The history of the world’s fastest box-making machine
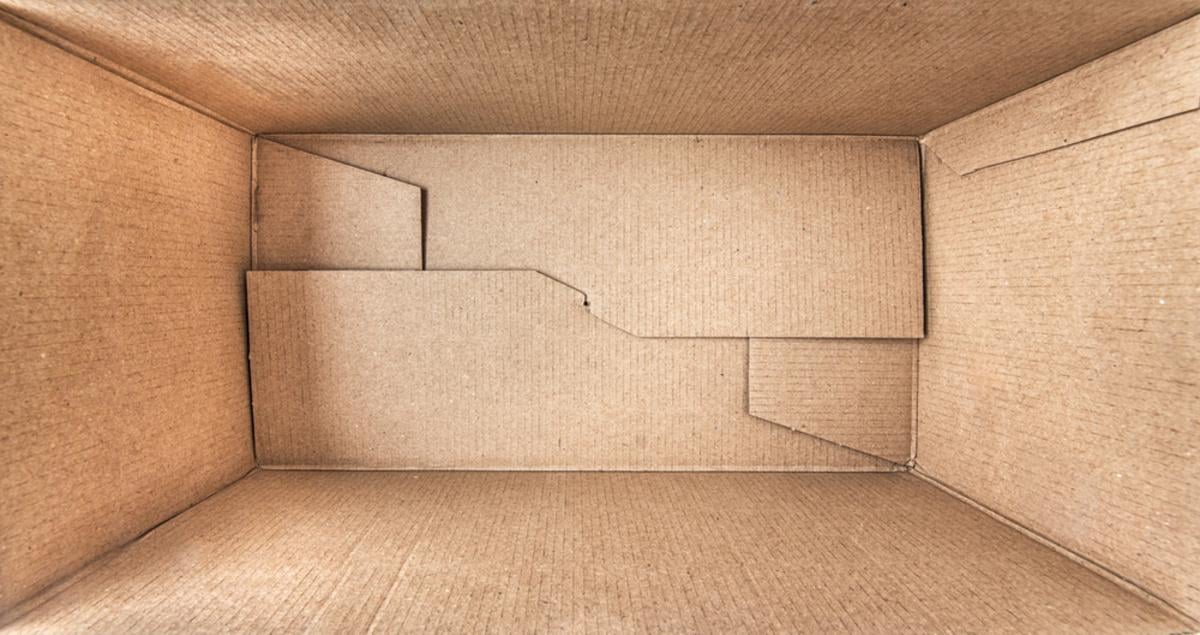
Lightweight, sturdy, easy to use and recyclable, the humble cardboard box is back in fashion.
The meteoric growth of online shopping has seen a surge in demand for boxes made of cardboard — or “corrugated cardboard” to use its proper name. Global e-commerce revenue has more than doubled in the past five years and is on a similar growth trajectory for the next five.
One thing is clear, greater reliance on home delivery will require boxes and lots of them.
Here we look back at the origins and evolution of the box-making machines that are vital to help meet growing online retail demand.
Back to basics
Ever wondered how box-making machines work? Flat corrugated sheets are fed into the machine, printed, creased and slotted, then glued and folded into boxes, and ejected in bundles at the other end.
Industry pioneer Mitsubishi Heavy Industries Machinery Systems (MHI-MS) has been developing this technology since the mid-1950s and currently manufactures the world’s fastest machine.
In the 1970s, this innovation proved a game-changer. Until then, multiple box-making machines were connected to a single motor operating at slow speeds and output. The machines furthest from the motor produced poor box-cutting accuracy so the boxes produced didn’t fit together properly when built.
MHI-MS was one of the first to introduce direct-drive servo motors that powered single units of the machine, so different units could be run at different speeds.
“Direct drive motors increased the accuracy of box-making machines, which could now run at higher speeds to produce higher volumes and better-quality boxes in different sizes,” explains Giovanni Bettini, Head of Sales for MHI EMEA Corrugating and Printing Machinery Division.
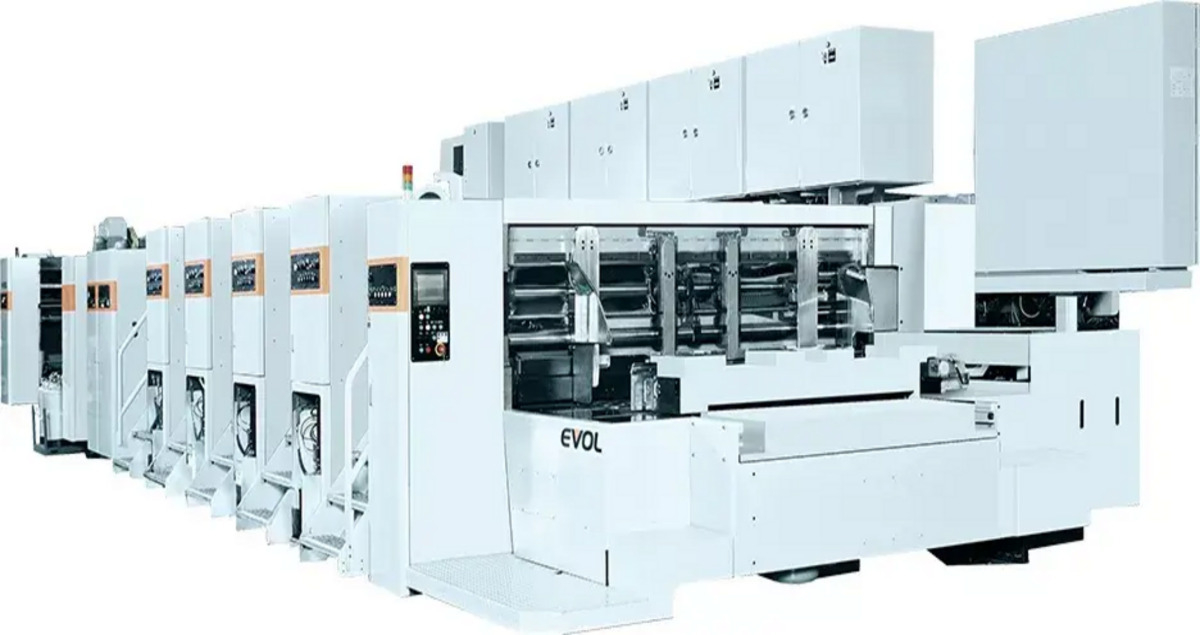
Thinking outside the carton
In 2003, MHI-MS released its first EVOL corrugated box-making machine, which has developed into an industry game-changer.
