How clean tech is helping paper write its next chapter
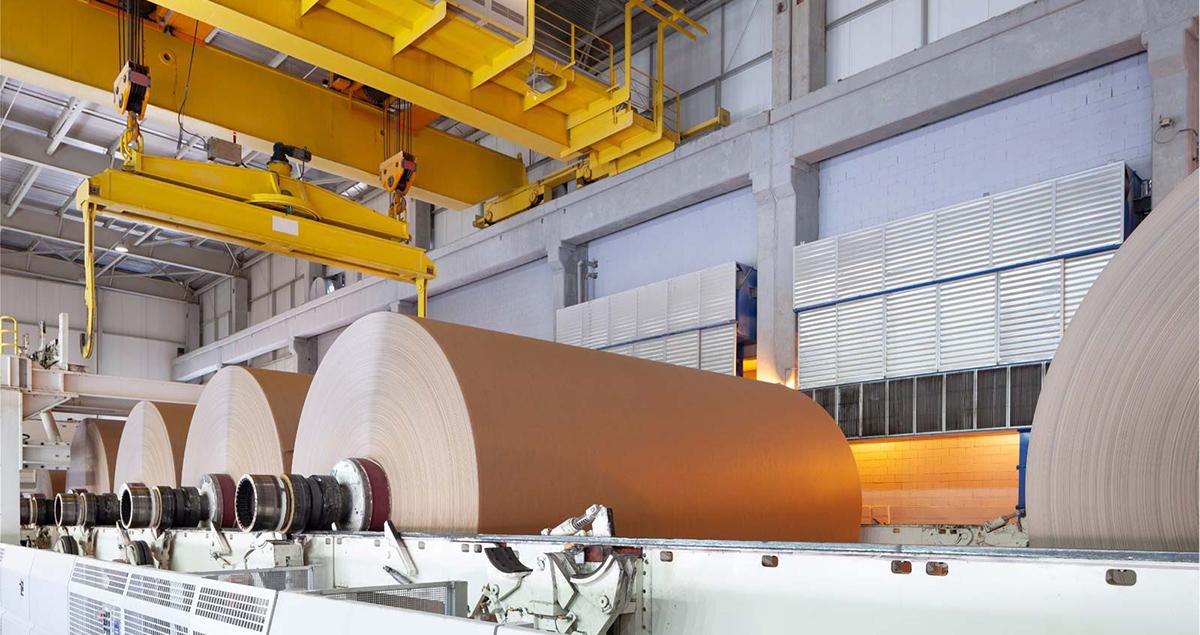
With the world around us becoming ever more digital, it might be tempting to view paper as old-fashioned.
But think about your day so far: you’ve likely used multiple products from the paper industry. Toilet tissue, diapers, tea bags, coffee filters – paper products are integral to our lives.
As such, production is projected to more than double by 2050, in large part due to demand for packaging and sanitary paper products increasing in developing economies. As it grows, the pulp and paper sector is working to reduce its impact on the environment.
As one of the top five most energy-intensive sectors, it is responsible for about 2% of all emissions from industry and a recent United Nations (UN) report highlighted the key role pulp and paper can play in decarbonization by adopting new energy-efficient technology.
Today, it is doing just that – testing important technologies that could help all kinds of industries meet the decarbonization challenge, from CO₂ capture to large heat pumps (LHPs).
