Green steel: Why this is a make-or-break decade
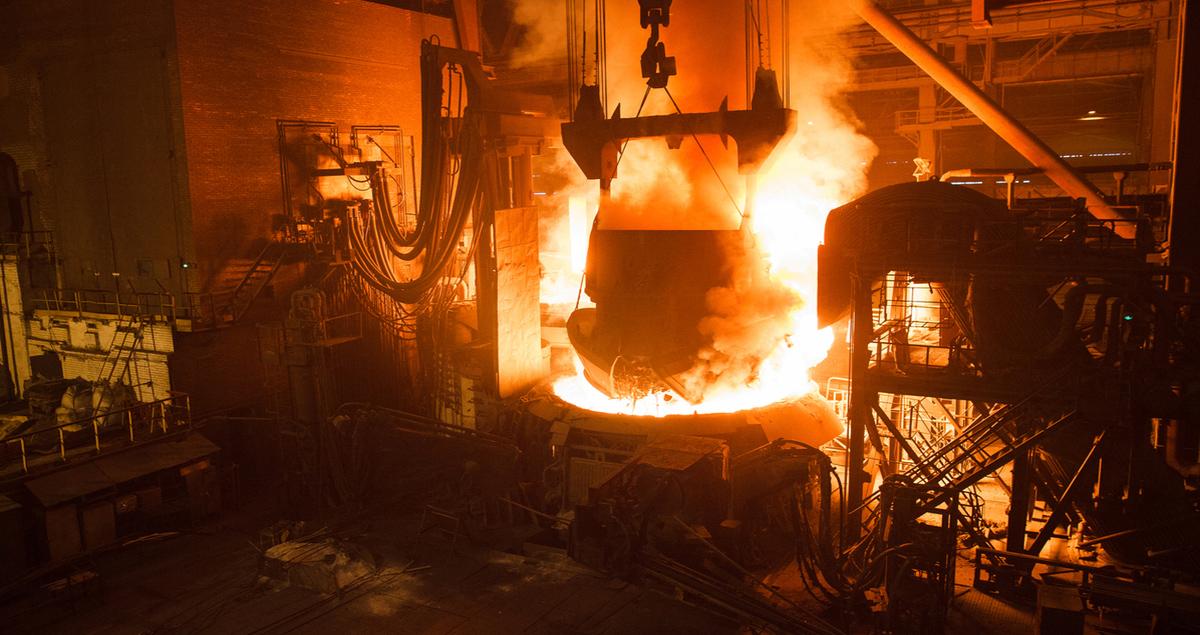
Look around you. Steel is seldom far from our daily lives, but steelmaking is coming to a crossroads where a wrong turn could be costly.
Much of the world’s existing steelmaking infrastructure is fast becoming obsolete: 71% of blast furnaces — which are coal-fired — will require major refurbishment (“relining”) by 2030, according to a new International Renewable Energy Agency report. The question is … what comes next?
Investors in this hard-to-abate sector must choose between refurbishing existing furnaces that run on fossil fuels, or rethinking their production routes and switching to electric arc furnaces (EAFs) that offer a path toward producing emissions-free “green steel”. However, what appears to be a simple choice isn’t so straightforward.
Here are some of the factors that could determine whether the next few years turn into the decade of green steel — or at least greener steel.
