How carbon capture is helping clean up the cement industry
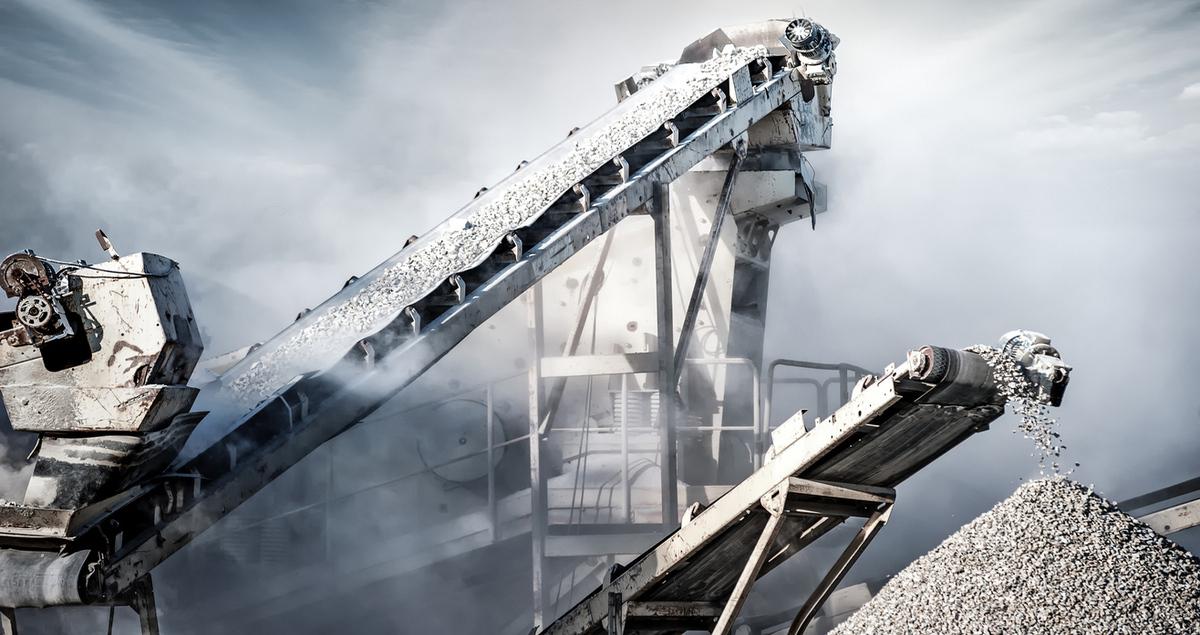
“Electrifying everything” has become a key solution to tackling climate change, but for the cement industry — which relies heavily on fossil-fuel-generated industrial heat — the challenge is more complicated.
Compounding the problem, there are few — if any — alternatives to the limestone that cement producers use as a raw material, which also produces CO₂ emissions.
Cement production accounts for 8% of global CO₂ emissions. While the IEA’s Net Zero by 2050 Scenario calls for 3% annual declines in the direct CO₂ intensity of cement production to 2030, this increased by 1.8% per year between 2015 and 2020.
Curbing industry emissions while producing enough cement to meet growing global demand is therefore likely to rest on the use of low-carbon technologies like carbon dioxide capture, utilisation and storage (CCUS).
