The three phases to green steel production
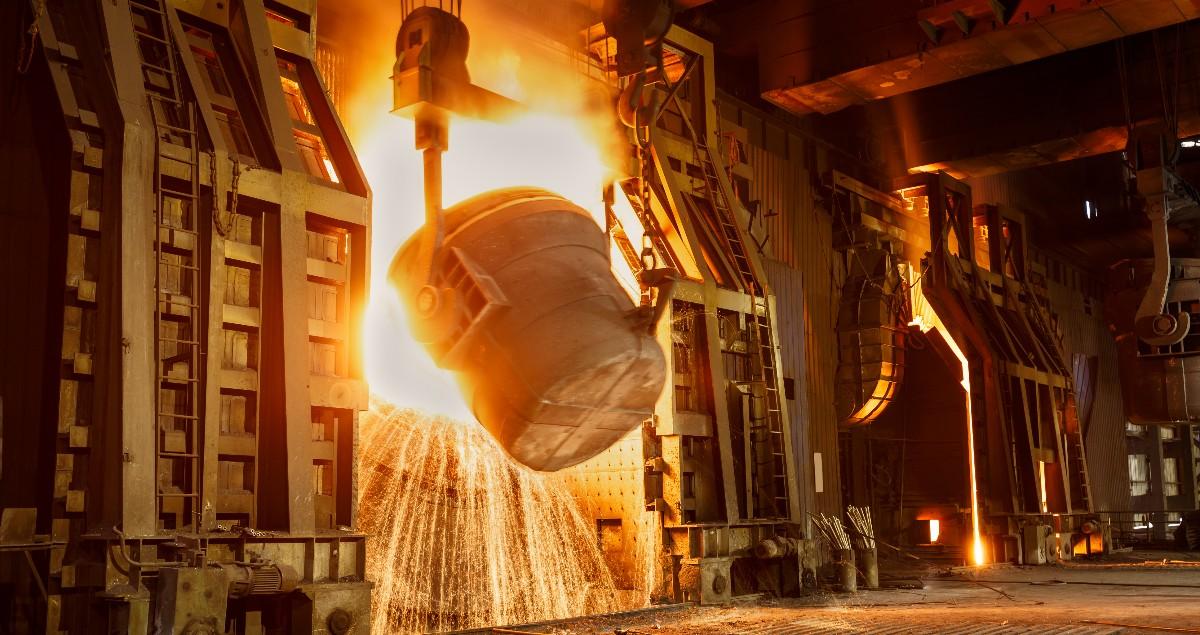
The original version of this article, published by Primetals Technologies, an MHI Group company, may be found here: https://magazine.primetals.com/2023/06/12/three-phases-to-green-steel/
Steel is a highly sustainable product that is nearly infinitely recyclable and crucial to the infrastructure necessary for developing industries, including e-mobility and renewable energy. However, the CO2 generated by every ton of crude steel production is nearly double that of the steel produced. Overall, the iron and steel industry is responsible for 7-10% of global carbon emissions.
As a result, the sector must fundamentally change how metals are produced, with sustainability principles at the core of the process, supported by new technologies, clean energy sources and the application of artificial intelligence. Green steel is the term that has come to embody this global transformation of the metals industry.
With demand for eco-friendly production coinciding with a steady increase in underlying steel demand, a premium price for green steel will emerge, helping to fund the transformation of production routes and creating a sustainable industry.
However, this transition will not occur overnight; the experts at Primetals Technologies see the transition in three phases.
The optimization phase
Developed over 70 years ago, the basic oxygen furnace (BOF) revolutionized the steel industry. Today, the blast furnace (BF) and BOF route comprise approximately 70% of worldwide steel production. However, producing one ton of steel this way generates almost two tons of CO₂ emissions.
The good news is that readily available technologies can reduce these emissions by 25-40% while increasing yields and reducing maintenance costs and waste. For the blast furnace, these technologies range from blowing more oxygen into the BF to increase combustion efficiency to recovering heat via specialized ‘top gas recovery’ turbines.
Leveraging steel’s recyclability, increasing scrap use is a clear focal point throughout all phases toward green steel Primetals Technologies has developed ‘crafted scrap’, a means of leveraging tracking sensors and AI-powered tools to ensure a well-sorted and refined batch of scrap is delivered to the melting units.
Scrap use does come with additional hurdles, but pre-heating scrap, usually to around 800˚C, can increase the amount a BOF can process from around 15% to 20%. Adding technologies like a bottom-blowing converter can raise the scrape rate to 30-50%, reducing CO₂ emissions by almost two fifths.
Digitalization is another way to boost efficiency, from measurement technology to data management. A network of sensors creates a ‘digital orchestra’, where each part of the steelmaking process interacts in perfect harmony.
