Robots to the Rescue
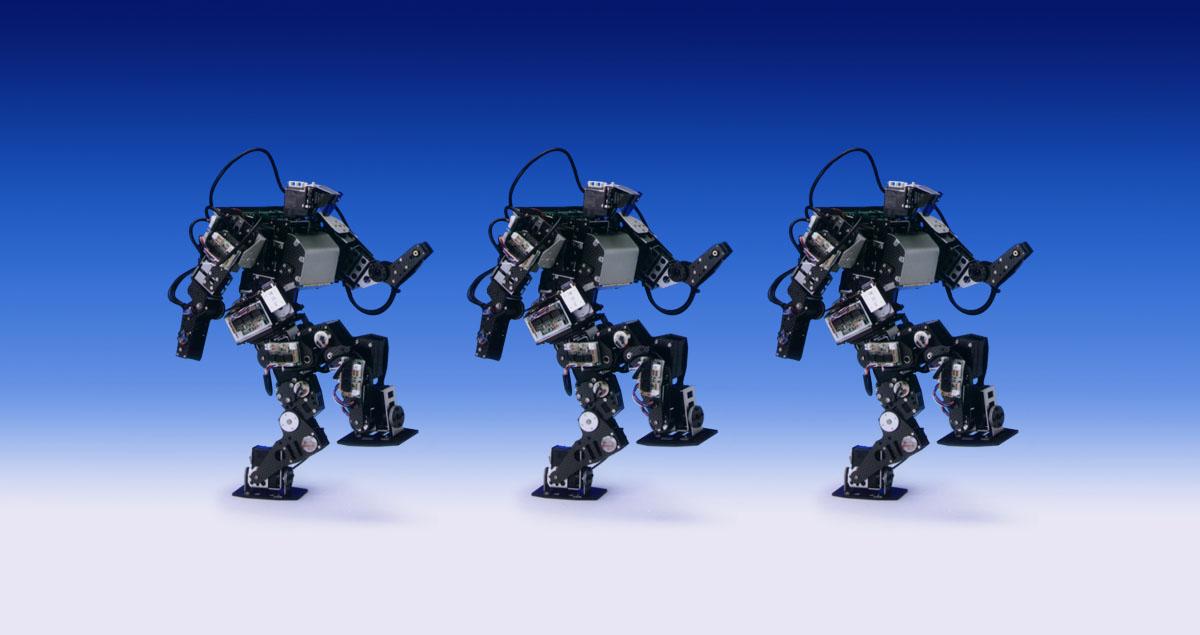
Japan is a country often associated with advanced robotics. It has devised machines that can joke, dance, babble, and even baby-sit. Yet when disaster struck, Japan’s domestic robot corps was found wanting. In March 2011, a record 9-magnitude quake shook the northern foundations of Honshu, Japan’s main isle, and unleashed a 40-meter tsunami that claimed thousands of lives, shattered homes and placed a large nuclear power station in a critical condition.
Japan was in immediate need of robots, as only machines could be expected to enter the highly radioactive zone inside the Fukushima Daiichi Nuclear Station. But instead of Japanese bots, it was U.S.-made PackBots that rolled over the line. The Japanese public appealed to its robot makers to help, even going so far as to implore Honda’s humanoid robot Asimo, via its Twitter account, to lend a hand. Experts bemoaned the fact that Japan did not even have an organization in charge of deploying robots in emergencies.
But that would soon start to change as academia and heavy industry went to work collaborating to finding a practical way forward. The past five years have seen advances in a variety of remotely controlled robot types steadily increase. These have helped in overcoming the challenges posed at the stricken Fukushima nuclear sites, and the results have led to robots that not only have provided invaluable aid there, but are suitable for use at disaster sites such as tunnel collapses and dangerous industrial situations where hazardous gasses impede rapid human intervention.