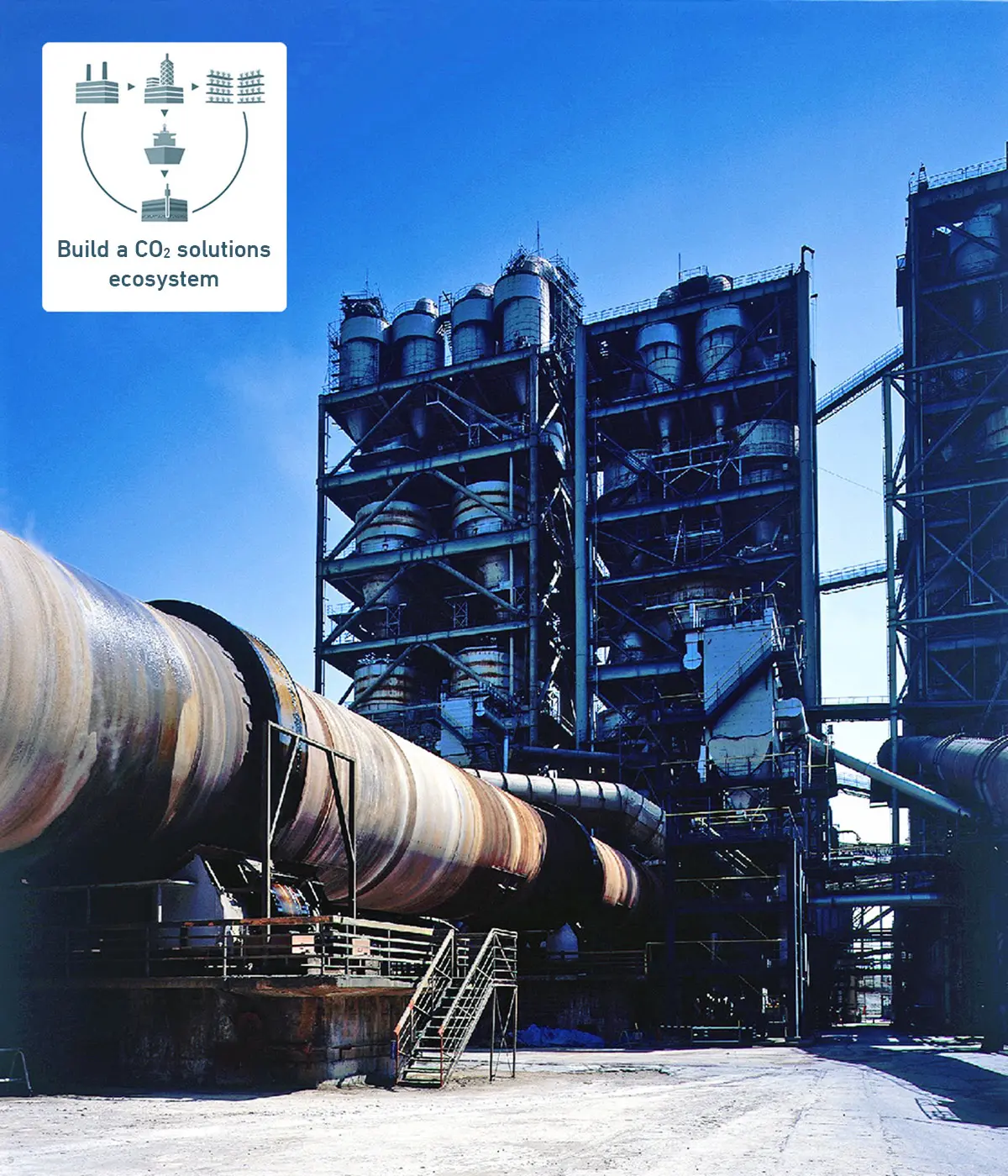
Testing times
CCUS can harness the emissions from cement manufacturing to help the industry realise its decarbonisation ambitions. While the technology is in its infancy, efforts are underway to scale up CCUS system deployment for cement manufacturing.
Mitsubishi Heavy Industries Engineering, a Mitsubishi Heavy Industries (MHI) Group company, has agreed to conduct a demonstration testing programme at an existing cement plant with the Tokuyama Corporation, one of Japan’s leading chemicals and cement manufacturers. A compact CO₂ capture test unit will be installed at Tokuyama’s plant in Shunan, Yamaguchi prefecture, and the testing is due to run for nine months from July 2022.
The CO₂ capture test unit — roughly equivalent in size to two 20-foot shipping containers stacked on top of one another — will harness CO₂ emissions from the plant’s flue gases, allowing the impurities in the gas to be analysed.
A small portion of the flue gas from the cement kiln is diverted to the CO₂ capture test unit, where hot gases are cooled by a quencher and then passed through a CO₂ absorber where the CO2 is captured by KS-1™ solvent, developed jointly by MHI and Kansai Electric Power Company. The CO₂-rich solvent is then pumped into a regeneration tower and heated to re-release the CO₂.