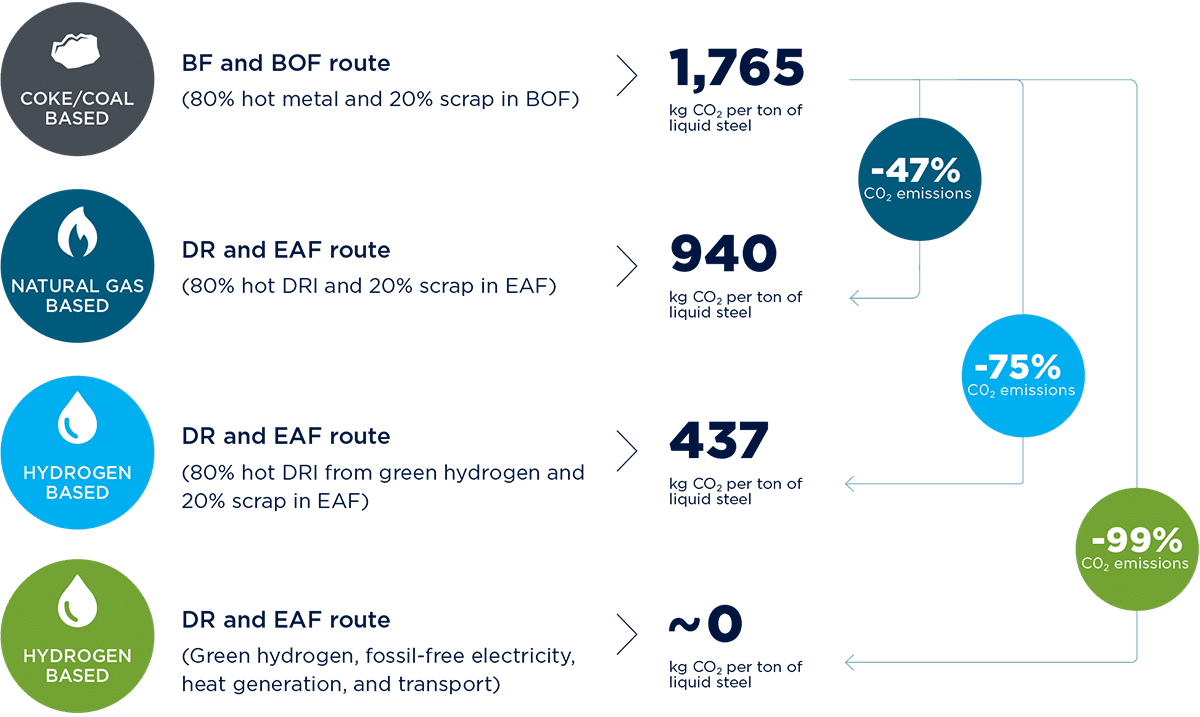
The transition phase
Meanwhile, new technologies are emerging at an auspicious time. With about 70% of all BFs worldwide requiring relining by 2030, producers have a near-term opportunity to shift toward two key innovations: direct reduction of iron ore (DRI) and electrification.
The MIDREX direct reduction process has gained traction worldwide as a leading DRI process, with immediate benefits for the reduction of CO2 and the production of high-quality merchant hot-briquetted iron (HBI).
HBI is a valuable material since it can be easily transported, implemented in existing integrated steel plants and used in electric steelmaking. Moreover, a MIDREX plant operating entirely on natural gas significantly reduces overall emissions compared to a BF. Capable of 100% hydrogen operation, MIDREX plants can transition as the hydrogen economy expands.
For the most environmentally friendly means of steel production, switching from the traditional BF-BOF route to scrap-based electric steelmaking can ‘future-proof’ steel plants. The changeover is complicated, but investing in EAFs while continuing to operate existing assets in the meltshop allows steelmakers to sequence any necessary changes to plant logistics and maintain capacity.
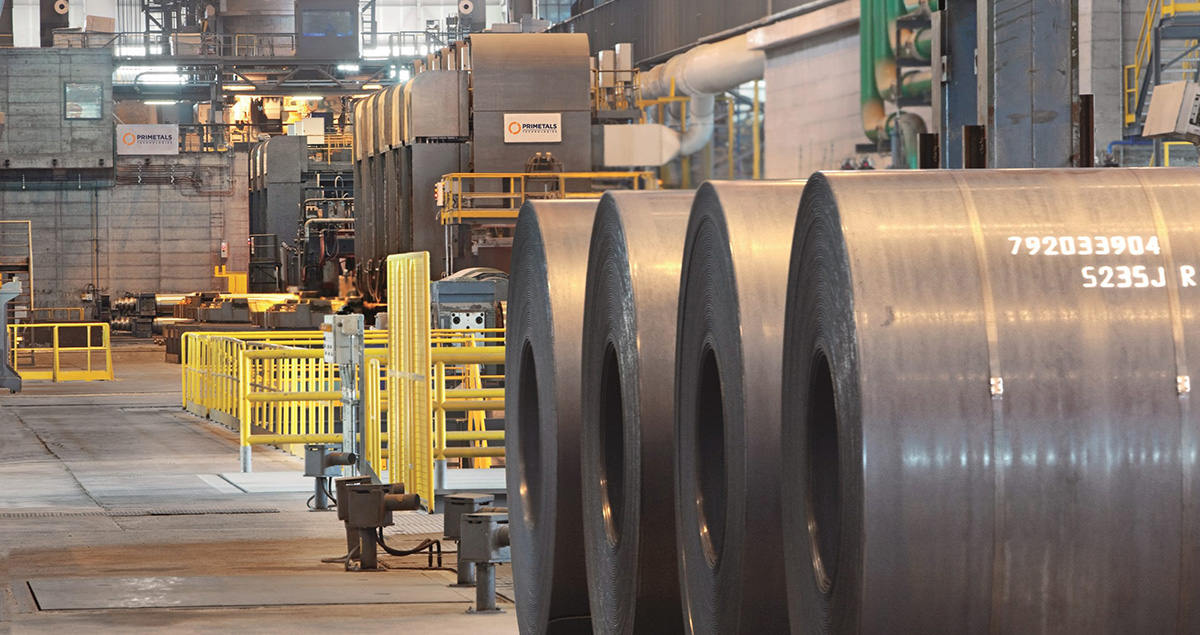
Beyond incorporating changes into the raw material value chain or the meltshop itself, downstream production processes, such as continuous casting and rolling present further improvement opportunities. Arvedi ESP, or endless strip production, allows producers to go from liquid metal to rolled end products in record time with less energy consumption and in an ultra-compact format, removing additional reheating steps.
