From trash to SMASH - A smart approach to recycling waste
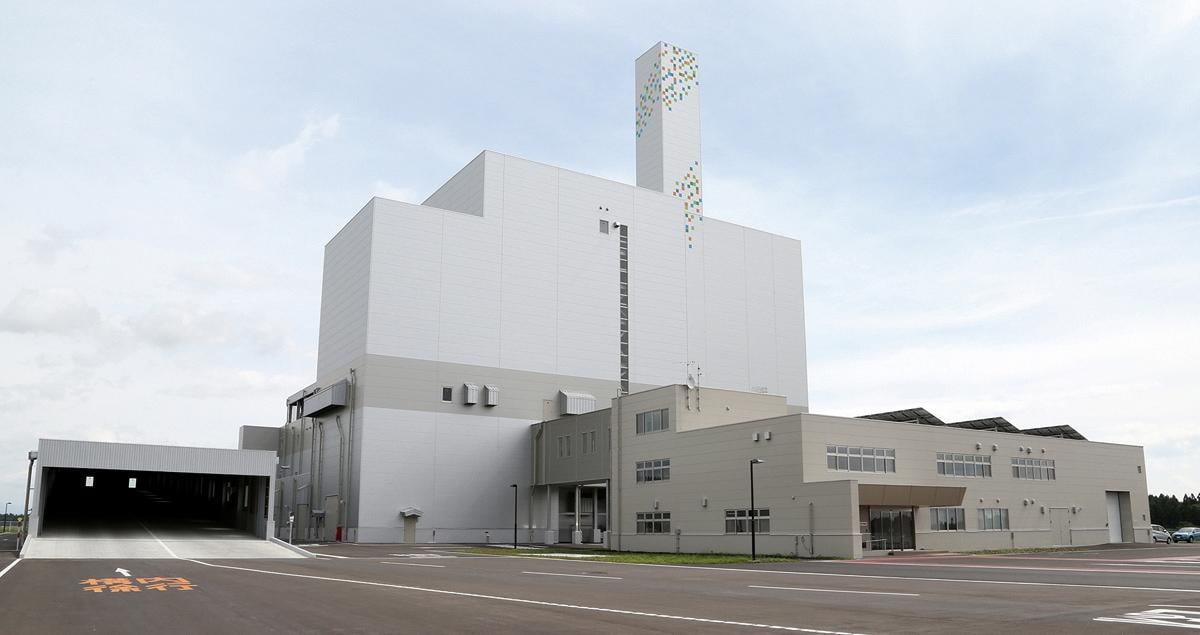
During Japan’s economic miracle decades of the 1960s, ‘70s and ‘80s, the nation experienced the fastest economic growth in the world. Consequently, the country climbed to number two in the global economic rankings, second only to the United States. One unwanted by-product of this success was the equally fast growth of the country’s waste, which soared to 44 million tons in 1980—five times the level generated in 1960, according to Japan’s Ministry of the Environment.
Faced with rising mountains of trash and escalating levels of hazardous pollution, the government took action and revised and enforced its Waste Management Act in the 1970s. Standards for private and municipal waste management facilities were raised, and the 3Rs scheme to Reduce, Reuse and Recycle waste was introduced and promoted vigorously. As a result, Japan, which had previously lagged well behind Europe and the United States in dealing with waste efficiently, has now vastly improved the sophistication of its waste treatment, while some of the waste management technologies it has introduced are among the most advanced in the world.
Several of these leading edge technologies can be found operating in the Iwate-Chubu Clean Center in Iwate Prefecture, in the northeast of Japan, helping turn it into a showcase for refuse treatment.