Although not part of this demonstration program, at this point, CCUS systems compress captured CO₂, which is then either stored or used in a range of industrial applications. For test purposes, the captured CO₂ will be returned to the stack once it has been analysed.
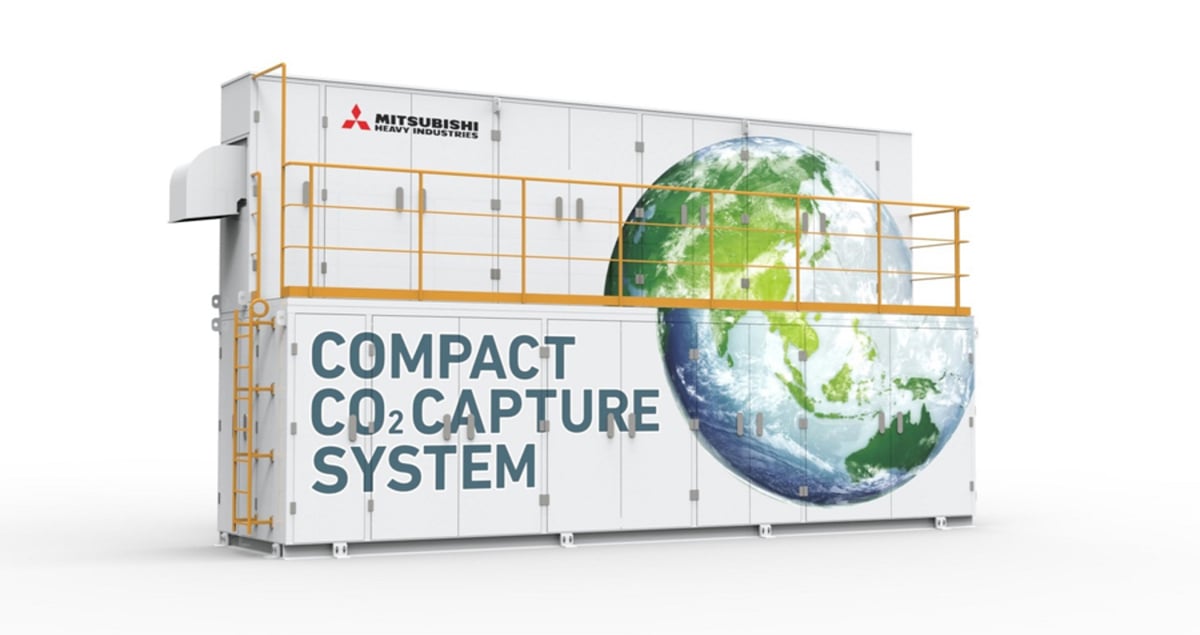
Capture capacity
The testing programme at Shunan aims to understand the effect of the cement kiln’s flue gas composition, using CO₂ capture process chemistry to understand any potentially adverse effect on the rates of amine solution consumption or on CO₂ capture performance due to impurity accumulation, as well as stable operation levels. This will provide essential data required for large-scale commercial application of CCUS technologies in the cement industry.
The CO₂ capture test unit that will be used at the plant has a modest capture capacity of 0.3 tonnes per day (TPD), a fraction of the cement plant’s typical emissions profile of between 3,000 and 5,000 TPD, but sufficient for testing purposes. It is designed to capture up to 90% of processed flue gas.
As these compact CO₂ test units can be easily transported from plant to plant, they can analyse a range of cement kiln emissions to gather data on plants that combust coal, natural gas, biofuel and other fuels as heat sources. The findings should help with the design of larger-scale permanent capture systems that maximise capture capacity and efficiency.
While it can design customized test units for customers, Mitsubishi Heavy Industries Engineering also offers a range of compact CO₂ capture systems, which brings with it many benefits.
The standard compact design can be manufactured in batches, ranging in size and capture capacity from 0.3 and 3 TPD all the way to 30, 100 and 200 TPD. Batch production helps to reduce both costs and delivery time. Being standardized, these compact CO₂ capture systems are also easier to transport and install than larger bespoke options, making them ideal for customers that have limited CO₂ capture and utilisation opportunities.