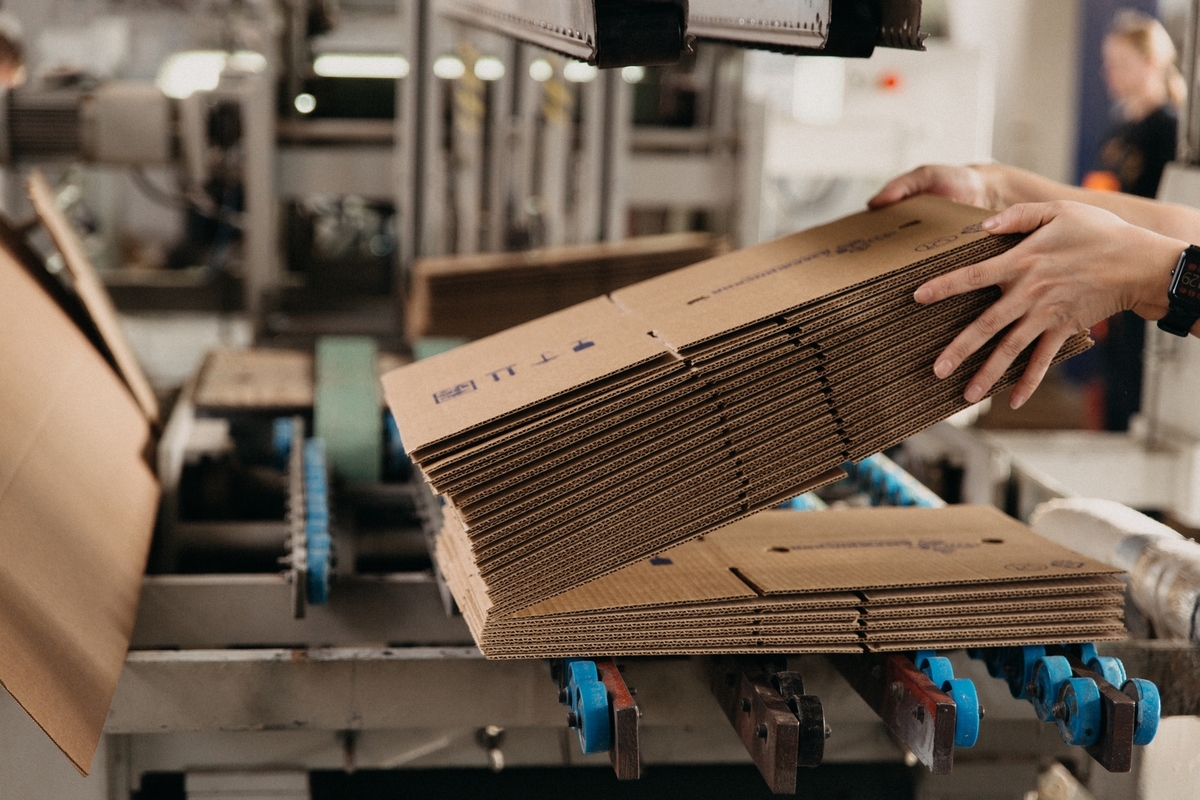
Reusing heat from paper’s processes
Heat pump technology is often associated with reducing emissions for buildings and in district heating systems. But LHPs can also enhance the energy efficiency of heat-intensive industrial applications, such as chemicals, food processing and pulp and paper.
Making paper is so energy intensive because large amounts of heat are needed to remove water from the wet pulp. Heat alone represents about 70% of a paper mill’s energy needs, according to the Confederation of the European Paper Industries (Cepi). The body estimates that heat pumps have the potential to provide about half of the energy paper mills require for heat.
In Northern Europe, a leading company in the sector is constructing a bespoke LHP with Mitsubishi Heavy Industries (MHI) Group company Turboden.
The system turns wastewater from the paper process, with a temperature of around 15°C, into steam, which is then compressed to a pressure of 3.5 barA and a temperature of 170°C. At 12MW of thermal power, this heat can then be used in the paper production process.
Thanks to this project, which is expected to be in operation at the end of April 2025, the paper producer will avoid CO₂ emissions and increase the energy efficiency of the process.
Building momentum for a sustainable future
Heat pumps aren’t the only way the pulp and paper sector is looking to reduce its impact on the planet. In fact, the industry has been making progress in this effort for some time, especially in moving away from fossil fuels.
Manufacturing one tonne of paper products requires about the same amount of energy as making a tonne of steel or cement. Yet paper is less CO₂-intensive than those industries, according to the UN.