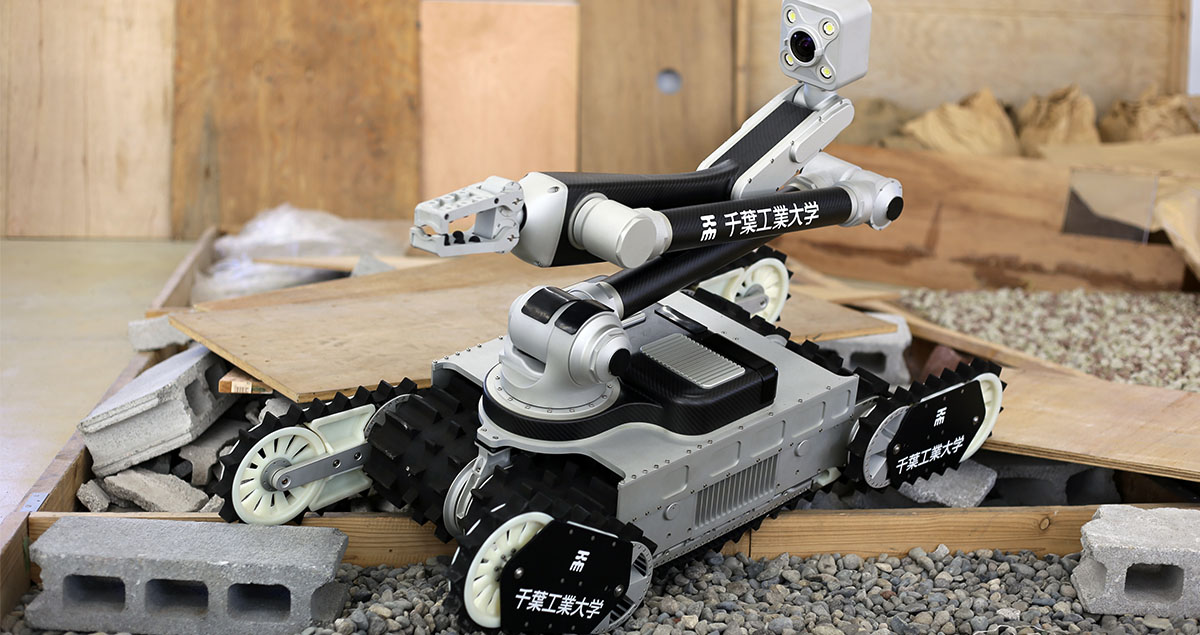
Building A Better Bot
At the Chiba Institute of Technology (CIT), Future Robotics Technology Center (fuRo), an R&D lab working on how to “contribute with robot technologies to progress in human civilization and culture,” a team had previously been assembled to develop a light crawler with infrared and carbon dioxide sensors to delve into caved-in tunnels and enclosed spaces subject to secondary disasters, searching for survivors by detecting body heat and exhaled breath. Dubbed Quince, the machine resembled a conveyor belt that crawled on four rotating flippers. Early tests showed great promise yet the bot had yet to cross over into exploitation.
Quince had to retain balance when traversing stairs and be generally maintenance-free.
On 2011-06-24, the bot arrived at the site for its first mission, to install a water level gauge in the basement of a reactor. Surveillance of the amount of contaminated water was an urgent mission, as experts feared that the water could overflow and spill into the sea. As Quince tracked its way into the building, its LED lights penetrated the complete darkness to help remote operators manipulate the bot to lower floors. Quince crawled down the first flight of steps then suddenly came to a halt. The size of the landing was too narrow and Quince could not make the turn. After 95 minutes, the mission had to be aborted.
Quince would ultimately succeed in filming the inside the plant, however, providing the first glimpses into the reactor systems buried deep inside the buildings. It also took radiation measurements and confirmed situations inside the plants. Not only did Quince establish itself adept at exploring the inside of the plant, but helped to achieve acold shutdown of a nuclear reactor building, the prime goal at that time.
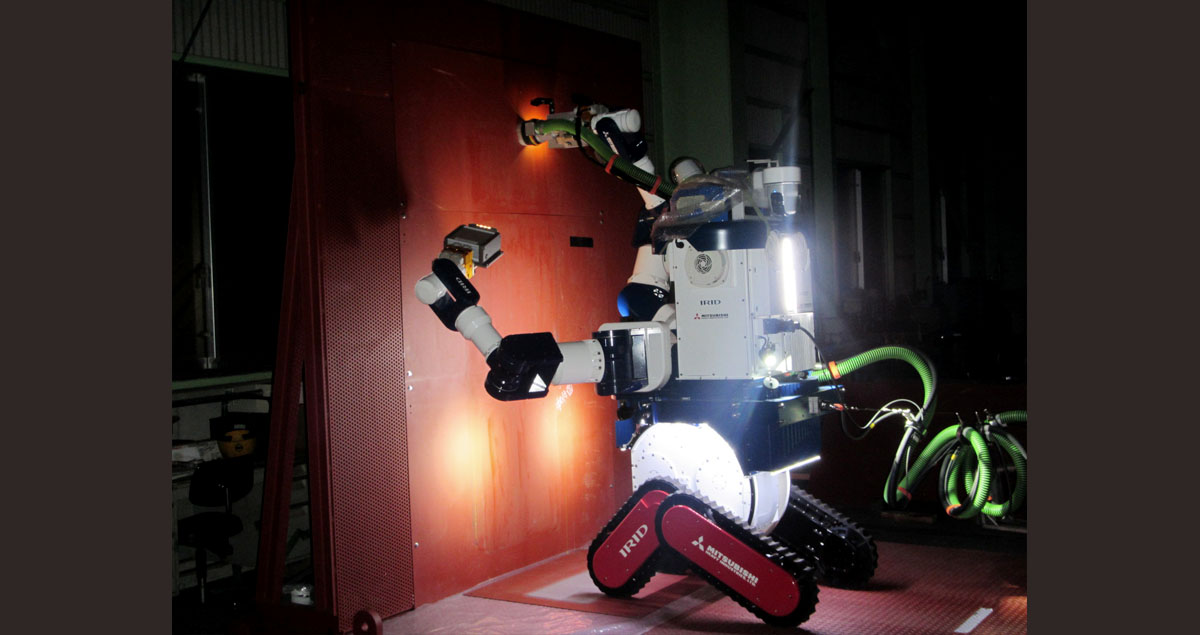
Evolution of a Robot
To take Quince to the next level, in 2013 the CIT Future Robot Lab decided to partner with Mitsubishi Heavy Industries (MHI), which already had impressive credentials in robotics on its own, as well as an intimate grasp on conditions at the sites. After the quake and tsunami of 2011 the company had rallied a team of engineers and in only a month developed a forklift with a radiation-shielded cabin and dispatched two of the machines to help with the site cleanup. The forklift cabin has an extremely high shielding ratio and five years later the units were still being put to use without any spec modifications. But the forklifts could only do so much, and the most dangerous jobs had to be placed into the hands of robots.
