Shaping the future of the U.S. steel industry
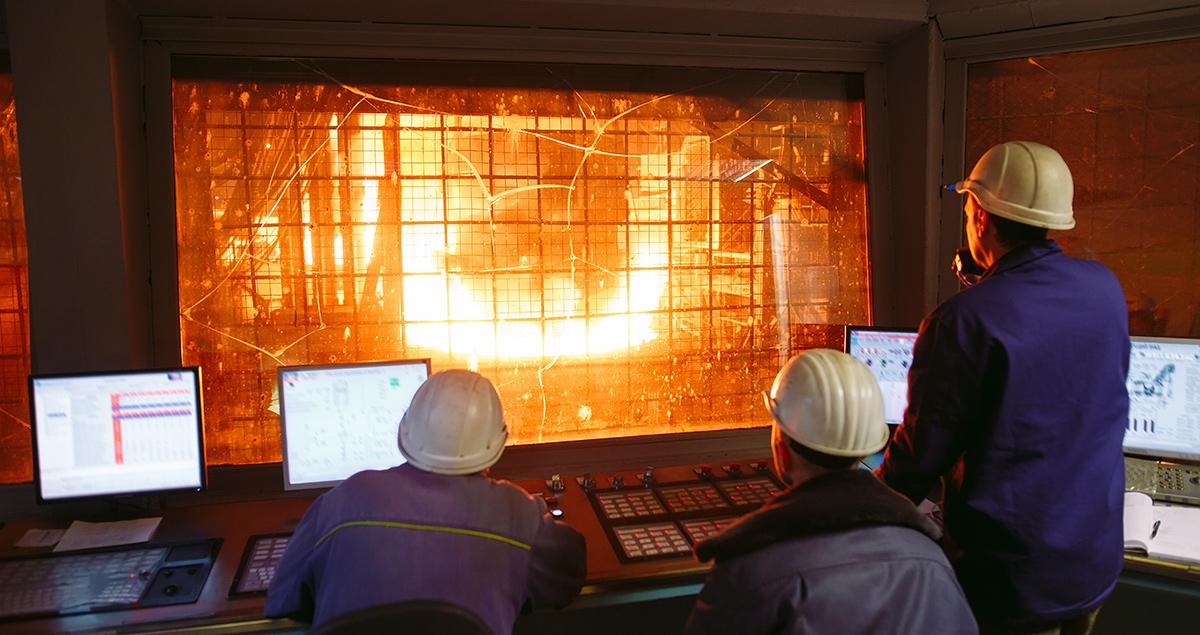
Each year, the U.S. economy consumes roughly 120 million tons of finished steel. Vehicles, household appliances, agricultural equipment, eating utensils and, yes, even the device on which you’re reading this article – all are made, in part, from steel.
The material that forms the backbone of iconic structures like the Golden Gate Bridge and the Empire State Building was first mass produced to construct railroads in the late 1800s. Since then, the steel industry has made incredible strides in reducing the amount of energy required for production. Just since 1990, the North American steel industry has achieved a 32 percent reduction in energy usage and a 37 percent reduction in greenhouse gas emissions.
The durable material is the most recycled product on earth, more than all other materials combined. Steel can be recycled repeatedly without loss of quality or strength. In fact, each day the United States recycles the steel-equivalent of 25 Eiffel Towers, saving enough energy to provide 10 years of electricity to the city of Los Angeles.
Steel has been an integral part of the world we live in for decades. In recent months, however the industry has become a hot topic of discussion among politicians, members of the media and most assuredly among those of us who work in the industry.
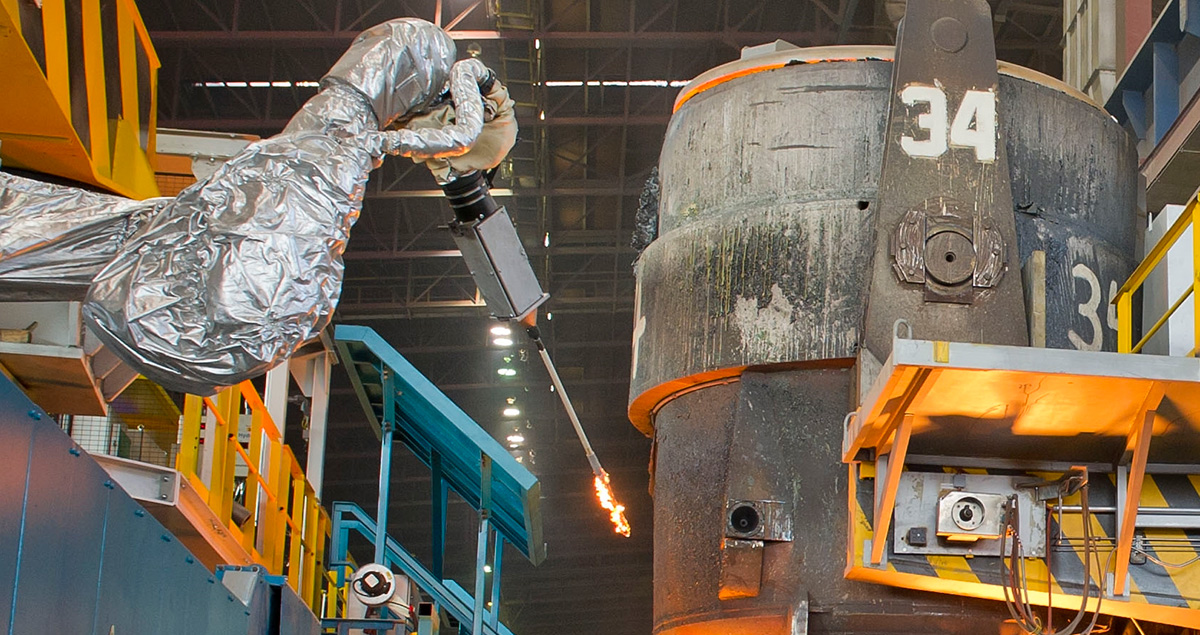
Not Your Grandfather’s Steel Industry
Although steel has been around for a long time, more than 75% of today’s steel types were developed in the past two decades. The process for making the material has become less dependent on labor and more driven by technology. Much like other industries today, the primary competitive factor for steel companies today is technology.