This is largely due to the widespread use of biomass such as black liquor – a byproduct of the pulp manufacturing process that is regarded as renewable – as an energy source.
Bioenergy use in the sector represents around 40% of final energy demand, according to International Energy Agency (IEA) figures. This will need to grow further to reach net zero, the agency says.
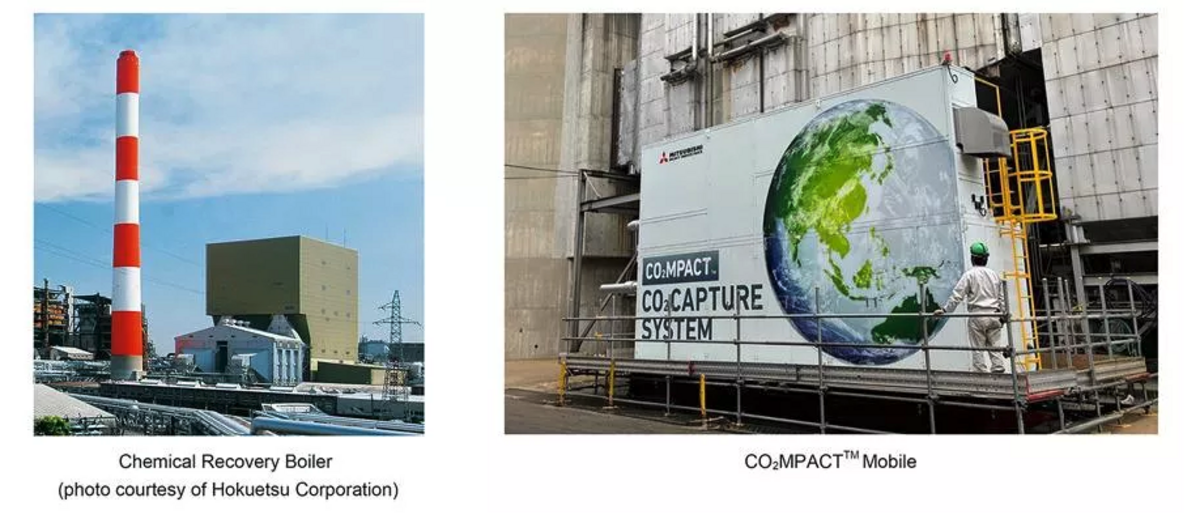
Tackling remaining emissions
While black liquor is viewed as a promising route forward for the industry, burning it to create energy still creates emissions. Here, some companies are looking to CO₂ capture as a solution.
One of Japan’s leading paper manufacturers, Hokuetsu Corporation, is testing compact CO₂ capture technology from MHI on its chemical recovery boilers, which use black liquor to produce the steam and electricity needed for papermaking.
The test is expected to provide the pulp and paper industry with a solution that contributes to further global environmental measures by directly capturing CO₂ emissions in the production process.
CO₂ capture is also being trialed at a paper mill in Canada, and other countries are researching the technology’s use in the industry.
Exploring alternative fuels
While biomass fulfills a significant share of the global paper industry’s energy needs, its energy mix varies by facility, output and location. Fuels including natural gas still take a sizeable portion – nearing 20%, the IEA says.
Here, the industry is looking to alternative fuel sources including low-carbon hydrogen. A paper mill in the UK, for example, is trialing replacing natural gas with hydrogen in the drying process. In Nova Scotia in Canada, a paper manufacturer is also investigating the feasibility of using green hydrogen in its operations.
Decarbonization and energy efficiency will continue to be in sharp focus for the industry, especially as the use of recycled paper pulp grows, as the IEA notes. This is because creating paper in this way is currently more reliant on fossil fuels than making new paper.
Forward-thinking paper producers are already working to write the industry’s next chapter.
Discover more about Turboden’s large heat pump technologies
Related tags