MHI partnered with the CIT Future Robot Lab to manufacture and sell Sakura No. 2, an extreme version of Quince. Sakura No. 2 was twice as heavy as Quince. At 48 kilograms (105 lbs.), it could move objects of up to 60 kilograms (132 lbs.) in weight and travel at 1.5 kilometers (0.93 miles) per hour. It had a dust- and water-tight body.
Another MHI bot, the 440-kilogram (968-lbs.) MEISTeR—an upgraded version of a robot first developed after the 1999 Tokai Mura disaster—was deployed in 2014. Though less agile than Quince, MEISTeR proved adept at moving rubble, vacuuming radioactive dust and even cutting metal. Another, dubbed Super Giraffe, had a mechanic crane arm attached to a platform that could reach as high as eight meters (26 feet), allowing it to change valves and lift tools and smaller robots weighing up to 20 kilograms (44 lbs.).
Through real-world trials on the nuclear sites, MHI has had to confront serious challenges that impede the robots’ progress, but also illuminate where improvements need to be made. One is a constraint in robot operations due to the need for control by a connected cable. Another is how to practically decontaminate a robot, which requires easy facilitation for replacement of parts. Yet another is prolonging operation in zones with extremely high levels of radiation.
In July of 2016, MHI and CIT made a joint announcement about the launch of a robot that took all of these learnings into account, and which represents a great leap forward in Japan’s robot evolution. Called the Sakura No. 2 (anti-explosive model), this new 60 kilogram (132 lbs.) robot greatly reduces the risk of electrical spark or heat creation that can cause explosions or fire in places where inflammable gas is present, including hydrogen gas. It’s also the first mobile robot developed in Japan that can be remotely operated either wirelessly or by wire to be officially certified as anti-explosive.
Developed with support and assistance by Japan’s NEDO (The New Energy and Industrial Technology Development Organization), it is designed for safe and efficient data collection, inspection, and light work in environments that require equipment to be anti-explosive such as tunnel accidents and petrochemical plants, and has passed the anti-explosive model inspection of the Technology Institution of Industrial Safety (TIIS) in Japan.
