Can factories and power plants be run from home?
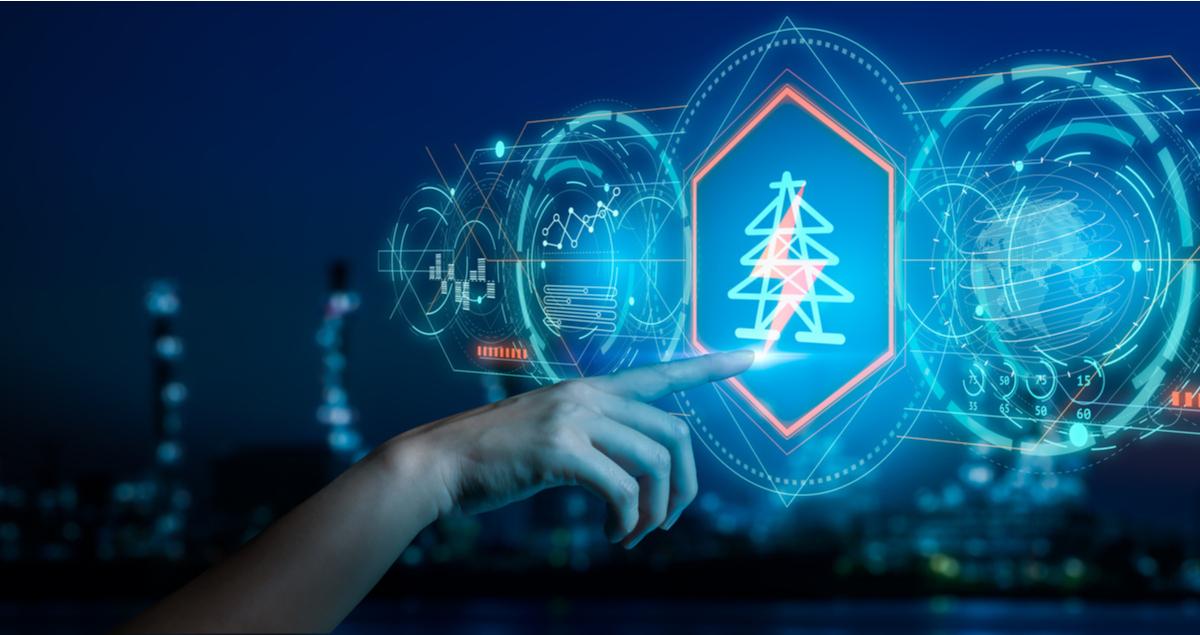
It has been called the world’s biggest remote-working experiment. Lockdowns in the wake of the COVID-19 pandemic have left many of us with no other option but to work from home. Even the greatest technophobes have taken to Zoom, Skype and Microsoft Teams in recent months. And it looks like – after decades of debate about the pros and cons of home working – we’ve finally proven it can be done.
But what if you’re in an industry where you simply have to be physically present, for example in manufacturing or power generation? Despite advances in digitalization and automation, running and maintaining steel mills, chemical works or power plants still relies on the presence of engineers on site.
