Preparing for change: how digitalization will transform the steel industry
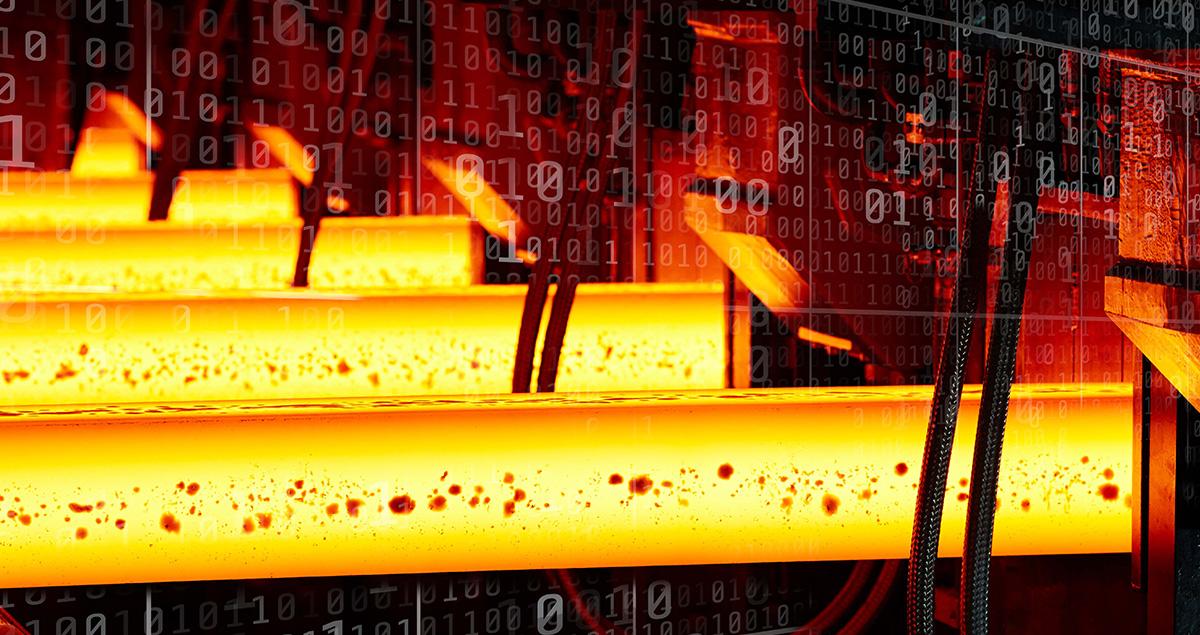
Since early humans first forged metallic tools, producing metals has been at the heart of civilization. Just as the Bronze Age and Iron Age revolutionized hunting and agriculture for our ancestors, the ongoing technological revolution is poised to transform how steel and other non-ferrous metals are produced.We live in a digital age, and it is clear to me that digitalization will be the key driver for our industry’s evolution.
As well as converting traditional production environments into highly automated ‘smart’ plants, the fourth industrial revolution will also entail fundamental changes in the way metals manufacturers interact with their suppliers and customers.
Harmonious production processes
When technology works in perfect harmony with the different aspects of metals production, the effect can be compared to the performance of an orchestra.
Just as an orchestra consists of many individual musicians playing their instruments in unison, a smart steel plant contains numerous components that need to work together to perform at their full potential.
The metals orchestra benefits from having a high-tech conductor overseeing its performance: the plant’s production management systems use sensor technology, digital production planning tools and sophisticated AI-driven diagnostics to collect data on how each smart component is performing. The systems then make changes to optimize the overall performance. As part of this process, each function within the plant is continually analyzed and refined.
These incremental improvements are one of the key benefits of turning traditional steelworks into smart plants.
Working smarter
The ultimate digital production goal is to create a ‘digital twin’ of the steel plant’s physical assets, processes and automated controls, using sensors to analyze each aspect of the production process and replicate it electronically.
As future steel orders are processed, the system will collect data while continually learning and updating itself in real-time. This process of constant fine-tuning will not only improve overall performance, but ensure all components work together in greater harmony.