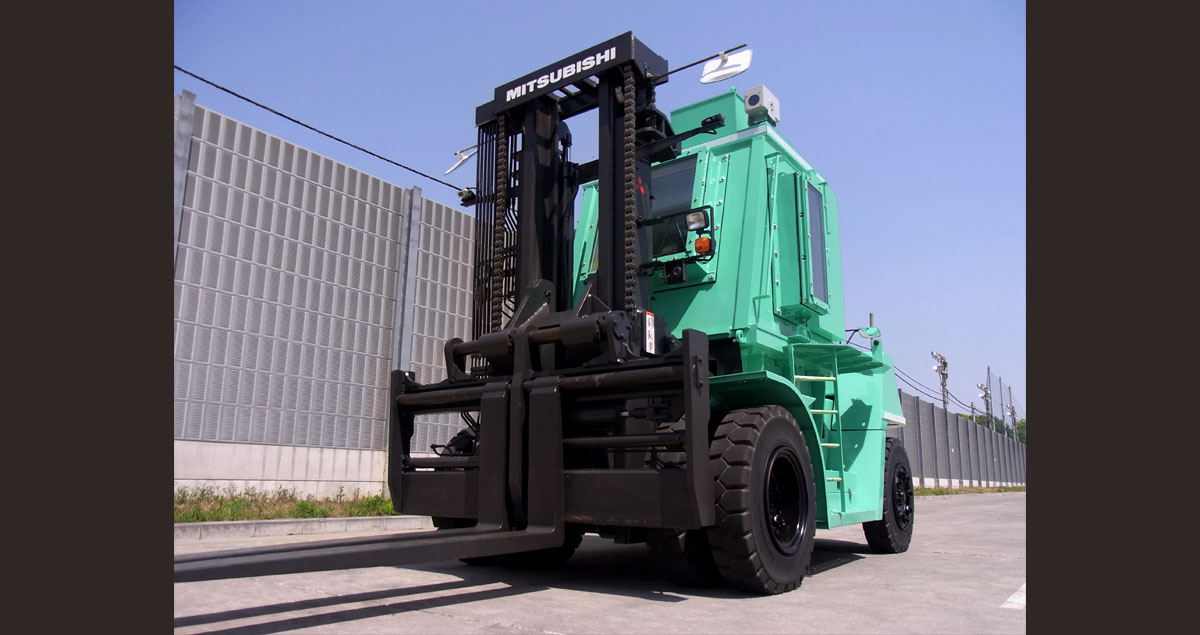
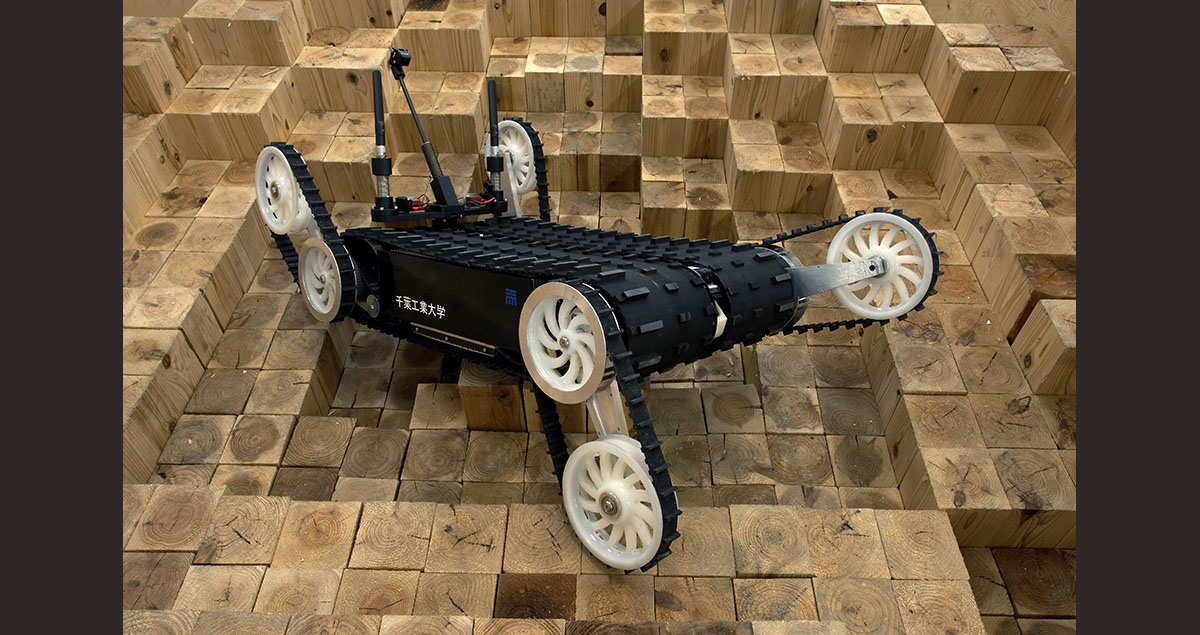
