Swapping carbon for hydrogen, and how the steel industry can do it
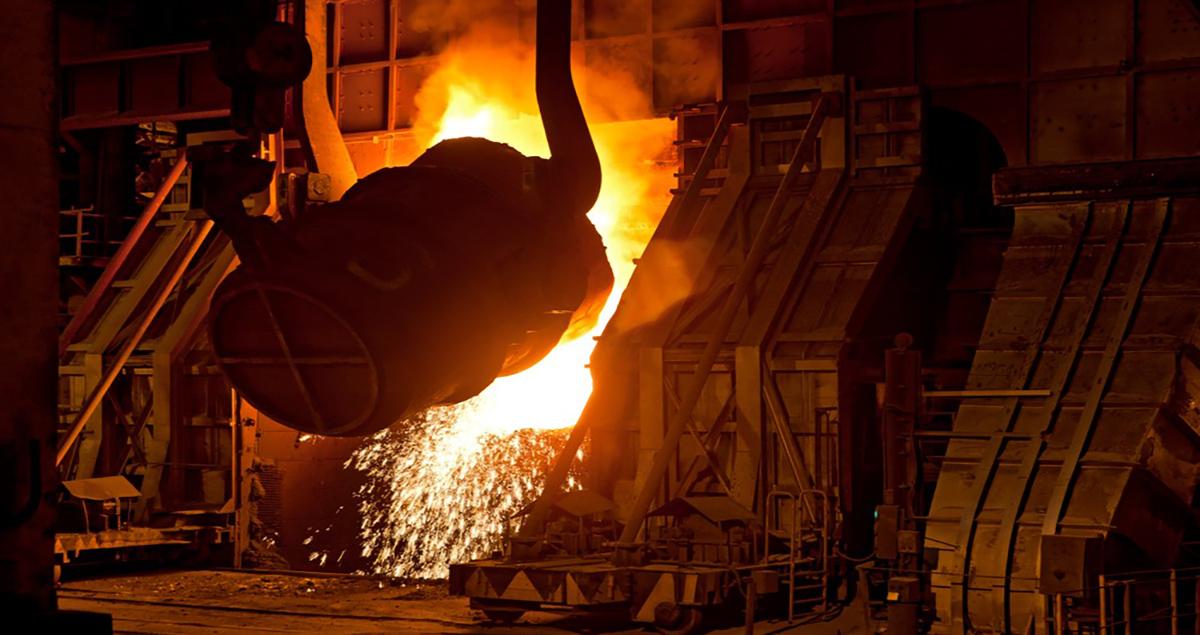
The steel industry’s biggest product today isn’t steel, as surprising as that may seem. It’s carbon.
Steel is a vital part of modern life – it’s indispensable in construction, machinery, transport and household goods. But iron, the base material of steel, has to be obtained from iron ore, which takes vast amounts of energy. And although other options do exist, today fossil fuels remain the only viable way to process iron ore at scale to get the iron needed to make steel.
To tackle this situation, steel makers around the world are racing to deploy new technologies aimed at reducing the sector’s carbon intensity. Such efforts include switching to cleaner electric arc furnaces, swapping coal for natural gas as a reduction agent, and converting carbon-rich waste gases into biofuels via carbon capture, utilization and storage (CCUS).
While these developments all have a role to play in boosting the industry’s green credentials, adopting hydrogen could be the key to a drastic reduction in its environmental impact.
Routes to a lower-carbon future
The rapid growth in steel production capacity over the past two decades has been driven by China. It is today responsible for half of global output and mainly uses the traditional processing route of coking plant, to furnace, to casting.
This type of steel production predates concerns about climate change and has a high carbon footprint, producing more CO2 than steel output.
“This integrated process generates a minimum 1.8 tonnes of CO2 per tonne of finished product,” says Dr Alexander Fleischanderl, Technology Officer and Head of ECO Business at Primetals Technologies, a part of Mitsubishi Heavy Industries (MHI) Group.
“Plants can run more efficiently, but many still run at three times or more of CO2 emissions for every tonne of steel produced. So unfortunately, the main product is still carbon.”
Switching to hydrogen as a fuel source can reduce the industry’s emissions: when burned, hydrogen’s only emission is water.
And according to Dr Fleischanderl, the steel industry is leading the way in demonstrating how a hydrogen-based society can be created.
Leading the charge
With the backing of the European Commission, steelmakers and their partners across Europe are investing heavily in hydrogen schemes.
Primetals Technologies, for example, is developing a process using hydrogen in place of coking coal as a reduction agent for iron ore. A pilot plant is being built at a production site of Austrian steelmaker voestalpine to test this new direct reduction process, and ensure it can directly reduce different types of ores found in various parts of the world.
Traditional direct reduction processes include an agglomeration stage to turn fine iron ore extracted from a mine into pellets, which is both energy intensive and requires a lot of capital. Once the iron ore pellets have been produced, they are transported from the mine to the steel production site.
Redefining this conventional wisdom, Primetals Technologies uses hydrogen as a reduction agent for iron ore direct from the mine. This eliminates the agglomeration step and much of the associated energy use and carbon emissions.
If the energy used to produce the hydrogen and refine the steel is generated by renewables, this could produce the world’s first zero-carbon iron.
“At the end, when green hydrogen is used it will for the first time ever result in completely carbon-free steel production,” explains Dr Fleischanderl.