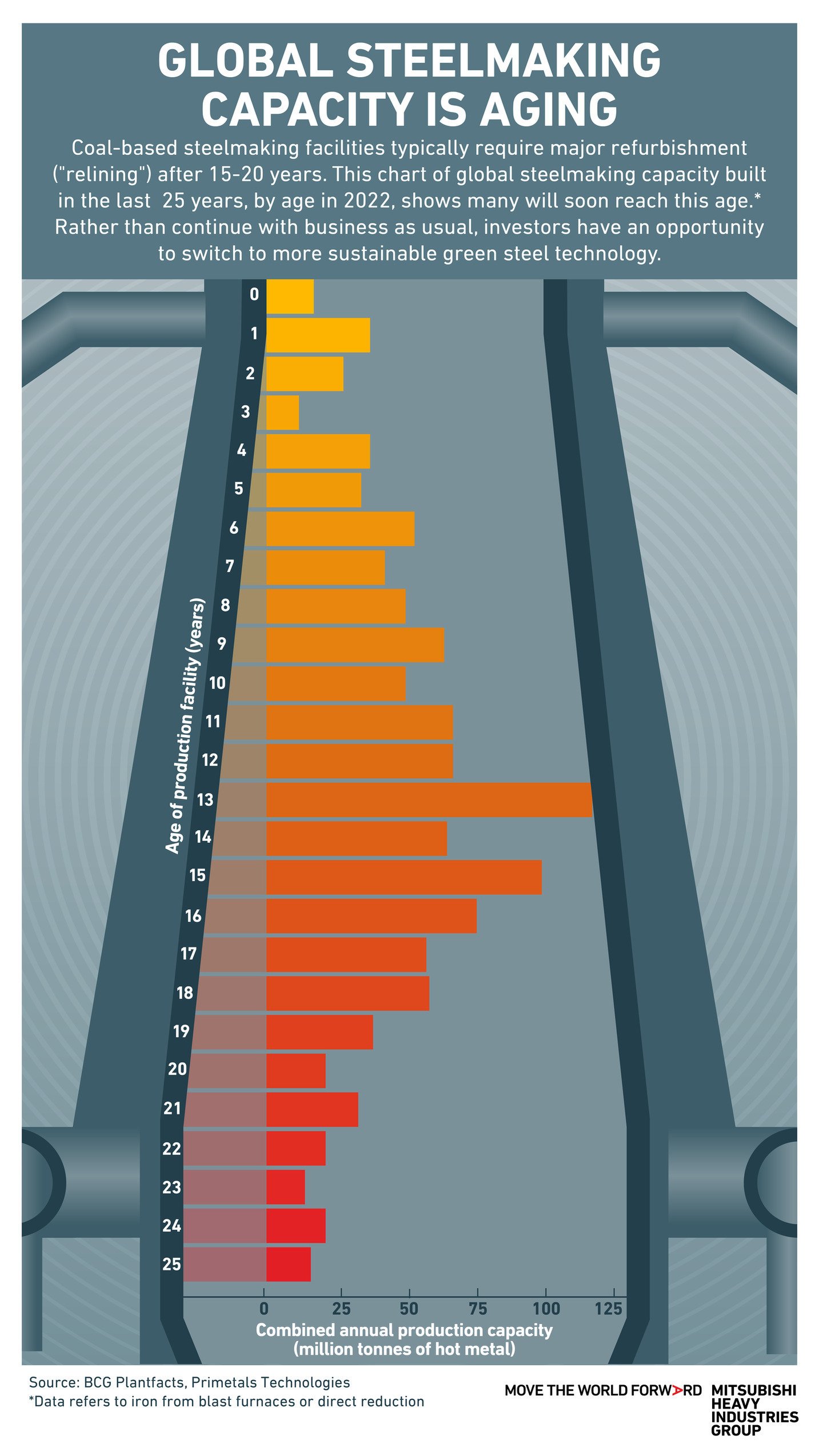
An investment dilemma
Infrastructure investment decisions are rarely simple.
Replacing heavy-polluting coal-fired blast furnaces with low-emission EAF technology fueled by electricity offers the industry a chance to clean up its act. But will investors buy into the promise of sustainable green steel when the market for this premium product is still in its early stages?
Many countries have already announced plans for new coal-fired furnaces, according to a Global Energy Monitor report, but investors could face jeopardy here too.
First, coal is a commodity with a global price tag, whereas the price for electricity to power EAFs is set regionally, which changes the business case significantly.
Also, building steelmaking infrastructure is a costly business, and these investments don’t yield returns for long periods. As momentum intensifies to shift away from fuels like coal due to carbon pricing schemes and looming carbon border taxes on traded products, fossil fuel furnaces and other infrastructure are at risk of becoming stranded assets.