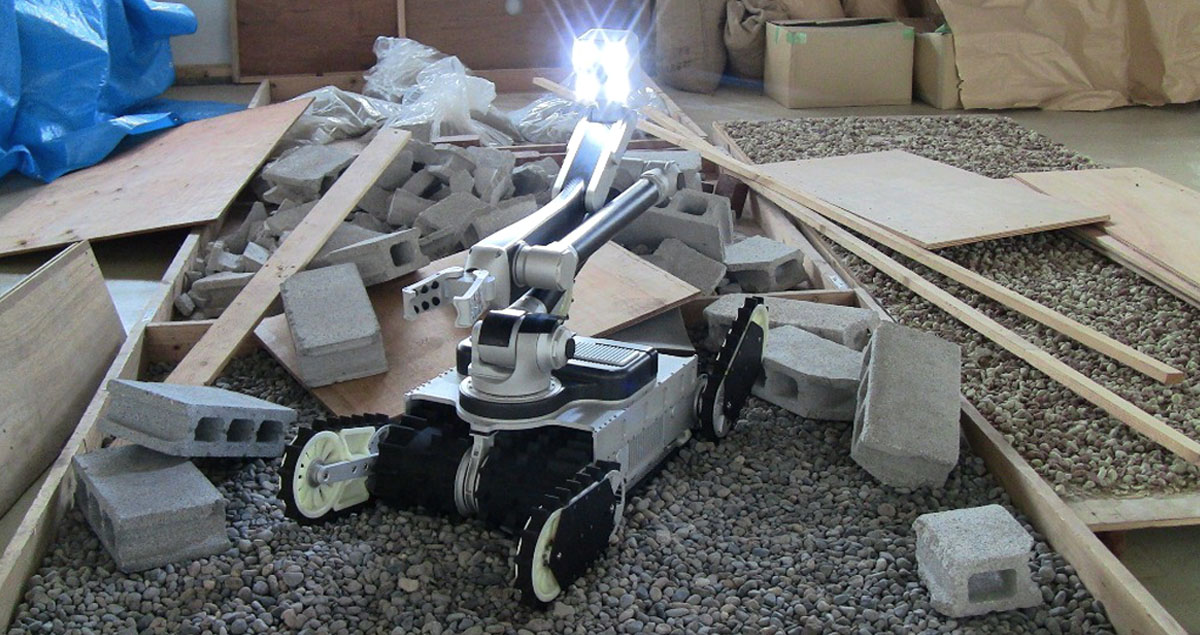
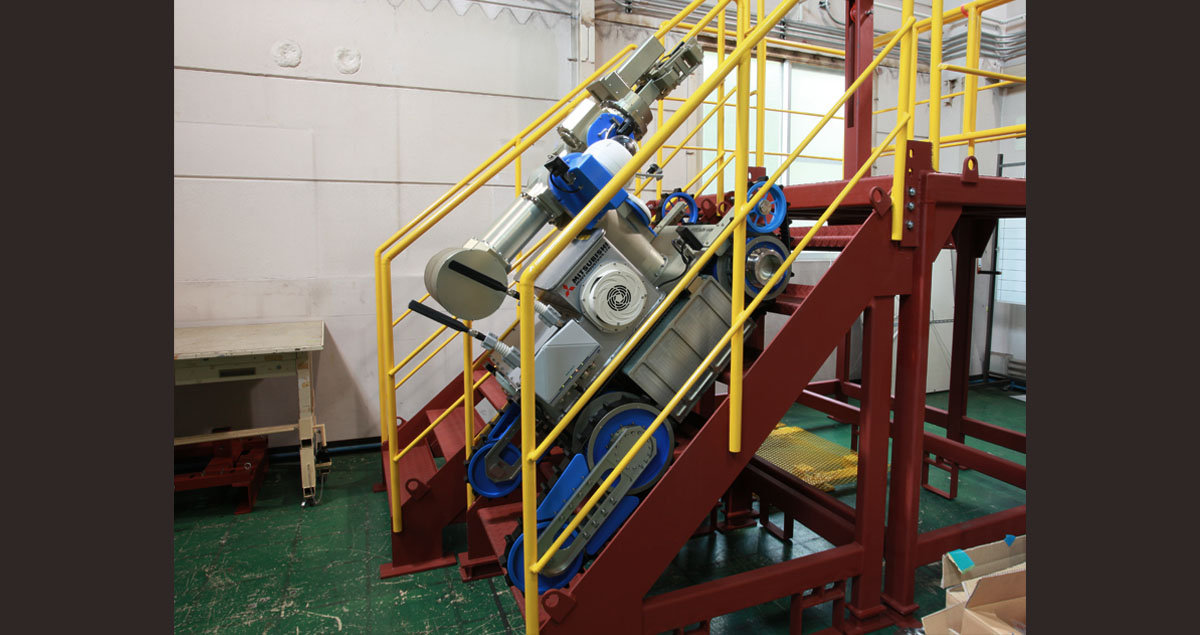
