‘Controlling the chaos’: grid-friendly electric steelmaking
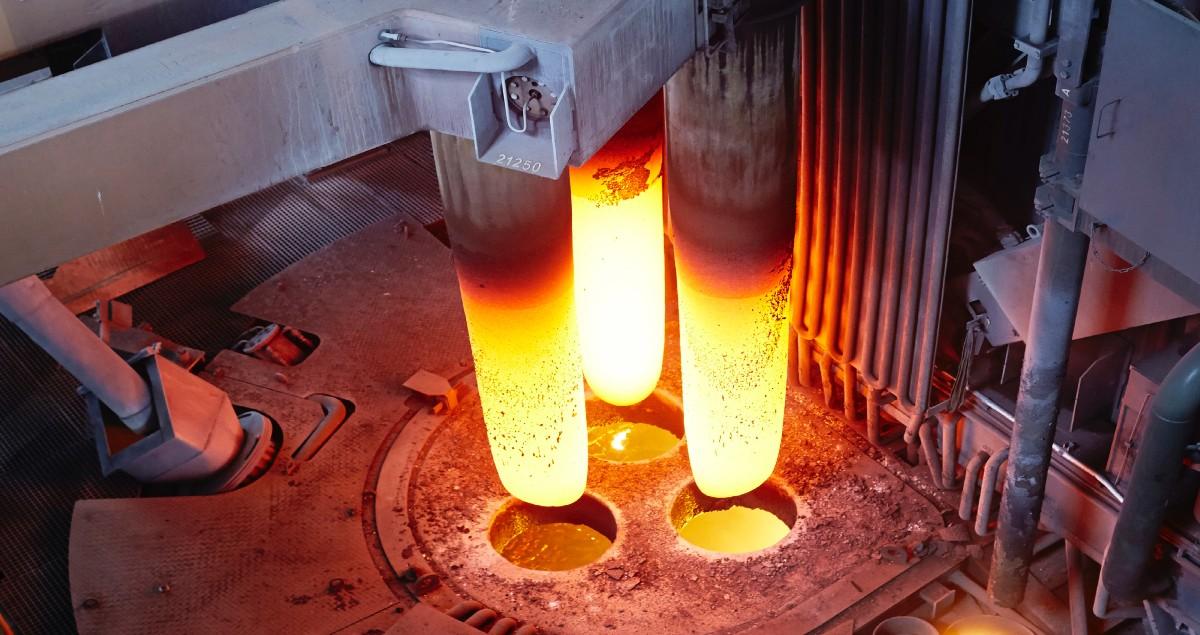
The electric arc furnace (EAF) may have been around for decades, but it is finally coming of age. The steelmaking technology accounts for almost 30% of global steel production. Last year, 43% of planned new steelmaking capacity was based on EAF technology, up from one-third the year before.
This increased take-up is being driven by the fact that more than 70% of coal-fired blast furnaces will require major refurbishment by the end of this decade, leaving steelmakers with a choice of relining the ones they have or switching to something new.
By melting down recycled or scrap steel instead of using coking coal to convert iron ore into steel, EAFs offer an appealing solution to a dirty problem. Demand for steel, a versatile material vital to the development of infrastructure and to the energy transition, continues to grow, especially in emerging markets. But the sector creates more CO2 than any other heavy industry and is responsible for between 8% and 10% of the world’s carbon emissions, according to the International Energy Agency (IEA).
EAFs are smaller, more flexible and cheaper to build than the blast furnaces traditionally used in steelmaking. What’s more, switching to making steel this way can reduce emissions by up to 80%.
However, EAFs come with their own set of challenges. The supply and quality of scrap is an issue, as is the cost of the electricity needed to power them. And there’s another significant problem — the impact on the grid of the sheer amount of energy EAFs consume to power their “violent” melting process, as well as the unpredictable nature of this power demand.
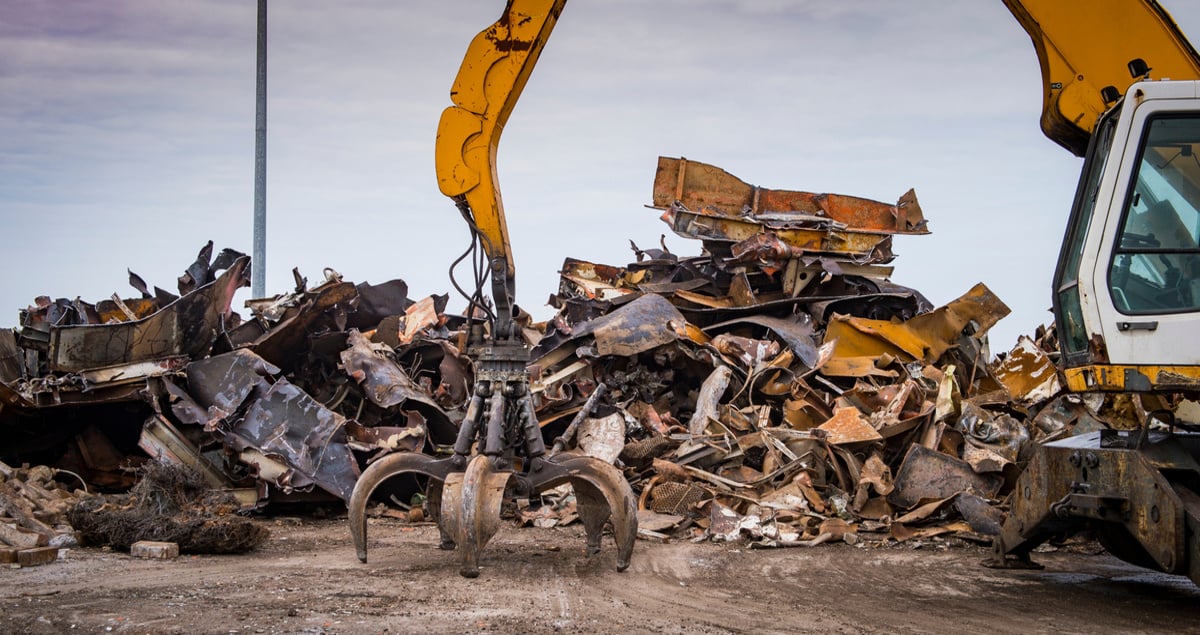
Managing EAFs’ efficiency and power demand
“An EAF is the worst machine that you can connect to an electrical power grid,” says Julian Magin, Head of Department, Electrification & Drives at Primetals Technologies, a Mitsubishi Heavy Industries (MHI) Group company. “It is so powerful, maybe up to 200, even 300, MVA [megavolt-amperes].” He adds that, with a standard nuclear power reactor producing around 1,500 megawatts (MW) of power, an EAF consuming that amount of power “is huge”.