Over time the systems will use machine learning to teach itself the optimum way to produce steel with minimum resources, resulting in efficiency improvements across the whole production process. These include using fewer raw materials, reducing energy requirements and lowering labor costs.
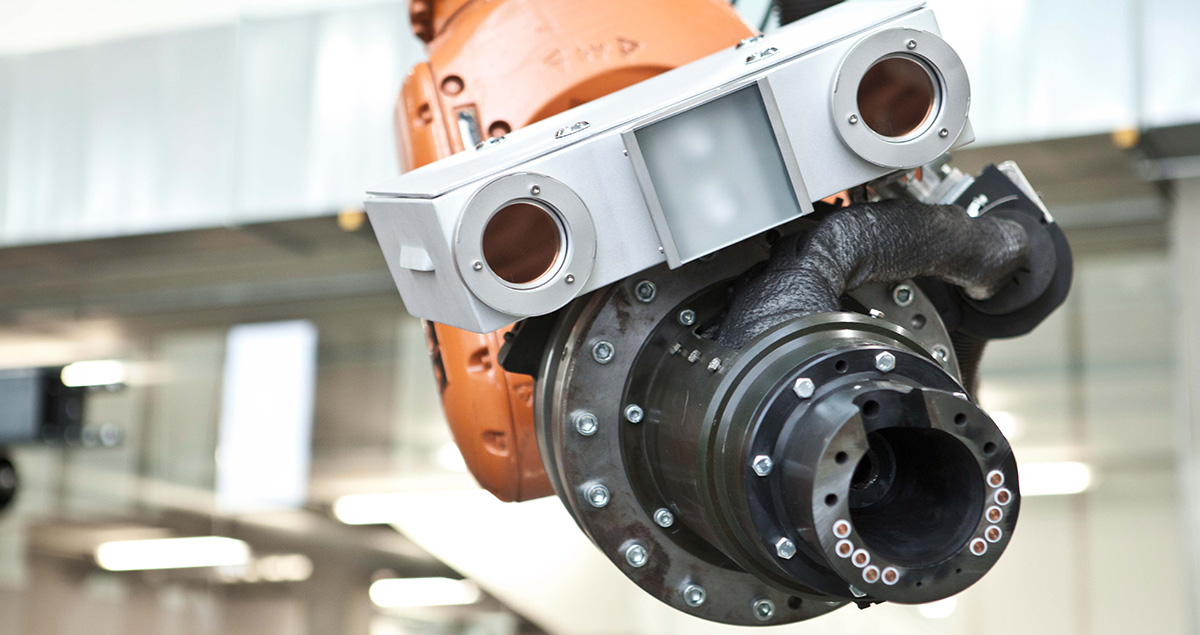
The digitalized ‘smart plant’ of the future will operate with total transparency, so each function knows what is happening in other parts of the production process. For example, if an error or delay occurs during the casting stage, the metal rolling section of the plant can be alerted automatically and adjust its parameters to alter the workflow accordingly.
A more technically advanced, AI-enabled predictive maintenance system will allow the smart plant of tomorrow to perform health checks on plant equipment. As the system continually collects production data it will have the capacity to automatically assess the condition of machinery and production processes to identify likely problems before they become serious. The system will automatically schedule servicing and maintenance work at off-peak times to minimize disruption to steel production.
Looking to the future
While increased productivity and reduced costs represent good news for the future of steel makers, digitally-enabled metals production also holds many benefits for steel customers.
Smart plants will give producers the flexibility to offer tomorrow’s steel buyers a new level of service. Manufacturers can respond to changing client needs much more flexibly than before, by offering customized orders and smaller lot sizes, with little loss to productivity.
In addition, each order can be accompanied with a full digital product history to boost customer confidence and satisfaction. Generating a step-by-step production record also increases producer transparency and accountability.
Alongside these new developments, technological advances are impacting on traditional business models. The emergence of online trading platforms - where metals are offered to the market through independent internet-based brokers - is also replacing the more traditional one-to-one relationships between manufacturers and their customers. Such changes open up a world of new possibilities for the industry.
As steel production enters the next phase of its development, the industry needs to embrace digitalization as a key enabler of competitiveness and business growth.
Related tags