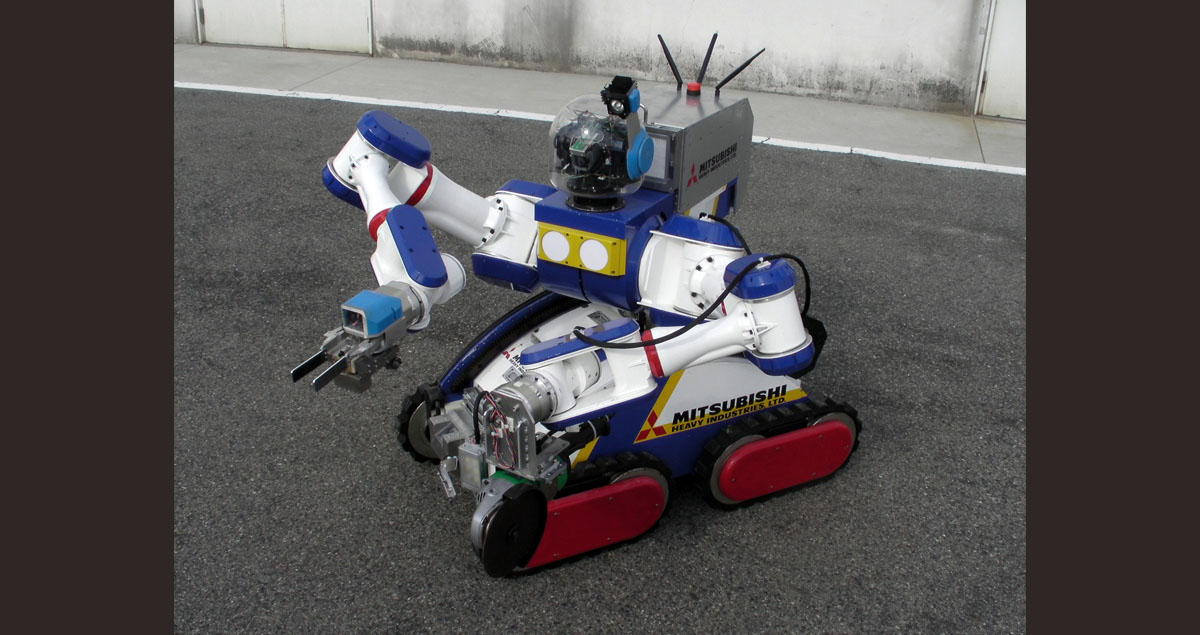
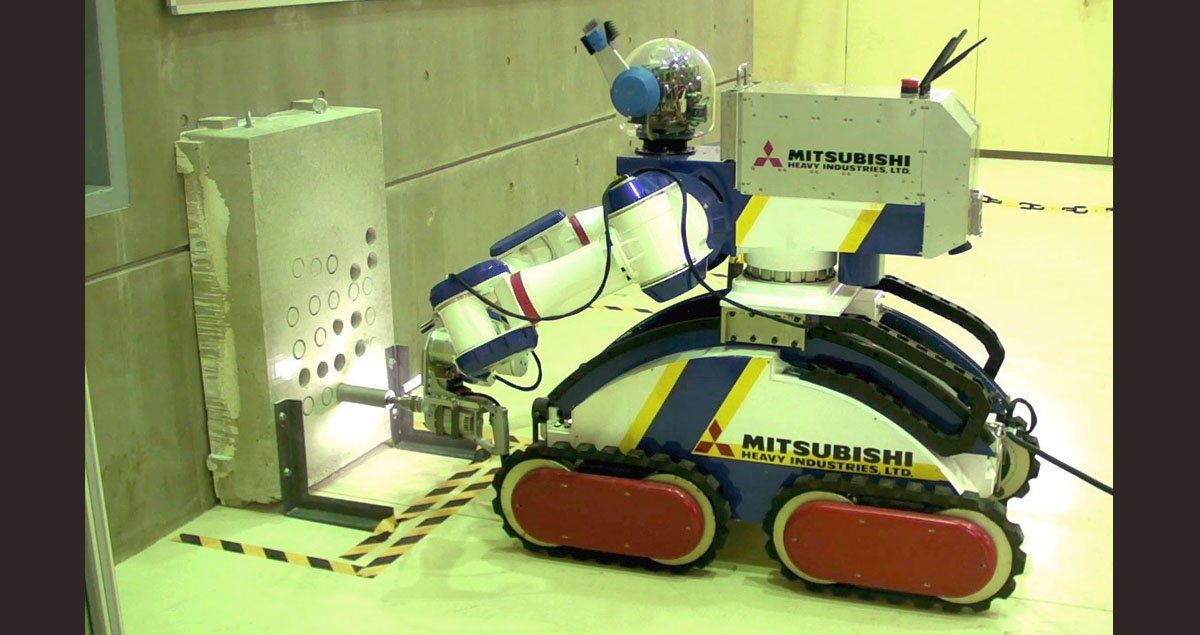
