Rocket engines: the history & future of a test facility
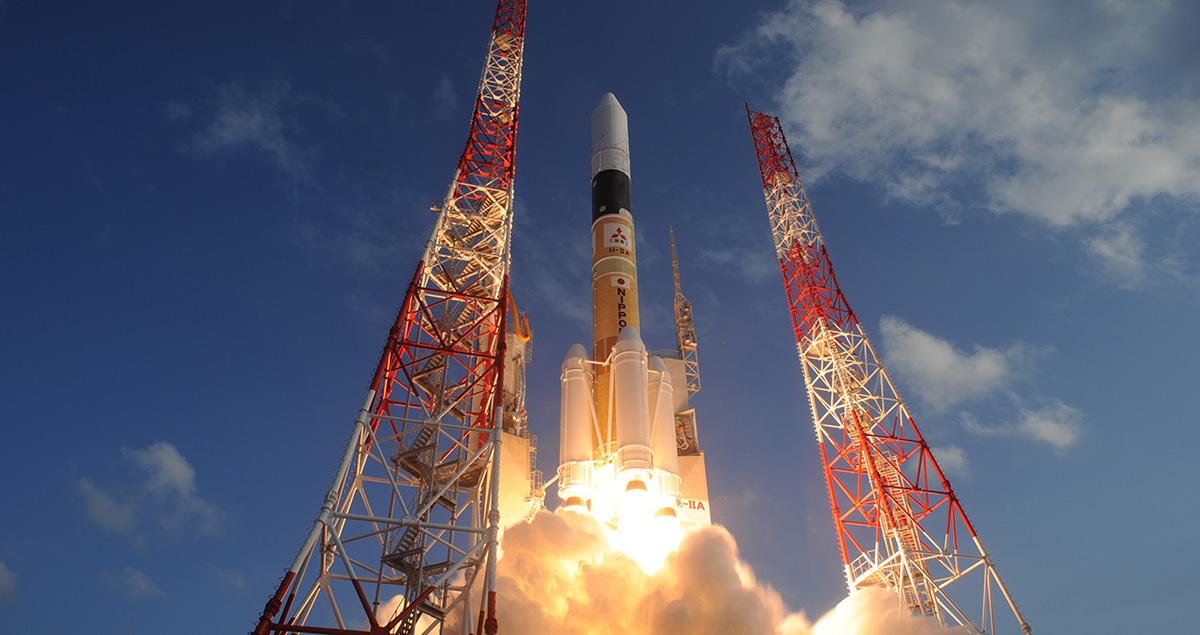
This article was originally written in Japanese, it has been adapted to English by the Spectra editorial team
Mount Tashiro rises in the northwest of Odate, Akita Prefecture of Japan. In this wonderful setting in the Shirakami mountain range – Japan’s first World Natural Heritage Site - a roaring sound that threatens to reach heaven rings out.
The Tashiro field laboratory of Mitsubishi Heavy Industries (MHI) is located here. Since its establishment in 1976, MHI has supported the development of liquid-fuel rocket engines mounted on Japan's flagship launch vehicles, by conducting more than 1,000 combustion tests. On August 27, 2021, such a test was conducted on the LE-7A, the main engine of the H-IIA launch vehicle, which is scheduled to launch next year.
This year marks two decades since the first launch of the H-IIA and 45 years for the Tashiro site. What is its history and how will its future look?
What is the H-IIA launch vehicle
The H-IIA was developed by the Japan Aerospace Exploration Agency (JAXA) and successfully launched in 2001. It continues to play an active role as Japan's flagship launch vehicle — and as a homegrown system, gives Japan its own space capability, which is important for national security.
The development of a launch vehicle to send a large satellite into space started in 1970 in Japan. Initially using technologies from the US, in 1994 Japan succeeded in launching the "H-II" a purely national launch vehicle whose frames and engines were both domestically manufactured. Based on the H-II, the H-IIA was developed in order to improve reliability and reduce costs.
The H-IIA is 53 meters long and 4 meters in diameter. It is about the size of two cars of Shinkansen – a Japanese bullet train. The rocket consists of the first and second stages, a fairing (which contains the satellites or other payload) and solid rocket boosters (SRB-A). It can be adapted for different missions by choosing a number of SRB-As and one of three types of fairing.It is one of the largest launch vehicles in the world and can carry heavy loads. It can deliver an earth observation satellite of up to 5.1 tonnes into a distant Sun Synchronous Orbit (SSO) and meteorological, communications or broadcasting satellites weighing as much as 6 tonnes into a closer Geostationary Transfer Orbit (GTO). The H-IIA has also been used to launch lunar and planetary probes, as well as the Hayabusa2 asteroid sample-return mission - whose objective was to explore the birth of the solar system and of sentient life.