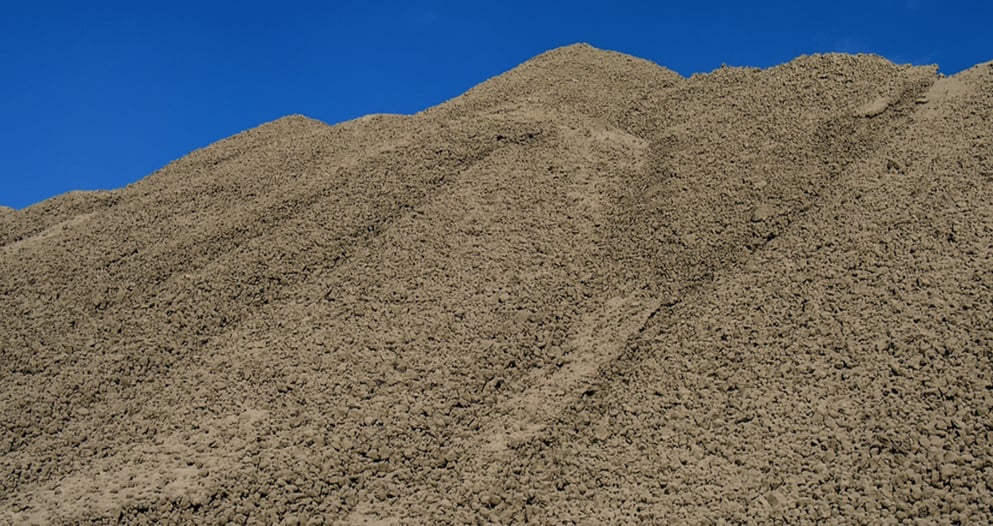
What happens next?
Nine months of accumulated know-how and experience from real-world operations will help inform plans to scale up this technology and deploy CCUS systems throughout the global cement industry.
As the IEA states, CCUS has a key role to play in helping the world reach net zero by 2050. And nowhere is this technology more important than in the cement industry.
While some hard-to-abate heavy industries can switch to cleaner fuel sources, like hydrogen, the cement industry’s reliance on CO₂-emitting limestone as a raw material leaves it set in stone, so to speak, making CCUS an essential tool.
Once CCUS systems are operating at scale, the bulk of captured CO₂ from cement and other industries will be stored securely, deep below ground. But a growing CO₂ value chain is developing that is turning this waste product from a liability into an asset. Captured CO₂ from cement industry flue gases can be injected into concrete as a raw material. It is encouraging to see these examples of the circular economy in action.
What is claimed to be the world’s first carbon-negative concrete has been produced in Japan. Called CO₂-SUICOM, it is capable of absorbing CO₂ in the curing process. Liquefied CO₂ is mixed with concrete while it is hardening, producing a strong product that stores a large amount of carbon dioxide. We could see a future where our walls and building blocks are also CO₂ stores.
Captured CO₂ can also be used in a growing number of other industrial applications, from chemical manufacturing to putting the fizz in carbonated drinks. Solutions such as CO₂NNEX digital platform — a joint venture between MHI and IBM — are being developed to analyse, record and verify volumes of captured, stored, transported, utilised and traded CO₂, connecting carbon emitters with offtakers in various industries.
Forward-thinking
Making captured CO₂ a tradable commodity could go some way to overcoming the main barrier associated with applying CCUS systems to the cement — or any other — industry, which is cost. While the global market for sustainably made concrete will certainly grow, many consumers may be reluctant to pay a “green premium” for concrete manufactured using CCUS.
But attitudes are changing as awareness of climate change increases. This can be seen in industry efforts to curb emissions: such as increasing the efficiency of kilns, switching from heavy-emitting fuels like coal to natural gas or biomass, and reducing the clinker-to-cement ratio (including a greater focus on blended cements).
Working in parallel with low-carbon technologies like CCUS, these efforts can help the cement industry decarbonise operations and realise a carbon-neutral world. But the question remains, is it happening fast enough?
Discover more about MHI’s compact CO₂ capture technology
Related tags