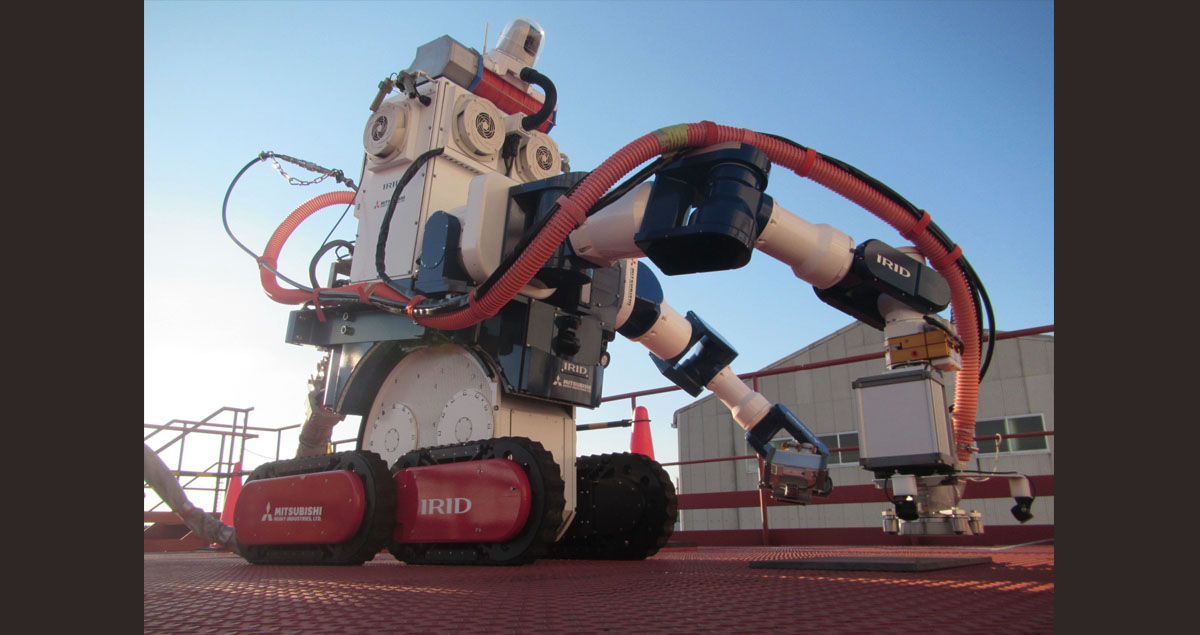
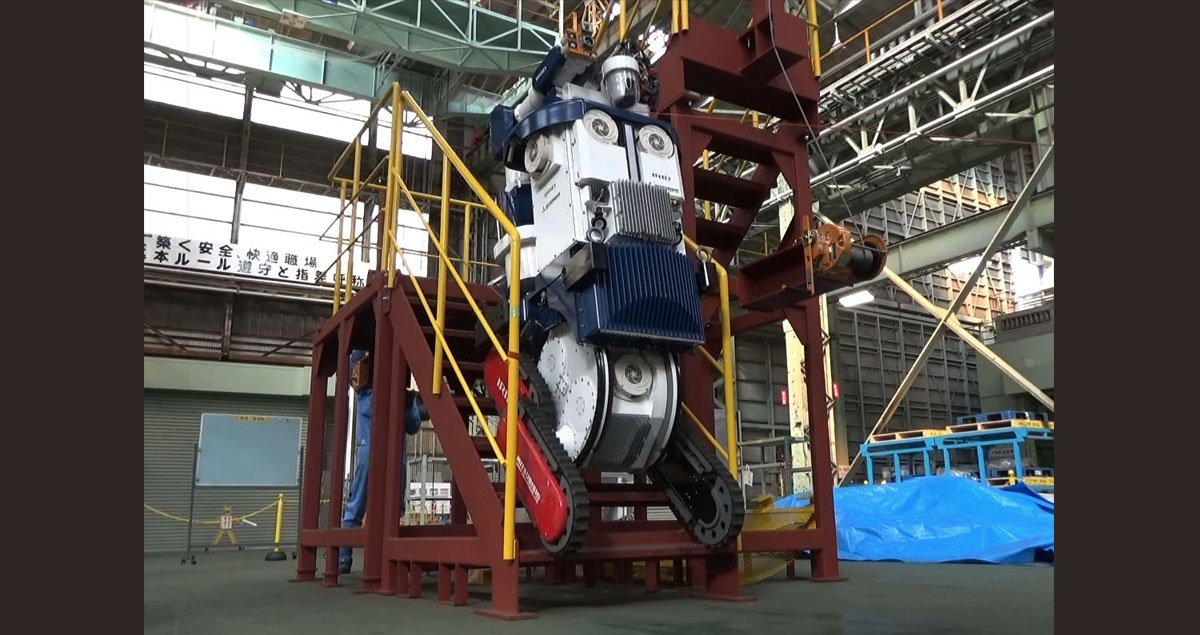