Achieving green steel
The final step toward producing green steel is to eliminate carbon emissions.
For DRI solutions, this means using 100% hydrogen as the reducing agent rather than natural gas – with Primetals Technologies offering its HyREX and HYFOR technologies. Currently, in cooperation with voestalpine and the mining company Fortescue, Primetals Technologies is pre-engineering an industrial-scale demonstration plant in Linz, Austria, expanding on the success of the HYFOR pilot plant to produce green pig iron from iron ore fines.
Simultaneously, producers are already focused on incorporating hydrogen production into their plant infrastructures, such as H2Future: a pilot facility to test the application of hydrogen in steel production, located at voestalpine’s steelworks in Linz.
With the expansion of electrification, powering EAFs with renewable energy can effectively eliminate all emissions from this portion of the steelmaking process. However, rapid growth in the renewables sector required to supply the power the steel industry would require will require vast amounts of steel.
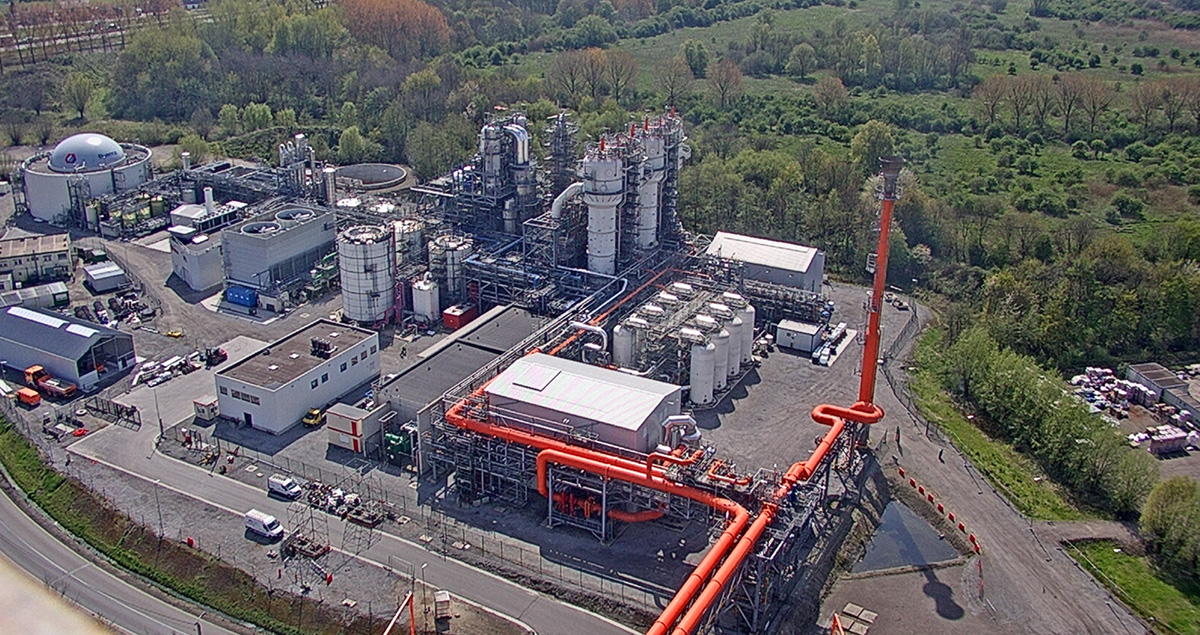
Recognizing that some producers may be slower to transition to a zero-carbon production route, producers are also focusing on recycling previously wasted carbon emissions through carbon capture technologies. Partnering with LanzaTech, Primetals Technologies has helped to establish a gas-fermentation “Steelanol” plant at ArcelorMittal’s facility in Gent, Belgium, recycling blast-furnace waste gas into bioethanol.
Converting waste into valuable by-products, recovering raw material, contributing to the circular economy, and becoming a flagship zero-waste carbon-neutral industry—the future of sustainable metals is defined by green steel technologies that are reshaping global steel production.
Learn more about green steel In Primetals Technologies' Metals Magazine
Related tags