Yet for the steel industry to cut its emissions in a scenario where the world reaches net zero by 2050, the share of production using EAFs will need to rise to more than half (53%) by that year, the IEA says. That could put a lot of extra pressure on the world’s already strained grids.
Magin is part of a team working on a technology that aims to help EAF steel producers improve efficiency while managing their demand on the grid: Primetals Technologies’ Active Power Feeder (APF).
Supporting a stable power grid
The APF is a power supply system specially designed for EAFs. It “decouples” the EAF from the grid and digitally controls the melting process to ensure it is dynamic, efficient and, above all, “very grid-friendly”, Magin says. This reduces power-on time and energy consumption, as well as helping to reduce stress and wear and tear on the electrical and mechanical components of the EAF.
The APF also supports and stabilizes grid voltage and frequency. A conventional EAF’s intense melting process creates an unstable electrical load that can result in issues including loss of the electric arc and voltage fluctuations.
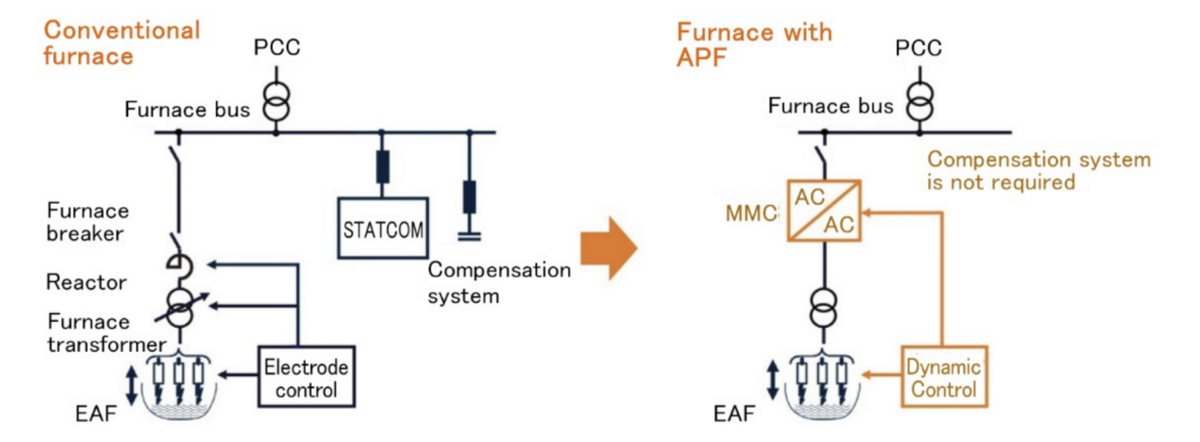
The APF compensates effectively for such power disturbances.
Torsten Buddenberg, Senior Project Manager for Low Carbon Technologies at Mitsubishi Heavy Industries EMEA describes this as “controlling the chaos” of the process.
“It’s an enabler of decarbonization in the sector,” he adds.
The future of green steelmaking
Primetals Technologies says the APF will be ready for operation in industrial settings by 2025, and the technology’s environmental, technical and commercial benefits for scrap melting with EAFs will be demonstrated through a collaboration with BGH Edelstahl. The German steel producer will test the solution at its 50-tonne EAF in Siegen, as it looks to continue providing its customers with high-quality stainless steel and special alloys while making significant cuts to its emissions.
Fully greening the sector, though, will require decarbonizing the process of making primary material. Here, green hydrogen-powered direct reduced iron (DRI) technology, used in conjunction with EAFs and automation and optimization technologies, would remove carbon from the steelmaking process.
The ultimate goal is “an electrification of the total process”, Buddenberg says. “But EAFs will be one of the main consumers of electricity — which means we will need to be very careful with the grid”.
The APF is suited to powering a wide range of arc furnaces, including both scrap- and DRI-based furnaces, according to Primetals Technologies, with large furnaces up to 300 tonnes and higher “on the APF roadmap”.
“We are starting projects with other customers with bigger solutions,” says Thomas Matschullat, Senior Expert at Primetals Technologies. “Our idea is to transport the results of our pilot plant to other plants — we have a huge field to play with and make radical innovations.
“We have an extremely good development team, not only on the electrical side but also on the process side. We have many people from the mechanical department who are very familiar with operating electric arc furnaces. We are a big team with a lot of ideas on how to make the best technology possible.”
Learn more about Primetals Tehnologies' Active Power Feeder
Related tags
