprietary methods developed in house – such as the customized drill that hollows out the 4,500 tubes in each steam generator with pinpoint accuracy and guaranteed smoothness.
Such demanding tasks require the best equipment and the most modern methods. The factory bays are stacked with high-end machine tools from Germany, Italy and Japan. And Kobe specializes in advanced welding techniques, like electron beam welding that can fuse thick pieces of metal in one pass and does not require welding material, which minimizes any distortion.
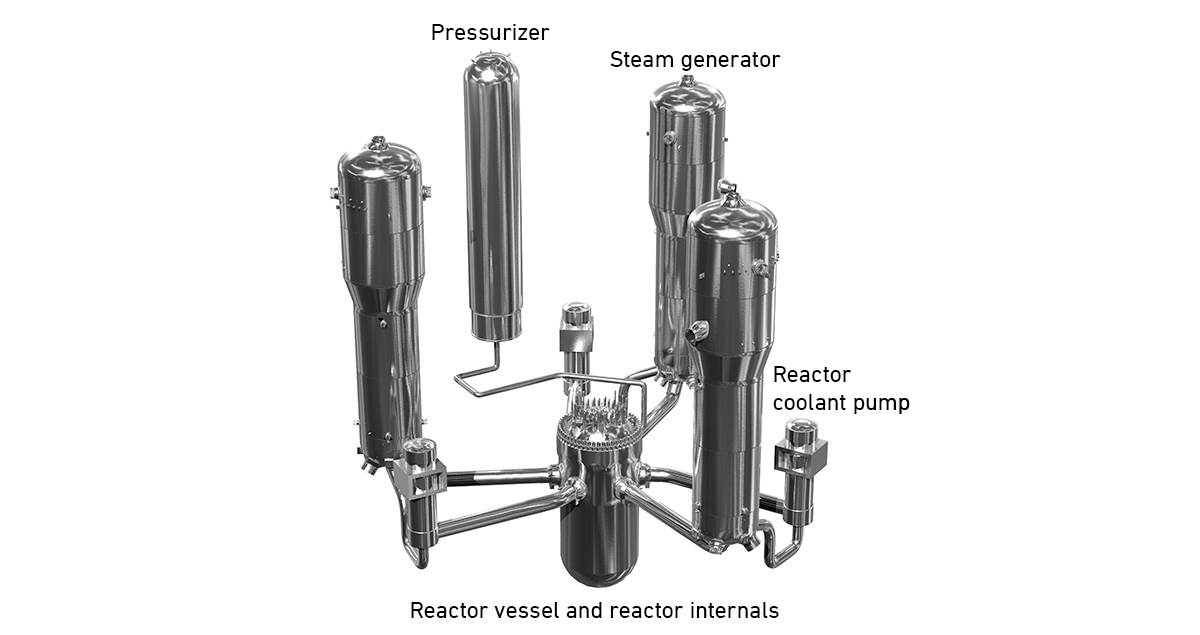
More and more of the steps are automated, though some of the most demanding still require a human. Welding together the two main parts of each steam generator takes three days and while the external submerged arc welding torches are controlled by a machine, the internal seam is welded by a worker laboring inside the generator in short shifts at more than 150°C heat.
Prioritizing safety
MHI demonstrates the same attention to detail when it comes to quality control, maintenance and operations – with safety as its absolute top priority. Components are checked at each stage of manufacturing and a safety culture among employees is reinforced by regular training, seminars, audits and an exhibition hall that showcases previous incidents – which staff are expected to visit at least annually.
Beyond that, Kobe has its own maintenance training center that boasts a mock-up of a full-size reactor vessel that can be flooded with more than 1,000 tons of water so that maintenance workers can train in realistic conditions.
To further assist both customers and maintenance engineers, MHI has developed a number of its own inspection devices, including ultrasonic sensors and scanners that can examine the integrity of pipes, and check welded joints for damage. Since nuclear equipment (with all those thousands of tubes) needs to be inspected every 13 months, the ability of these systems to work quickly and without human oversight is key.
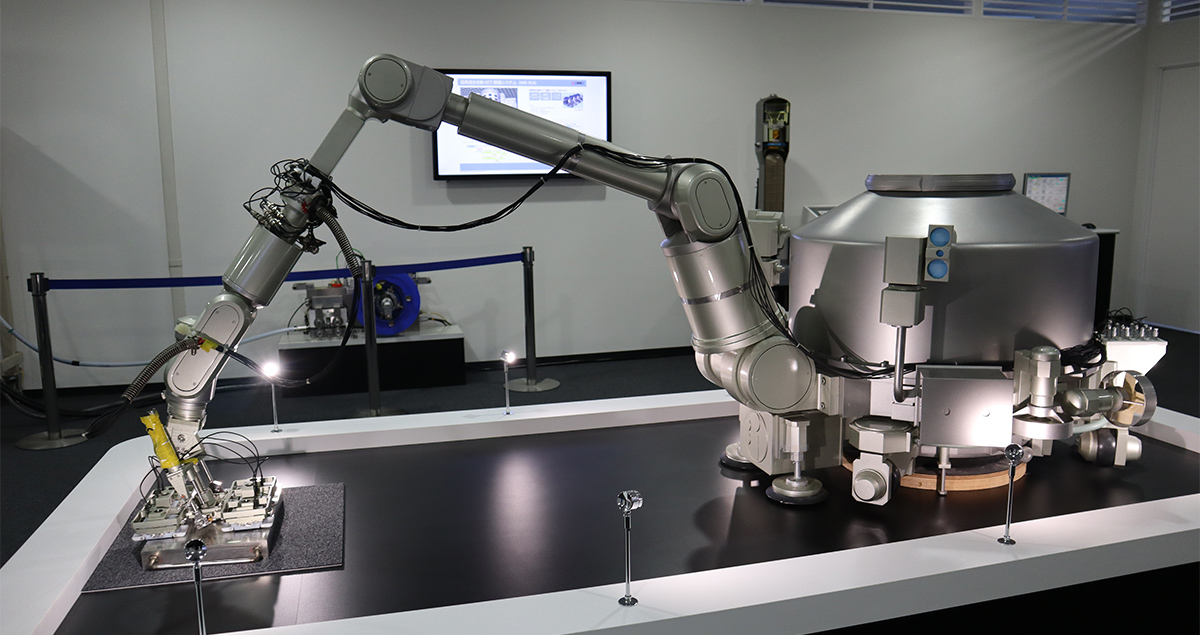
The most eye-catching inspection device, however, is the A-UT robot, which was developed and built entirely in-house at Kobe. This looks a little like a small metal giraffe, features a robotic arm with seven axis and a sensor pad at the end, and can swim like a submarine inside the reactor vessel or stick on walls with its vacuum pad feet.
The time and effort it took to develop this robot and the obvious pride the Kobe staff take in explaining its functions exemplify MHI’s commitment to its nuclear power business, which is set to provide the group with many years of profitable growth while making an important contribution to worldwide decarbonization.
Discover more about versatile nuclear solutions
Related tags