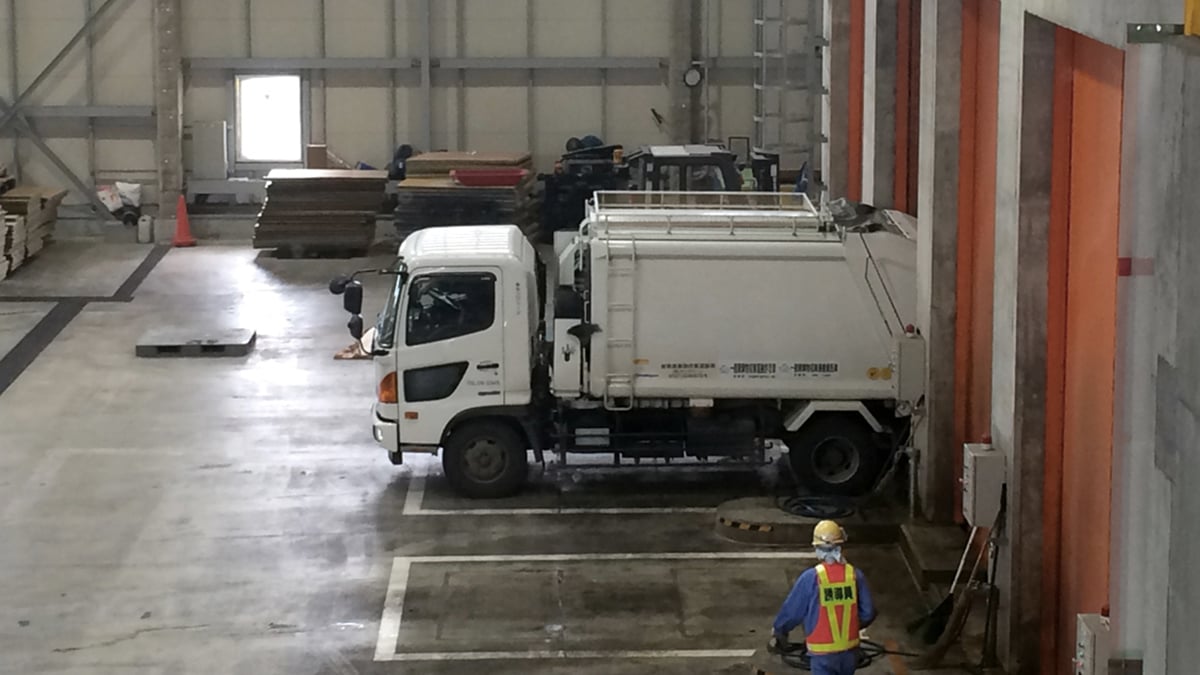
Recycle, SMASH and Reuse
The Clean Center is a US$84 million stoker type incinerator facility, which began operations in October of 2015. With a lean crew of only some 30 souls, the facility takes in waste, generates electricity from a steam turbine using the heat generated by incineration of the waste, and outputs non-toxic, low-chlorine ash that can be added as filler to concrete. Incineration of solid waste is considered the most practical approach and is the most widely adopted scheme in Japan, where two-thirds of the country is mountainous, which leaves little space for landfills when agriculture and living space are at a premium.
In the past, each Japanese municipality was responsible for dealing with its own waste, an approach now seen as impractical and uneconomical. By contrast, the Clean Center deals with refuse from four local municipalities in central Iwate, a response to a 1997 government report on the need for the development of “wide-area refuse-treatment” facilities.
The Clean Center features both advanced resource recycling systems and the SMASH (SMart ASH treatment) system developed by Mitsubishi Heavy Industries Environmental & Chemical Engineering (MHIEC), which turns incinerated ash into a stable supply of filler for cement used as a building material. As well as designing and constructing the facility, MHIEC also operates it through a special purpose company established for that reason. The facility uses twin incinerators able to treat a total of 182 tons of mostly household waste each day or 56,000 tons annually.
Heat from the incinerated waste is recovered and used to create steam superheated to 400° Centigrade to generate electricity via a steam turbine. Over a year, the system can generate 26 gigawatt-hours of electricity—the equivalent of powering some 5,500 average households annually. Approximately one-third of this output is used to run the entire facility, while the rest is sold back to the local power grid.
The purpose of the SMASH component of the system is to wash, clean and process the incinerated ash for final disposal—after metals have been recovered—to make it fully reusable, rather than wastefully disposing it in landfills, as is often the case with ash from conventional waste treatment facilities.
The SMASH process of repeated washing and cleaning not only reduces the chlorine content—a reuse inhibitor—in the ash by half compared to non-treated ash, it disperses the remaining chlorine evenly throughout the ash. The result, according to MHIEC, is that all of the ash at the Clean Center can be recycled for mixing with cement and cement products—an alternative to using clay. “It’s used in ordinary cement as a raw material that meets the JIS or Japan standards for cement factories,” said a spokesperson for MHIEC. “The resulting ash is used as one of the raw materials for cement.”
To achieve a high level of heat recovery during incineration, an advanced technology called Internal Gas Recirculation (IGR) is employed as a secondary combustion air supply. It combines recycled combustion gas from the furnace with a rich supply of oxygen to feed the furnace during combustion or ember-combustion process. IGR also works in combination with an advanced combustion control system to eliminate the need for a secondary air fan. More importantly, it enables the furnace to operate using a lower ratio of air. As well as improving the efficiency of heat recovery, less air during combustion reduces the amount of exhaust gas produced, which in turn means a more compact flue-gas-treatment system can be used.