The global steel industry could have to write off between $345 billion and $518 billion in stranded fossil fuel assets in the coming years, the report estimates, supporting the case for decarbonization
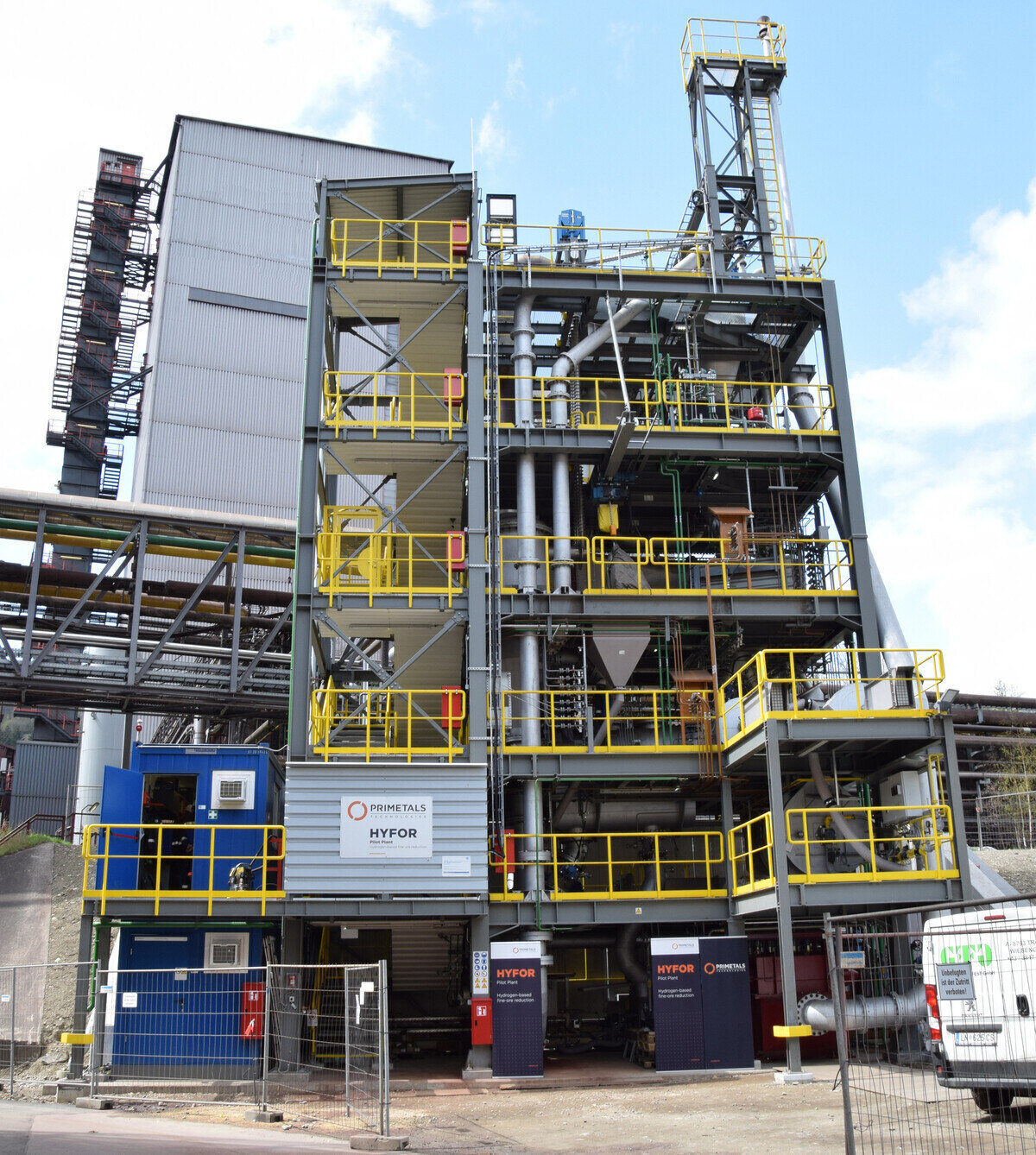
Emerging steel markets
Another key factor is global demand for steel, which is projected to increase 30% by 2050, with resource-hungry emerging economies responsible for much of that growth.
Around 80% of the world’s new coal-fired steelmaking capacity is located in the emerging economies of China and its neighbors in Asia, which could leave them locked into carbon-based production for decades.
Heavy reliance on coal-based steel could also expose these emerging economies to the risk of their steelmaking assets becoming stranded.