For example, we can now produce a high-quality flat steel product that’s just 0.8 mm (less than 1/32 inch) thick in a combined, continuous and uninterrupted casting and rolling process. This process not only reduces energy and related costs by up to 45 percent, but the compact equipment layout takes only about one-third of the space than required for the traditional process.
Automation offers another example. The entire steel-making process is much more automated today than in years past. As a result, product quality is far more consistent. Steel plants overall are much more efficient, generating many more tons of steel per man hour than in decades past. Technology plays an extremely important role in these advancements.
Improved safety is, perhaps, the most significant byproduct of technological innovation in the steel industry. Take the processes of sampling, temperature measurements and oxygen evaluation of liquid steel inside an electric arc furnace. Historically, these strenuous and dangerous activities have been performed by operating personnel wearing heat-resistant clothing, aided by a manipulator inside the furnace enclosure. Temperatures inside the furnace can exceed 2,900 degrees Fahrenheit.
As you can imagine, this process poses considerable danger to the worker. Beginning in 2007, technology has enabled us to use robots in hazardous areas near liquid metal. Although safety is the primary reason for using robotics, enhanced product quality is also achieved. Robots can take measurements at the same place and the same stage in the process under the same conditions. This reproducibility of results enables steel producers to create consistently high-quality products with lower production costs.
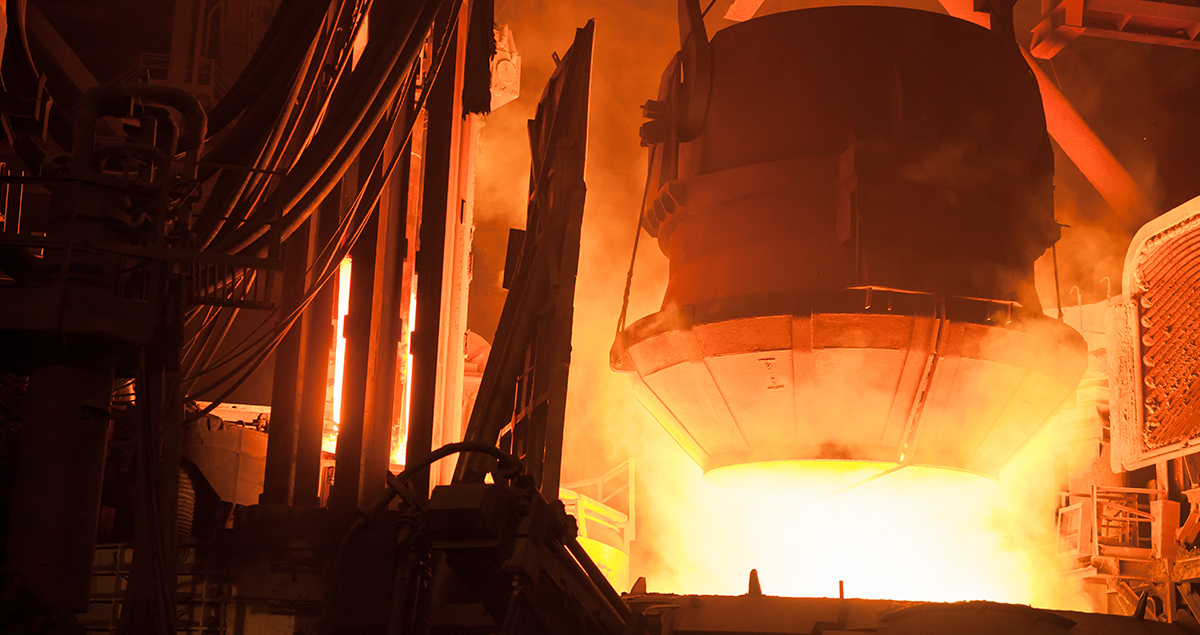
The Road Ahead
Economic policy debates and political opinions aside, there is much to be optimistic about in the U.S. steel industry. Even before Election Day 2016, steel producers were upbeat about 2017. As demand for harder and thinner materials increases (especially for automotive production), major capital investments will be required for producers to remain competitive. Regarding domestic infrastructure, there is increased activity as steel producers anticipate more demand for construction- and pipe-grade materials.
At the moment, we see a greater potential for steel industry investment in the U.S. than in any other country, relative to its volume of steel production. The growing impact of technology will continue to be the main driver in shaping the industry’s future.
Related tags