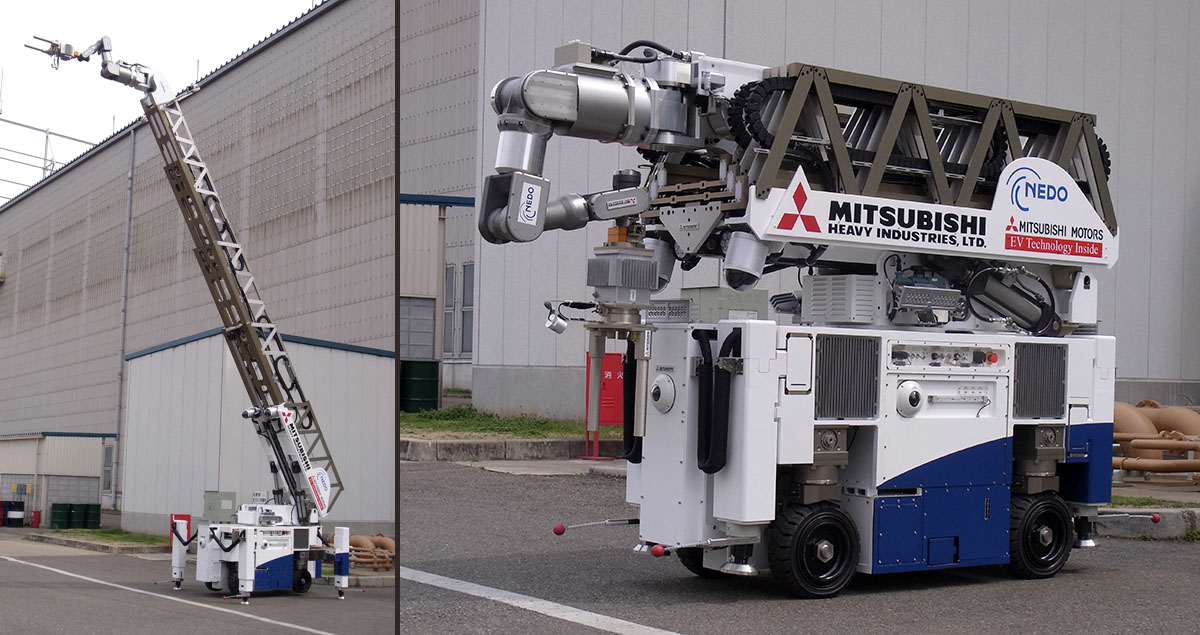
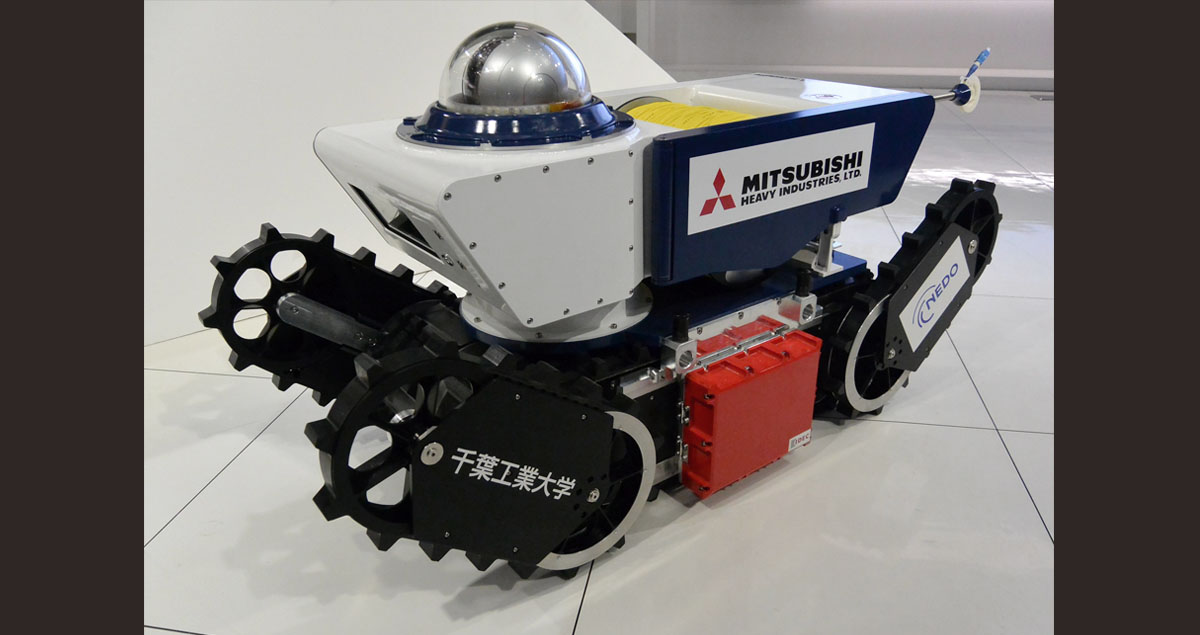
Related tags