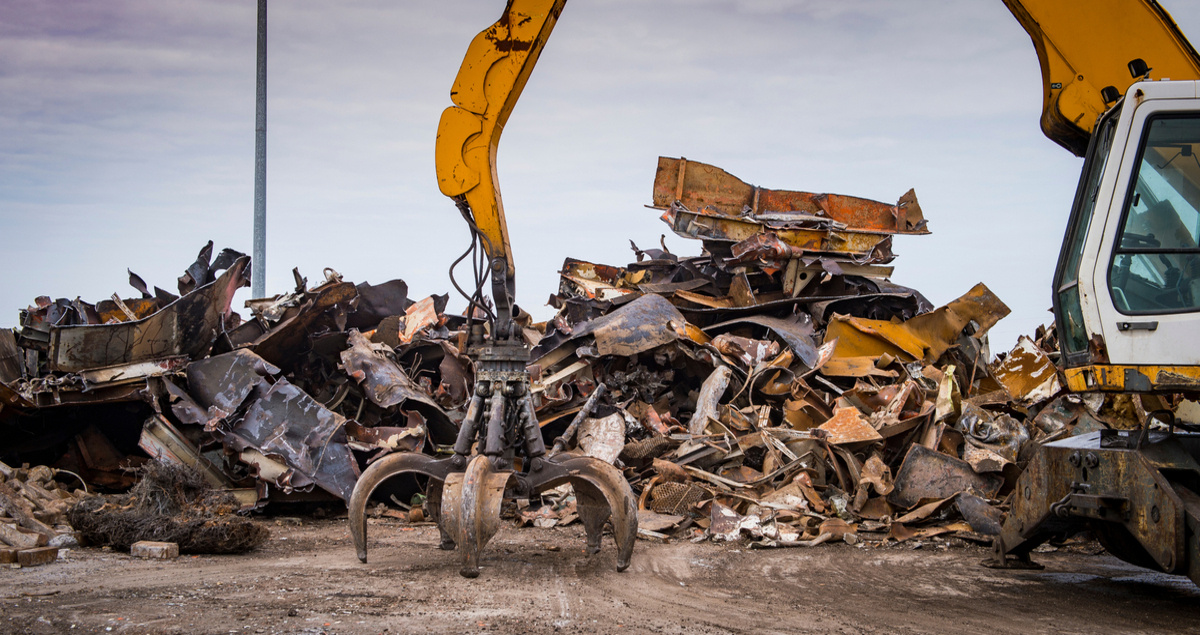
Low-carbon steelmaking solutions
Innovation is another factor driving many aspects of the energy transition and steelmaking is no exception. New solutions are being developed to ease the steel industry’s transition to a more sustainable future.
Primetals Technologies, a Mitsubishi Heavy Industries (MHI) Group company, has developed its HYFOR® direct reduction pilot plant for iron ore fines at a site of Austrian steel producer Voestalpine. The process uses 100% hydrogen as a reduction agent, reducing CO₂ emissions close to zero. The company has also unveiled a new type of electric furnace called Smelter, to efficiently turn the resulting iron to steel.
Meanwhile a group of the world’s biggest manufacturers have formed the SteelZero initiative, using their collective purchasing power to demand lower-carbon steel in an effort to reach 100% net zero steel by 2050.
Efforts to expand the use of EAFs can help recycle the world’s waste steel. But while this technology emits a fraction of the carbon dioxide associated with mainstream steel production, supplies of scrap steel are limited and purely scrap-based EAFs cannot always produce the high-quality steel needed for applications such as car production.
Alongside EAF technology, the hunt is also on for a more sustainable way than coal-fired furnaces to achieve the extreme temperatures needed to produce new steel.
An uneven pitch
However, while all these innovations could help kickstart the market for green steel, global adoption will likely be uneven.
Regions such as the US, Australia, the Middle East and North Africa will have greater access to the clean hydrogen made from renewable sources that is needed to produce sustainable steel. And countries like China and India that have invested heavily in traditional blast furnaces need these investments to pay for themselves over the coming decades.
Sustainable steel also commands a premium price, so establishing a market will depend on having the right policy and investment framework in place to encourage uptake — while also ensuring that current steelmaking assets do not become stranded. Yet despite the premium price tag, sustainability is becoming an important aspect of buying behavior.
Cleaning up one of the world’s most CO₂-intensive industries may be a challenge, but with the right support, green steel could help deliver on its potential.
Discover more about Primetals Technologies’ HYFOR hydrogen-based direct reduction technology
Related tags
