The large heat pumps transforming gas-intensive industries like pulp and paper
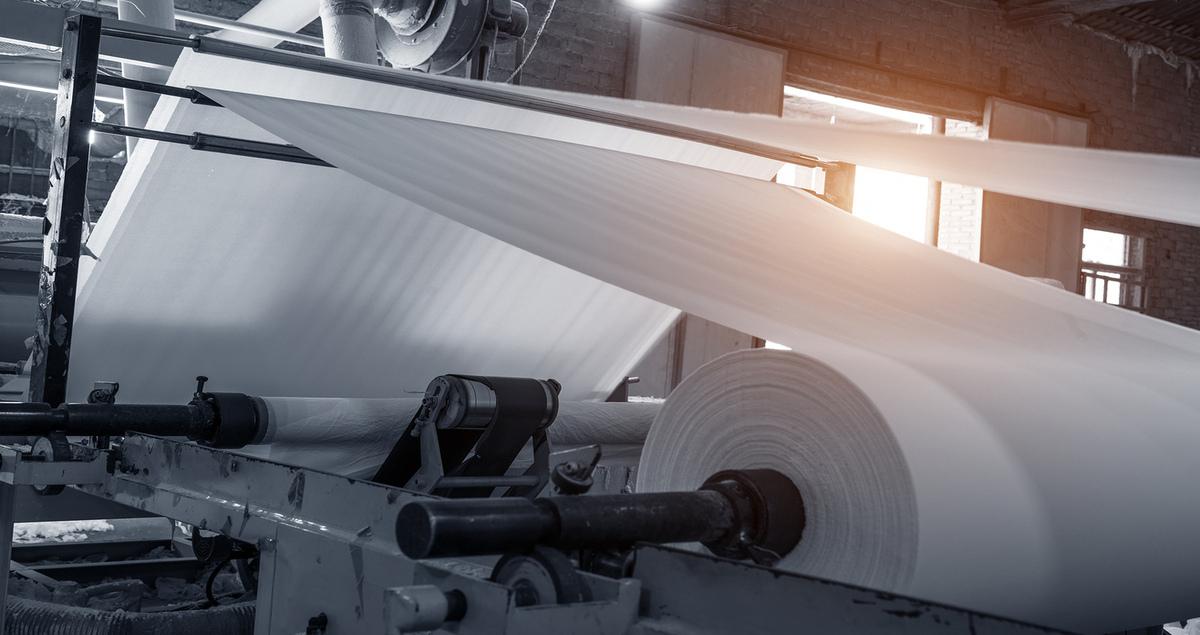
In an increasingly digital world, our growing reliance on screens is an ominous sign for paper manufacturers, as newsprint, writing and printing paper use decline. However, demand for lower-grade wrapping, packaging and household paper continues to expand, increasing by 2% annually.
Pulp and paper production accounted for 2% of global CO₂ emissions from industry in 2021 and production is expected to keep increasing to 2030, according to the International Energy Agency (IEA), which raises important questions about the industry’s long-term sustainability.
That’s where heat pumps come in. Forward-thinking equipment manufacturers are supersizing the conventional heat pump designs used in domestic households, to help decarbonize gas-intensive industries like pulp and paper.
Pulp faction
Paper production requires intense heat to evaporate large amounts of water in the drying process: heat that could be reused rather than wasted. Drying represents more than two-thirds of the energy used in papermaking.
Scaling up heat pump technology enables paper manufacturers to harness large quantities of low-temperature residual heat from production and repurpose it for use at high temperatures for the drying process.
Mitsubishi Heavy Industry (MHI) Group company, Turboden, has signed a contract with a leading European company in the pulp and paper industry to create a bespoke large heat pump (LHP) with capacity to generate high-temperature steam without CO₂ emissions in the production process.
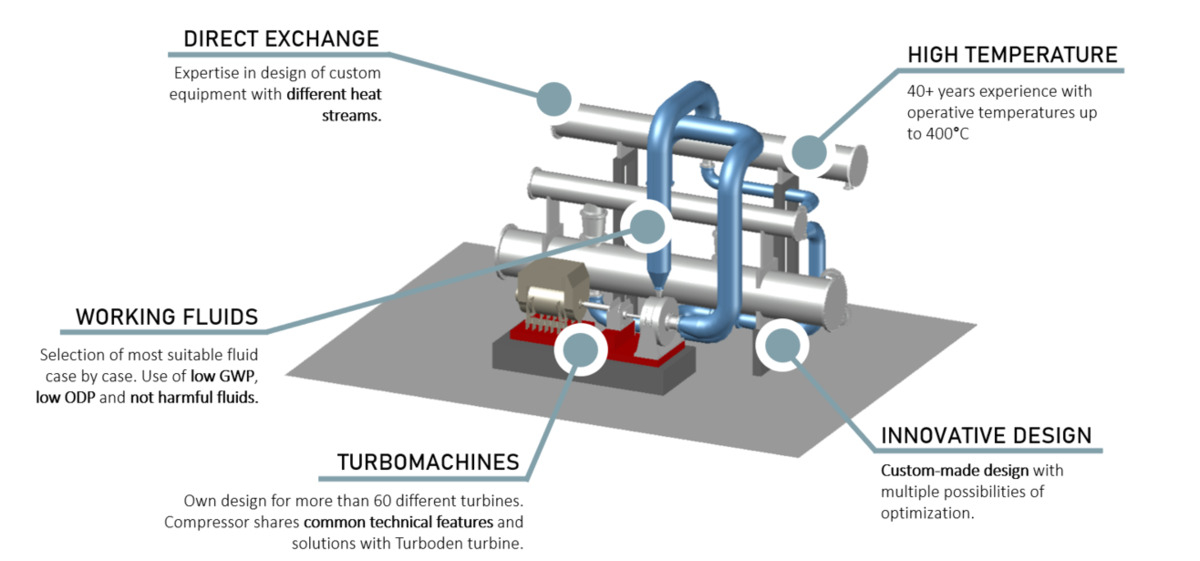
Using refrigerant liquid, Turboden’s LHP technology will integrate with a mechanical vapor compressor to turn low-grade heat ranging between 10-12°C into superheated steam of more than 200°C that is needed to produce paper.