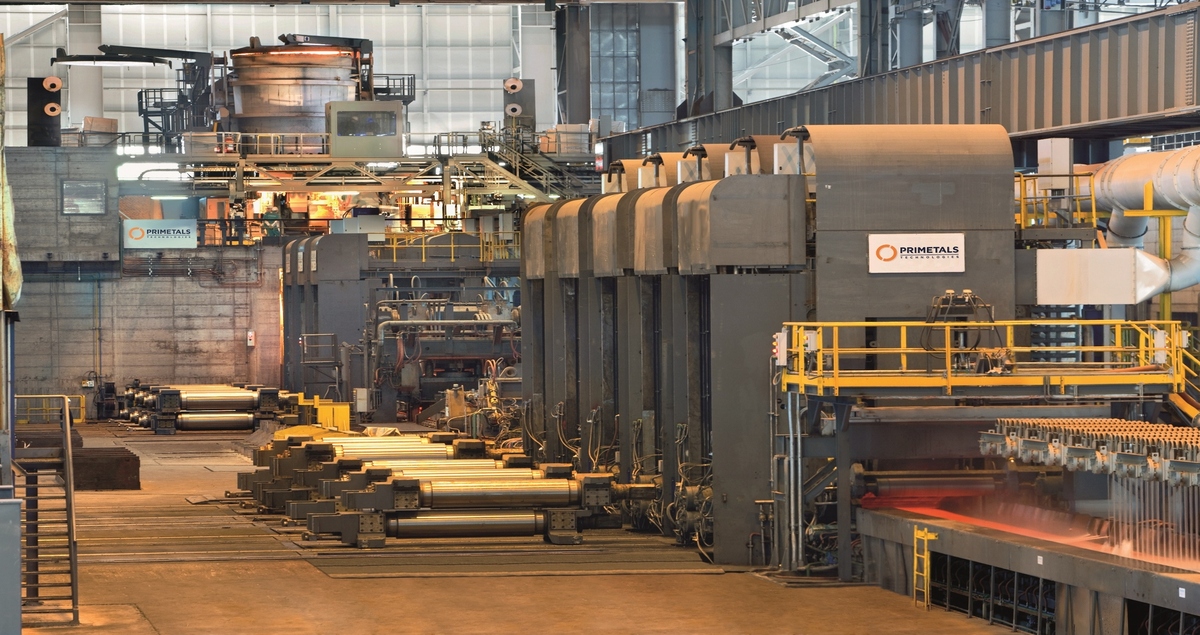
Smart glasses for smart steel plants
Commissioning new equipment for a steel plant is just one example of an industrial process that seemingly demands a physical presence.
In early 2020, Primetals Technologies, part of Mitsubishi Heavy Industries (MHI) Group, was ready to commission a casting-rolling plant designed for endless strip production (ESP); a new production line for ultra-thin metal strip in Fujian province, China.
Some of the equipment had been manufactured by a Chinese partner and key components needed to undergo the mandatory inspection and function tests before installation.
Typically, the next step would have been to fly out two specialists from Primetals Technologies’ nerve center in Linz, Austria, to carry out the inspection. But with China in lockdown, this was not an option.
To deliver the manufacturing line on time despite the virus outbreak, Primetals Technologies had to proceed with testing. But how?
The solution the teams in Austria and China came up with was to mount smartphones on industrial hard hats, so that the client’s own engineers could share what they could see via Webex with the experts back in Linz.
Remote commissioning required more than just technology, however; remote handholding was also essential for people on the client side who had less experience of the product concerned.
Successful completion of the commissioning in China means that further remote projects are now being lined up. One is already underway in Brazil and Primetals Technologies has now ordered smart glasses to be sent to commissioning customers, replacing the original ‘smart hats’.
“Most people are still working from their home office, but we have commissioning happening all over the world,“ commented Nicole Oberschmidleitner, head of mechatronic products at Primetals Technologies. In addition to plant commissioning, the company has also been using smart glasses to provide remote assistance to maintenance engineers and other on-site personnel when fixing production equipment.