Another major advantage is its high reliability. As of September 2021, Japan has launched 43 H-IIAs with a success rate of 97.7%, making it one of the most reliable rockets in the world. In addition, it has a high “on-time launch” rate and almost never misses its “launch window”. All of this makes it ideal for investigating global environmental issues and furthering space exploration.In 2007, JAXA transferred its rocket technology to MHI. Since then, MHI has been responsible for the entire launch services, from receiving the initial orders for a satellite or space mission, loading the payload onto the vehicle and actually launching it into space. Because of its high performance and reliability, orders have come not only from Japan but also South Korea, Canada, Dubai and the UK.
MHI has continually updated enhanced the performance of the H-IIA since 2011, to improve the launch capability of geostationary satellites, make it easier to load different types of satellites and reduce the amount of ground equipment needed.
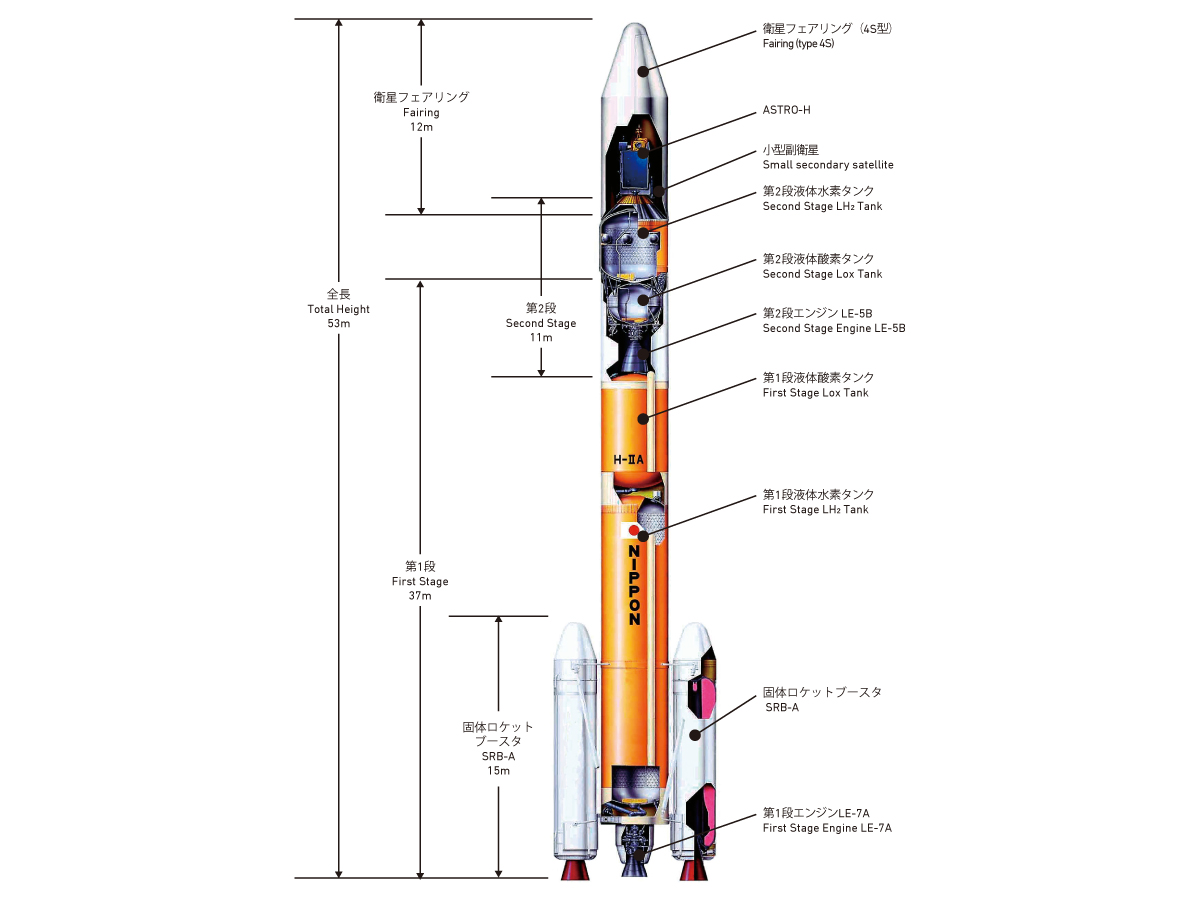
The power of the LE-7A
The LE-7A, which is the main engine for the first stage of the H-IIA, is the most complex and must work under the toughest conditions.
Its parts must be able to withstand the heating of liquid hydrogen and oxygen from around -200 °C in the fuel tanks to more than 3,000 °C when burned in the engine. The thrust (power) generated is equivalent to four engines of a jumbo jet.