Not only is EVOL the world’s fastest, but it also operates reliably at very high speeds with precision folding accuracy that produces top-quality boxes. As most modern-day boxes are erected by a machine as part of an automated process, fit accuracy is vital.
One machine can produce 350 boxes per minute or 21,000 per hour. Think about that number for a second. What if you could double the output?
Using MHI-MS’ pioneering dual slotter unit, giant corrugated sheets can process two boxes simultaneously and cut the sheet in two, with a maximum hourly capacity of 42,000 boxes.
“Customers do not need to have two different machines, because this EVOL can do the job of two competitor machines,” says Bettini.
It is also kinder to the environment, reducing average annual ink loss by more than 10 tonnes and average annual washing water volumes by more than 750 tonnes compared to conventional designs, research conducted at the company’s Mihara box-making facilities in Japan shows.
Replacing two lines with one EVOL machine also results in a 43% reduction in electricity consumption, the tests show. This equates to an annual reduction in CO₂ emissions of 147 tonnes, or the equivalent of planting 10,300 trees to absorb carbon dioxide from the air.
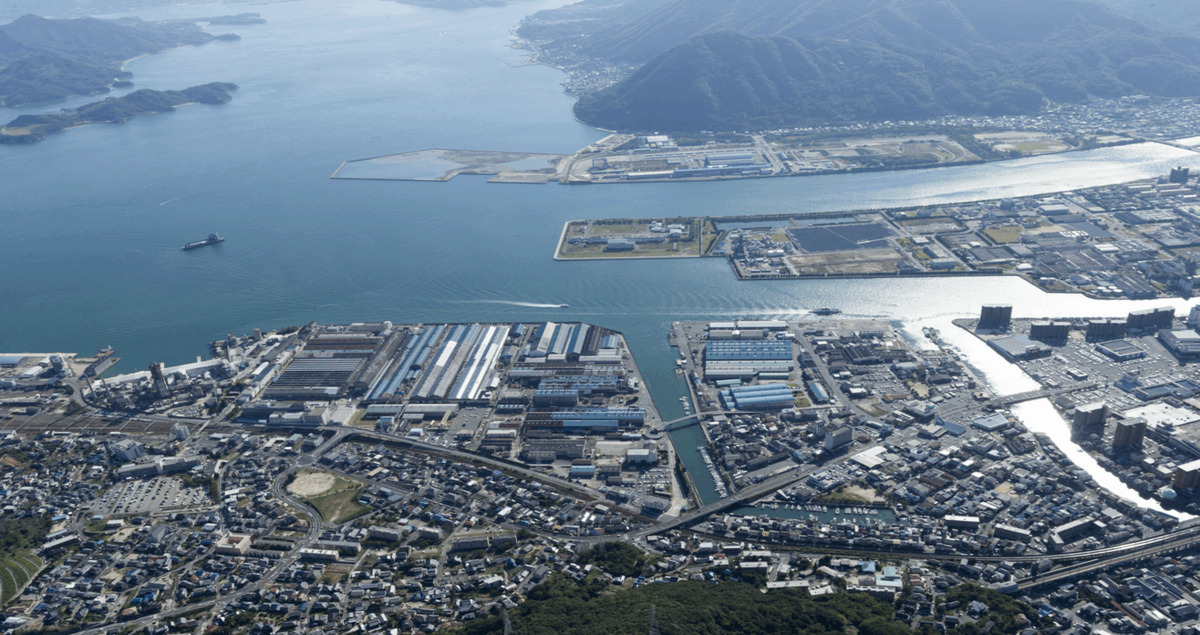
Sustainable future
This sustainability mindset extends beyond the machines themselves. The Mihara Machinery Works in Hiroshima is taking measures to achieve carbon neutrality with initiatives that include replacing fossil fuel power with on-site solar electricity to power all business activities.
As a result, it is expected to reduce 97.7% of its annual CO₂ emissions by the end of March 2024. And similar clean energy initiatives are in place at the company’s Amsterdam offices, which are already carbon neutral.
As the transition to online shopping gains momentum, the output of the box-making machines this industry relies on must keep pace and do so sustainably.
So, the next time a boxed order arrives at your doorstep, think about what goes on behind the scenes to make it possible.
Discover more about MHI’s industry-leading box-making technology
Related tags