The LHP transfers thermal energy from the low temperature heat source into a heat exchanger, turning a natural refrigerant liquid into gas. The compressor conveys energy to the gas, causing its temperature and pressure to increase further. Heat from the pressurized refrigerant gas is then released ready to be utilized to heat the condensate into superheated steam, while leaving the refrigerant to return to liquid form as it cools further by depressurizing, ready for the cycle to begin again.
The project is also a meeting of minds between two MHI Group companies, bringing together Turboden’s industry know-how and Mitsubishi Heavy Industries Compressor Corporation’s expertise and experience, to develop a cleaner and more efficient heat provision system.
The combination of these two technologies would help the European pulp and paper company reduce as much as 23,200 tons of CO₂ annually from its heating process.
Halving industrial energy needs
For gas-intensive industries like pulp and paper, combining LHP and steam compressor technologies provides an efficient way to reduce the industrial greenhouse gas emissions associated with thermal power production. These two technologies could more than halve the energy used to dry paper, the EHPA/Cepi working group report says.
Alternative efforts to make papermaking more energy efficient also focus on improving the paper drying process. A consortium of technical universities in the Netherlands is working to develop non-thermal water removal technologies based on electric forces, the IEA notes.
Research is also underway in Germany and Scandinavia to develop methods of papermaking without using water, although there is some way to go to deploy such solutions at scale.
The potential of heat pumps in other industrial sectors
Currently, heat pumps provide about 10% of final industrial energy demand in regions like Europe, according to a joint European Heat Pump Association (EHPA) and Confederation of the European Paper Industries (Cepi) working group. This is helping to increase energy efficiency and lower emissions across many industrial sectors by reducing reliance on fossil fuels.
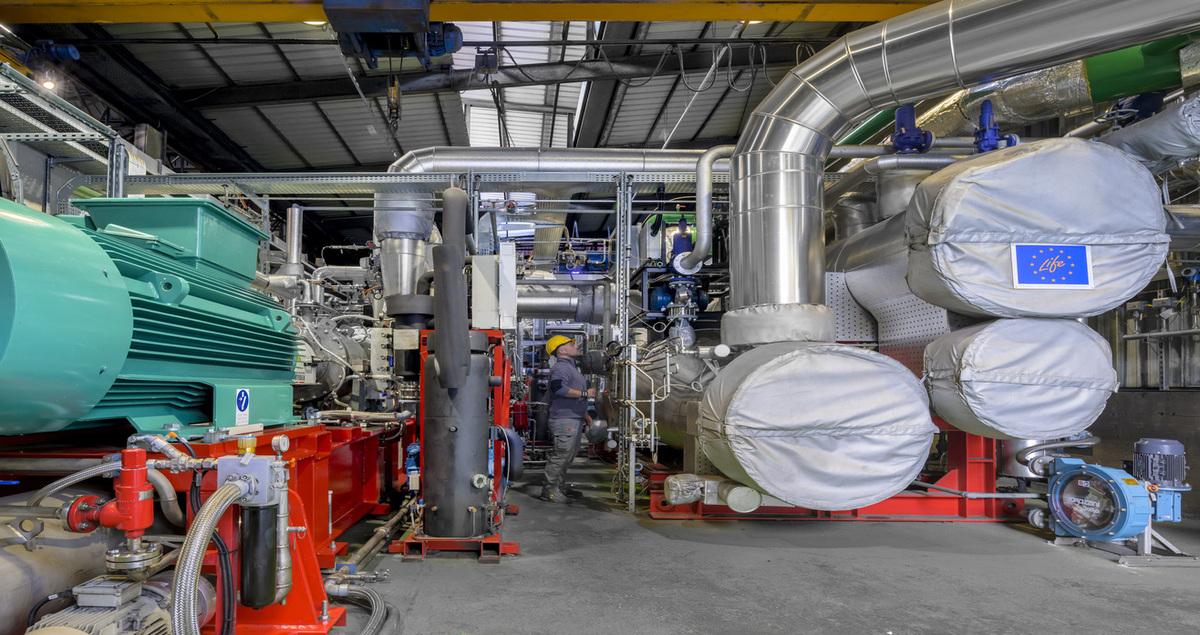
Steelmaking is another heat-intensive, hard-to-abate industry, where recycling waste heat can produce huge efficiency gains and emissions reductions. Turboden is also working on another project developing an LHP solution for Ori Martin in the Italian steel industry. Turboden created a LHP solution for the Ori Martin steel manufacturing plant in the northern Italian region of Lombardy. The large heat pump solution transforms low-temperature residual heat from the electric arc furnace’s cooling circuit into pressurized water, which powers the nearby city of Brescia’s district heating network.
Volatile natural gas prices, the global quest for sustainability to combat climate change, advances in technology and other factors, are combining to generate a lot of excitement about the future potential of sustainable and efficient LHP solutions.
Discover more about MHI’s large heat pump technologies
Related tags