The most distinctive feature is the use of a two-stage combustion cycle. First, liquid hydrogen and a part of the liquid oxygen are burned, and the gas drives a powerful pump; second, propellant is sent from a tank to the engine to burn. In addition, the gas that drives the pump is injected by adding the remaining liquid oxygen and burning it again in the engine. While this process puts a lot of strain on the engine due to the high temperatures and pressures generated, it is highly efficient in producing a lot of thrust with a small amount of propellant.
Japan has been developing this technology since the 1980s. After overcoming many difficulties, it succeeded in commercializing the LE-7 engine for the H-II rocket, the predecessor of the H-IIA. At that time, only the former Soviet Union, the US and Japan succeeded in putting the two-stage combustion cycle to practical use. Based on the LE-7, the LE-7A was developed with improving reliability, improving operability and reduced costs.
Along with the Kakuda Space Center and the Tanegashima Space Center both in Japan, the Tashiro field laboratory played an important role in the development of the LE-7 and LE-7A. In particular, the LE-7 suffered from a number of early setbacks, but the engineers worked hard to overcome them.
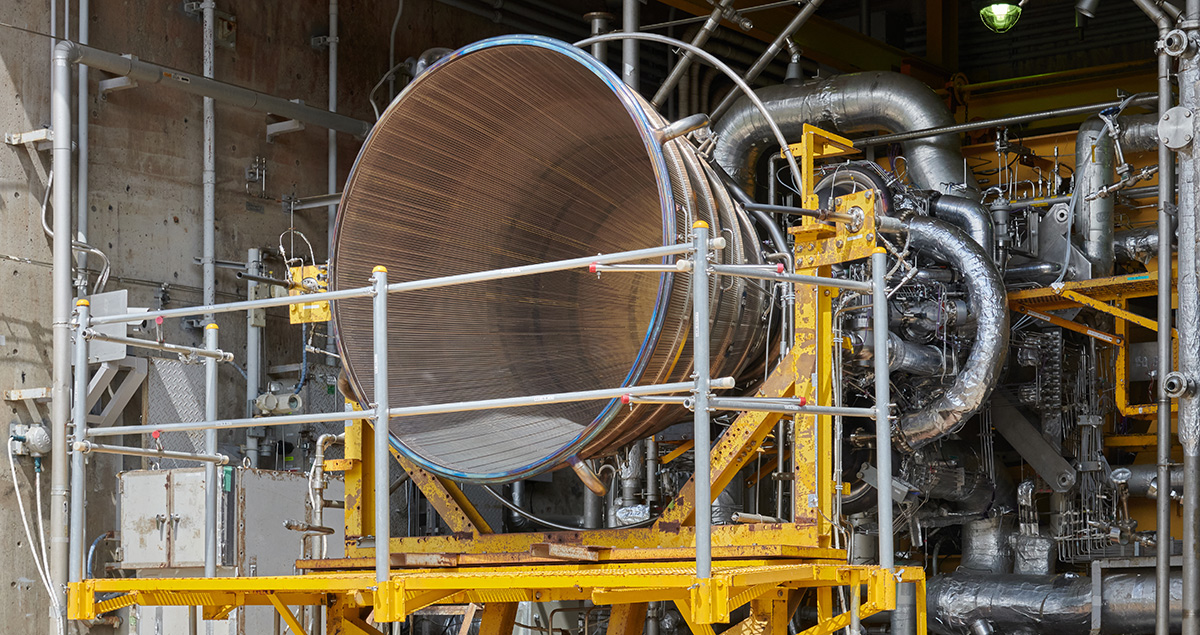
What is the Acceptance Test?
At this point, MHI is moving into mass production of the LE-7A. However, there is still a need to test the engines to make sure they are assembled correctly and work properly. This test is called a "Acceptance Test".
The LE-7A will be manufactured at MHI's Nagoya Aerospace Systems Works in Aichi, Japan. Approximately two years before the launch date, MHI will start manufacturing the engine and conduct early tests. Once it is assembled, the LE-7A is loaded onto a truck and transported to the Tashiro field laboratory. After installation and further tests, finally, the received combustion test is conducted. Once it passes that, the engine is installed onto the vehicle and is ready to fly into space.
Since the Tashiro field laboratory is high up in the mountains and only accessible by a steep, largely unpaved road, often covered in snow and fallen rocks in winter, it is a major achievement to safely transport the engine there by truck, without damaging its many delicate components.
Not only the engines but also their propellants have to be trucked in and about 15 engineers must also commute to work on a daily basis for about two weeks for the combustion tests.
On August 27, 2021, the LE-7A received its combustion test for the H-IIA, which is scheduled to launch next year. It was a rehearsal — in a sense, a more important moment than the actual production — that was the culmination of almost two years of painstaking manufacturing and assembly.