Find out more about remote assistance and smart glasses by attending our webinar on Smart Assistance in the Steel Industry
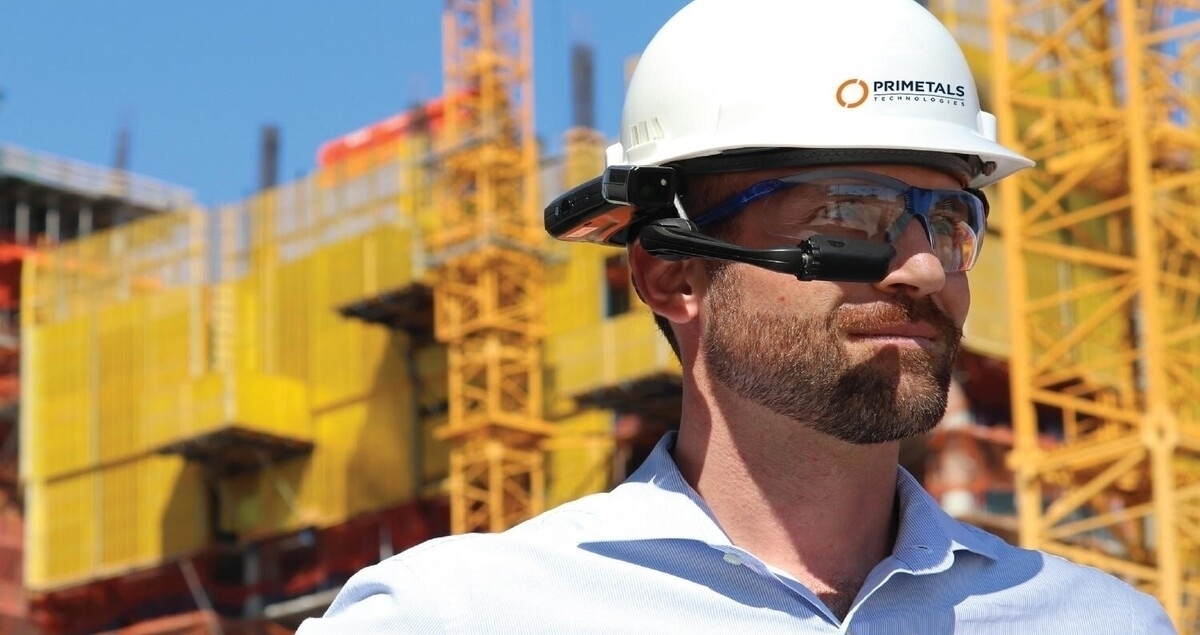
Mixed reality
Even without COVID-19 and travel bans, access to the “real thing” can be difficult.
This can be the case where, for example, products can’t easily be taken to a customer site for demonstrations.
MHI Marine Machinery & Equipment (MHI-MME) faced this challenge with its turbochargers and in response has started using Microsoft HoloLens 2.
These so-called mixed-reality headsets feature a multitude of sensors that capture the reality around the user and overlay it with holographic images – in this case, of turbochargers – to create an augmented reality that users can interact with in real-time.
It’s as close as trainees can get to experiencing real maintenance work without using an actual turbocharger and is a useful tool to help staff training in the future.
And MHI-MME is not alone.
“In industries like these, products are often heavy, high-value and of significant size. Therefore, it can be difficult or even impossible to put them in front of a trainee. Using HoloLens 2, trainees can see, walk around and interact with the product without it physically being there,” said Takesen Ito, co-founder and COO at HoloLab, a Japanese augmented and virtual reality solutions provider that worked with MHI-MME to develop the turbocharger training experience.
Keeping the lights on – remotely
Other essential services are also finding innovative ways of working from a distance.
Power plants keep the lights on and the rest of the economy’s video conferences going. But as with manufacturing, many aspects of their operation and maintenance still involve on-site visits – lockdown or not.
“It’s a challenge because a lot of the mechanical interventions require you to be there in person,” explains Marco Sanchez, head of intelligent solutions at Mitsubishi Power Americas.
Again, digitalization is helping address this by minimizing or even eliminating maintenance visits, as Sanchez observes.
Mitsubishi Power has operated remote monitoring and diagnostic centers for more than two decades, helping power companies find the best operating parameters for their plants, providing early fault warnings and scheduling preventative maintenance. Longer-term, these centers have the potential to deliver operational support and maintenance remotely, reducing the need for on-site visits.
A digital suite including remote sensors (Internet of Things), artificial intelligence (AI) and data analytics plays a key part in delivering expert support and helping plant operators run their power plants more efficiently, avoid costly outages and, as a result, stay competitive.
These kinds of tools will also enable power stations to be operated and maintained remotely as a next step.
Some power generators are closer than others to this goal. Sanchez mentions Altamira II in Mexico, which has rolled out an end-to-end system for plant monitoring that also enables its operator to adapt operations flexibly to business needs.
But this is just the beginning. The ultimate goal, says Sanchez, is an autonomous power plant. Such a plant doesn’t just throw up alerts and operational recommendations, it automates routine tasks and can self-optimize key operational parameters to ensure safe, reliable and cost-effective running of the plant.
