Demand for dual-fuel turbines is rising. Here's why

The energy industry has long heralded natural gas as the “bridging fuel” that will help it move from heavy fossil fuels to cleaner energy sources.
However, power plant owners are becoming increasingly aware that even natural gas’ days may be numbered and are seeking ways to future-proof their plants for a net-zero emissions future. Whether investing in new builds or retrofitting existing plants, installing cutting-edge turbine technology can help prevent today’s infrastructure becoming tomorrow’s stranded assets.
According to Mitsubishi Power Americas CEO Paul Browning, in 2020 about half of Mitsubishi Power’s customers in the U.S. asked to change their gas turbine orders to dual-fuel turbines, which combust a natural-gas and hydrogen mix, producing fewer emissions.
This step-change turbine technology can currently burn a ratio of 30% hydrogen to 70% natural gas. But they will in the future be capable of burning 100% hydrogen, generating zero CO2 emissions.
Plant life
With sustainability high on the energy industry’s agenda, a growing urgency to decarbonize power production could explain the spike in plant owners opting for dual-fuel turbines. A raft of pledges by US investor-owned electric utilities to reach net-zero emissions by 2050 is an indication of the changes taking place in today’s energy sector.
Although 2050 may seem like a long way off, the life of energy infrastructure such as combined cycle gas turbine (CCGT) plants can often span several decades. Major investments in new equipment today must be viable in the decades to come.
Hydrogen’s only emission when burned is water. It can be produced through electrolysis powered by renewable electricity, and it can provide a steady source of power – all of which make it greener than natural gas and an ideal partner to renewables.
“Hydrogen will become increasingly important as a means of storing renewable energy and providing dispatchable renewable power when it’s needed,” says Browning.
“Just as natural gas replaced coal as a supporting fuel for renewables, in time hydrogen will supersede gas as a cleaner alternative.”

At the Intermountain Power Plant project in Utah, an existing 1.8GW coal-fired power station will be retired in 2025 and refitted with Mitsubishi Power’s game-changing, highly efficient dual-fuel turbines, which will run on a mix of natural gas and 30% emissions-free hydrogen, increasing to 100% clean hydrogen no later than 2045.
In the mix
The huge environmental benefits of realizing 100% hydrogen-fueled turbines are clear, as this would eliminate CO2 emissions from the entire power-generating process when using hydrogen produced using renewables. But while increasing hydrogen’s dominance in the fuel mix might sound like a simple aim, the gas can be difficult to handle, leaving Mitsubishi Power’s engineers facing unique challenges.
With a higher concentration of hydrogen the fuel mix becomes less stable, increasing the danger of flashbacks, while also generating higher levels of nitrogen oxide (NOx) emissions – the gases found in vehicle emissions.
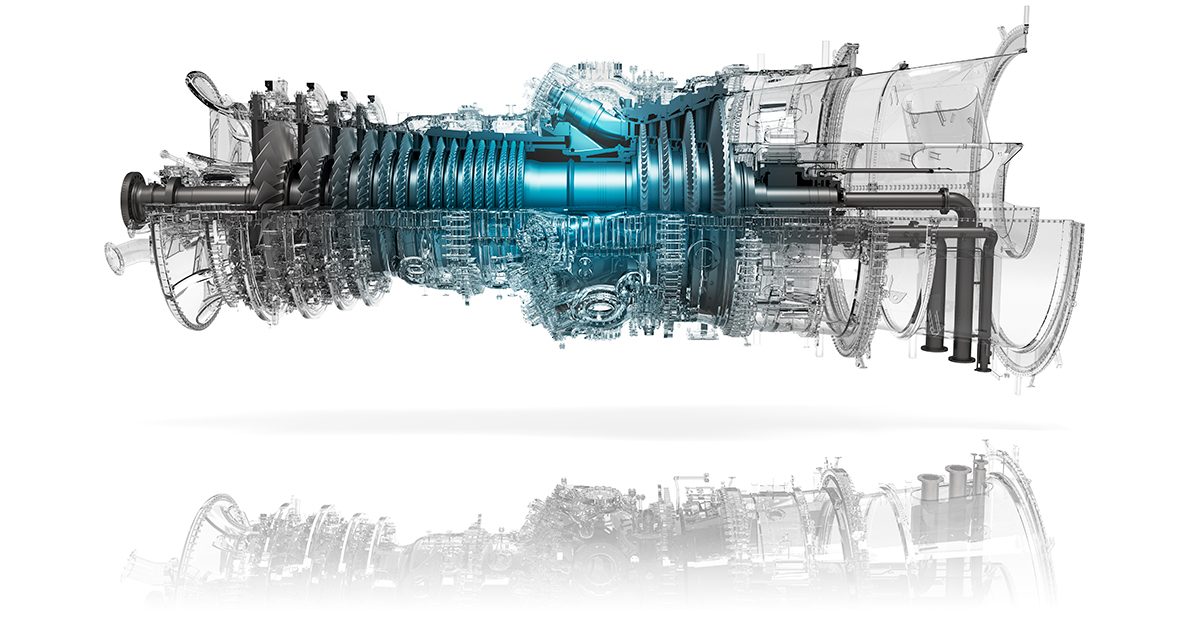
Resolving these issues means developing solutions that allow hydrogen and air to mix efficiently and ensure stable combustion.
“In order to mix hydrogen and air in a short period of time, it has to be done in as confined a space as possible,” explains Satoshi Tanimura, Chief Engineer, General Manager at Mitsubishi Power’s Gas Turbine Technology & Products Integration Division.
“The problem is that in this case the fuel nozzle jets and flame are in closer proximity, making flashbacks increasingly likely.”
The solution could lie in dispersing the turbine’s firing flame and reducing the particle size of the fuel spray that the flame ignites to power the turbine.
“The key technology to this method is the fuel delivery nozzle,” adds Tanimura.“We upgraded the design, which normally features eight nozzles, and created the distributed lean burning, or multi-cluster combustor, which incorporates many nozzles.”
By reducing the size of the nozzle opening, injecting air and then spraying hydrogen, the air and gas mix can be achieved on a smaller scale, reducing the likelihood of flashbacks and keeping NOx emissions low.
Burning ambition
Mitsubishi Power has targeted 2025 to achieve 100% hydrogen-fueled turbines, a groundbreaking engineering feat allowing power plant operators with dual-fuel turbines installed to quickly migrate from today’s natural gas and 30% hydrogen mix. All with no major infrastructure modifications, no expensive plant downtime, minimal costs and no future CO2 emissions.
“Using the same equipment, power plant owners needing more natural gas today can be ready to use more hydrogen in the coming years,” says Browning.
Mitsubishi Power has multiple types of combustors catering to individual project requirements and hydrogen densities. At the heart of Mitsubishi Power’s hydrogen fuel technologies sits a multi-cluster combustor, which can be installed in any size of project to power large, medium or small gas turbines. Looking to the future, the company will develop a flexible gas turbine which can burn fuels with any mix ratio.
With such flexibility, dual-fuel turbines represent an important step along the road to decarbonizing power generation and help explain why hydrogen is challenging natural gas as the key fuel in a net-zero future.
Learn more about Hydrogen-Capable Gas Turbines
Related tags