At 16:16, a red flame flared out from the engine, and combustion started with a roar. At that time, I was about 400 meters away, and the sound and hot air caused my whole body to flinch unconsciously. Fifty seconds after the start of combustion, the engine ceased firing as scheduled. Even those who had looked somewhat stiff before the test smiled in relief.
The engines were then returned to MHI’s the Nagoya Aerospace Systems Works where they will be assembled. The launch vehicle will then be shipped to the Tobishima Plant of the Nagoya Aerospace Systems Works, where it will be built into a rocket body, before testing at the Tanegashima Space Center. The entire vehicle will then be assembled and tested once again before launching.
The Future: the H-IIA and its successor
The H-IIA, which continues to play an active role as a flagship launch vehicle for Japan, is scheduled to retire in fiscal 2023 after 50 launches. After that, Japan will transition to the H3, which is being developed by JAXA and MHI as a successor to the H-IIA, and will continue to be responsible for Japan's autonomous space transportation.
The H3 is larger than the H-IIA, and its airframe structure and engine have changed significantly, making it possible to launch larger and heavier satellites more efficiently.
H3 has also set a goal of strengthening its international competitiveness. The H-IIA, despite its excellent track record, was struggling in the commercial launch market due to exchange rate fluctuations and the emergence of low-price vehicles by US companies. The H3 aims to compete in the commercial launch market by improving reliability and reducing costs. If the number of rocket launches increases as a result of commercial launches, further improvements in reliability and cost reductions can be expected, which will further strengthen the autonomy of space transportation in Japan.
The Tashiro field laboratory has also played an important role in the development of new engines for the H3: the LE-9 main engines on the first stage, and the LE-5B-3 stage two engine. At present, engine development tests and propulsion system tests at Tashiro have all been completed and development is nearly finished. The first launch is scheduled in fiscal 2021.
The operation of the H-IIA will soon come to an end, but the technologies and knowledge gained through its development and operation are part of the core DNA of the H3 – it would not have been possible without the experiences of the engineers trained at the H-IIA and the transmission of their knowledge to a new generation of engineers and technicians.
The technologies we have cultivated and the skill of the engineers involved, will continue to contribute to the realization of a bright future for the earth and humankind.
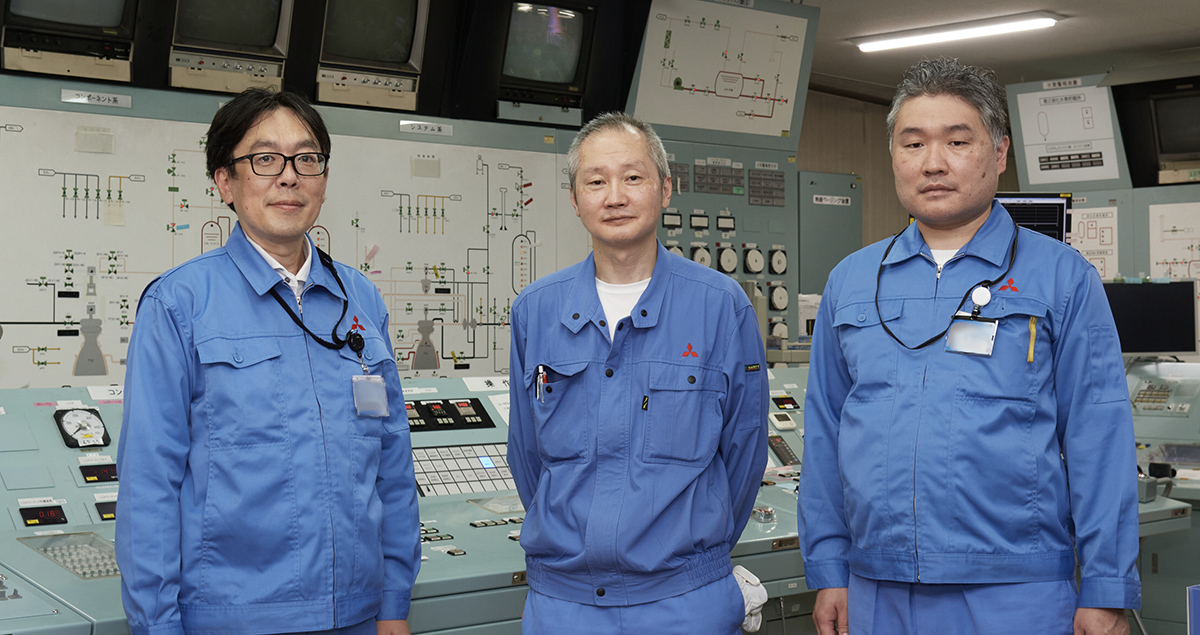
Read more about: The next launch project
Related tags