While this may sound like science fiction, Mitsubishi Power is already working on the building blocks for the world’s first autonomous combined-cycle power plant. In Takasago, Japan, its new test and validation facility, T-Point 2, started commercial operation this summer. Connected to the local power grid, it is not only set to operate and maintain itself in the future, but also to boast the highest fuel efficiency levels in the industry.
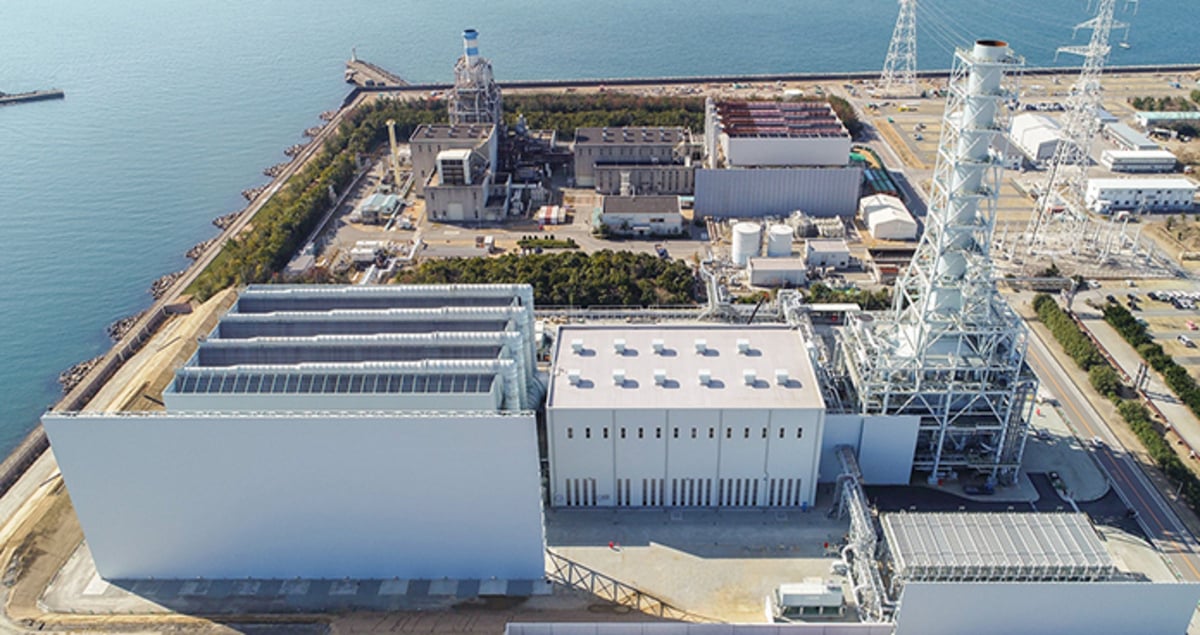
Where next for remote operations?
Marco Sanchez at Mitsubishi Power explains: “To make it happen requires a lot of technological strands to merge: cyber-secure communications, adequate bandwidth and access to the plant’s control systems, data and documentation. To run simulations and trial planned modifications, the use of virtual models of the plant – also known as ‘digital twins’ - is becoming more common. Last but not least, you also need at least some of the operator’s experts on hand – because we’ll still need that human factor, especially in a crisis.”
However, the experiences of recent months suggest that office communications and collaborative technologies are not alone in coming of age: the use of digital tools in industry is also rising to the coronavirus challenge.
During the peak of the COVID-19 crisis, when Mitsubishi Power was unable to send maintenance staff abroad, on-site personnel were able to carry out inspections and maintenance guided remotely by the company’s experts using mixed-reality headsets.
As Takesen Ito from HoloLab observes: “Because of social distancing, a lot of businesses are now searching for new ways to market their products. And one of the prospective solutions might be mixed reality conferences or events.”
We’ll likely look back and realize that the lockdown has helped us leapfrog technology advances that would otherwise have taken significantly longer to materialize.
Learn more about Digital Technology in Power Generation
Related tags