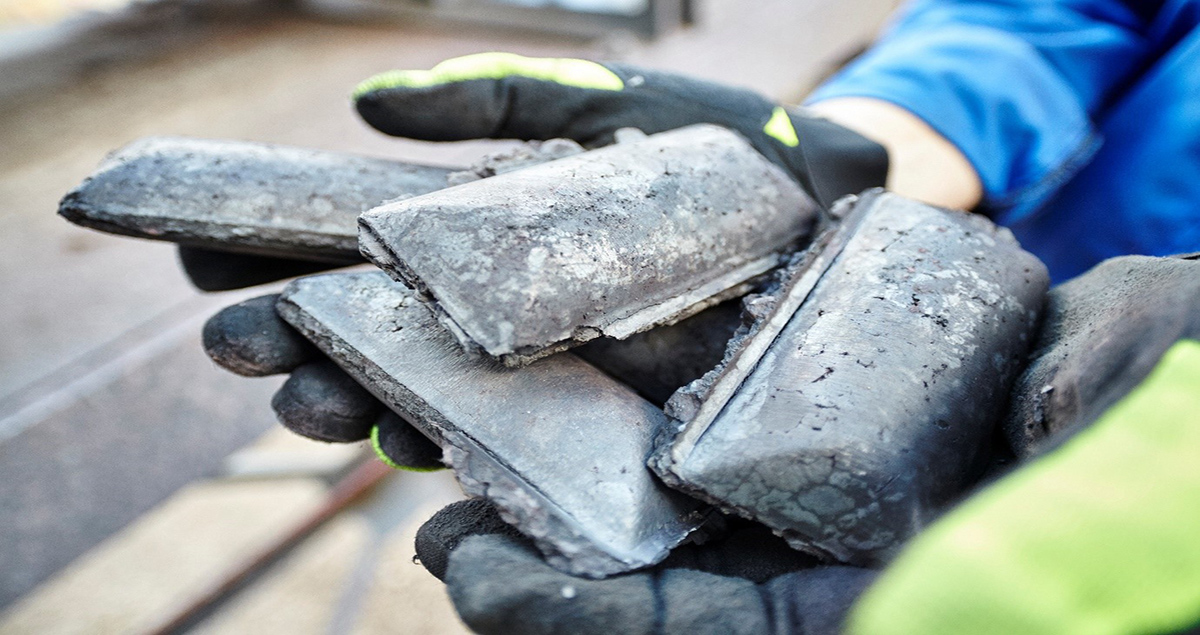
Meeting the challenge
However, establishing a ready supply of hydrogen that can make steelmaking truly carbon-free will be a major challenge.
One of the key barriers to overcome is the sheer volume of hydrogen needed to support a massive upscaling in use by the steel industry.
“Hydrogen could be the ultimate solution in many areas, such as metallurgy, energy transformation and mobility,” says Dr Fleischanderl.
“But the amount that will be consumed is tremendous. A steel mill converted from coal to hydrogen that produces 5 million tonnes of steel will require more than 44 tonnes an hour of hydrogen.”
Not only will vast quantities of additional hydrogen be needed to support the steel industry, but it will also need to be produced using alternative processes.
Currently, around 95% of hydrogen is “grey”, - that means it is produced by extracting gas from fossil fuels.
It is possible to use CCUS technology to prevent emissions being released into the atmosphere. But this only makes economic sense where a high volume of CO₂ can be captured at a single site. And it is only feasible in areas where there are geologically safe places to store captured carbon, such as beneath the sea or deep underground.
Clean emissions
The alternative to CCUS for carbon-free hydrogen production is electrolysis. This involves using electricity to split water into hydrogen and oxygen. If the energy that powers this process is from renewable sources, the end product is a carbon-free gas with water as the only emission.
To date, producing hydrogen through electrolysis has proven too costly to be competitive. But this is changing, as the boom in renewable energy sources, like wind and solar power, bring down global electricity prices. Generating hydrogen also provides a way to store excess energy when the wind blows or the sun shines during times of low demand. However, producing the vast quantities of hydrogen needed to power tomorrow’s steel industry, will require major investment in technology, supply chain capabilities and infrastructure.
And once enough of the gas can be generated, industry faces a second major challenge to transport it.
For example, in Europe, hydrogen produced by cheap electricity from solar power in the Sahara and wind farms in the north would need to be distributed to Central Europe. And although ships may be capable of transporting enough gas at the start, pipelines would ultimately need to be built to transport the huge volumes required to fuel demand.
A sustainable future
There is growing pressure on governments and policymakers to decarbonize their economies, which could provide a green light for investments in clean energy generating capacity, storage and transportation infrastructure.
Establishing a policy and financial incentive framework for adopting hydrogen is an essential part of the switch to a more sustainable future: it gives industry leaders confidence to invest in long-term hydrogen projects.
For example, the Asian Renewable Energy Hub plans to generate up to 15,000 megawatts of renewable energy from thousands of wind turbines and solar panels in Western Australia. This could generate 1.5 million tonnes of hydrogen each year, enough to produce 25 million tonnes of direct-reduced iron annually – equalling a quarter of today’s global production capacity.
In Europe, the Salcos project from Salzgitter AG, in Germany, and steelmaker SSAB, in Sweden, are using clean energy to power small-scale electrolyzers to generate green hydrogen for iron production.
Dr Fleischanderl says projects like these should encourage other industries to adopt hydrogen as a fuel source, providing an incentive for other steelmakers to follow.
At the moment these schemes are subsidized by the European Union and international funding schemes, as it’s in the clear interests of its member states to do this. But as global interest builds, the price of producing clean hydrogen should fall.
Just as industrial innovation has produced the technological capabilities to create a hydrogen economy, these same innovators are leading the charge to transform that opportunity into a reality.
Dr. Alexander Fleischanderl will be speaking at the Bloomberg New Energy Finance Summit in London between October 21-22 about the role of hydrogen in decarbonizing the ‘hard to abate’ sectors.
Read more in our report on the Energy Transition New Frontier for MHI Group
Related tags