In addition to these benefits, the higher level of heat recovery obtained from incineration increases the amount of electricity generated from each ton of waste by two to three percent compared to conventional furnaces, which significantly improves the facility’s running costs over time. “By adopting the low air ratio combustion technology with the latest combustion technology of the IGR system, we were able to improve the power generation efficiency over traditional methods from the excess heat produced during the incineration of waste,” said the MHIEC spokesperson.
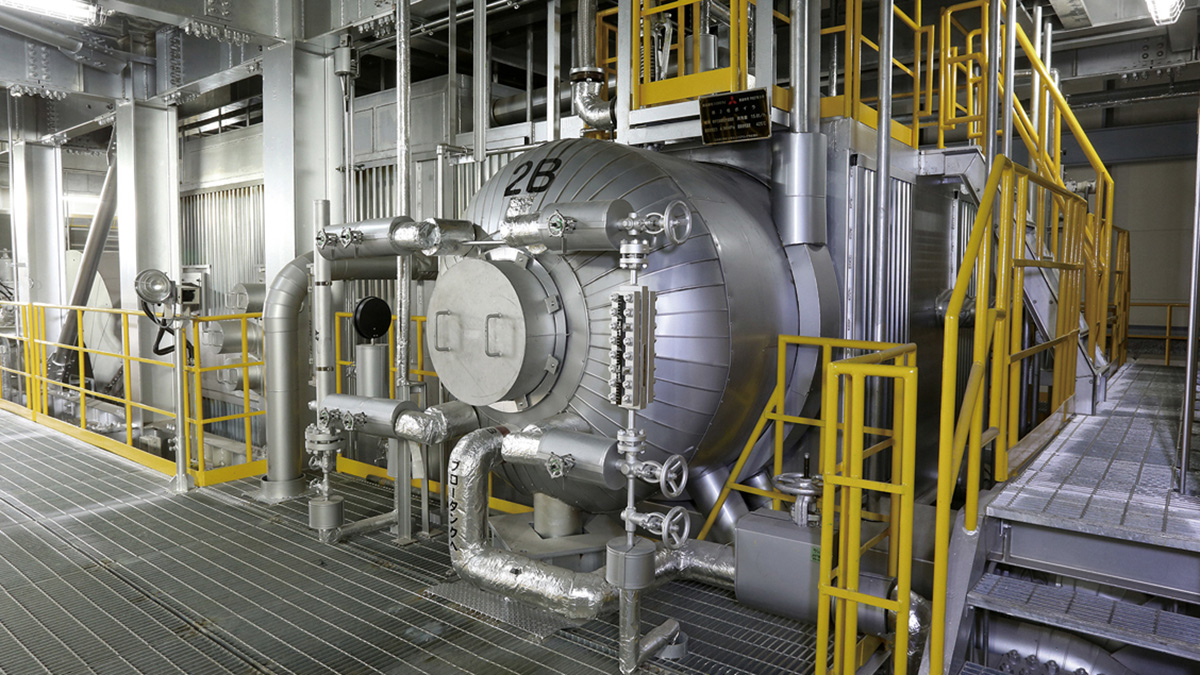
Disaster Relief Base
The Clean Center is also designed to make practical use of the plant’s empty space. This is accomplished through the construction of a large-scale solar power generation system. The system generates an estimated 90 megawatt-hours annually—the equivalent of powering 19 average households each year.
Also, the facility is equipped with a large capacity diesel turbine to power the plant in the event of a natural disaster—such as when an earthquake might disrupt electric power in the region. This enables self-sustaining operations. Consequently, the Clean Center can continue functioning as a waste treatment facility and help prevent the accumulation of waste that too often build up quickly during prolonged emergencies and which can turn hazardous.
Furthermore, the solar power generation system working in combination with a power storage system of large lithium ion batteries can produce electricity for emergency use even when the waste power generation system is offline. This enables the Clean Center to take on the role of a community shelter and relief base during times of emergencies.
This creates added value to for the community, which also benefits from the core activities of the Center. “It provides for sanitary living while contributing to the environmental sustainability of the local community through a stable method for processing refuse,” the MHIEC spokesperson said. “What’s more, the heat generated by waste incineration produces electricity as renewable energy. The Iwate-Chubu Clean Center has also established an education base, as information is distributed and inspires activities in the region.”
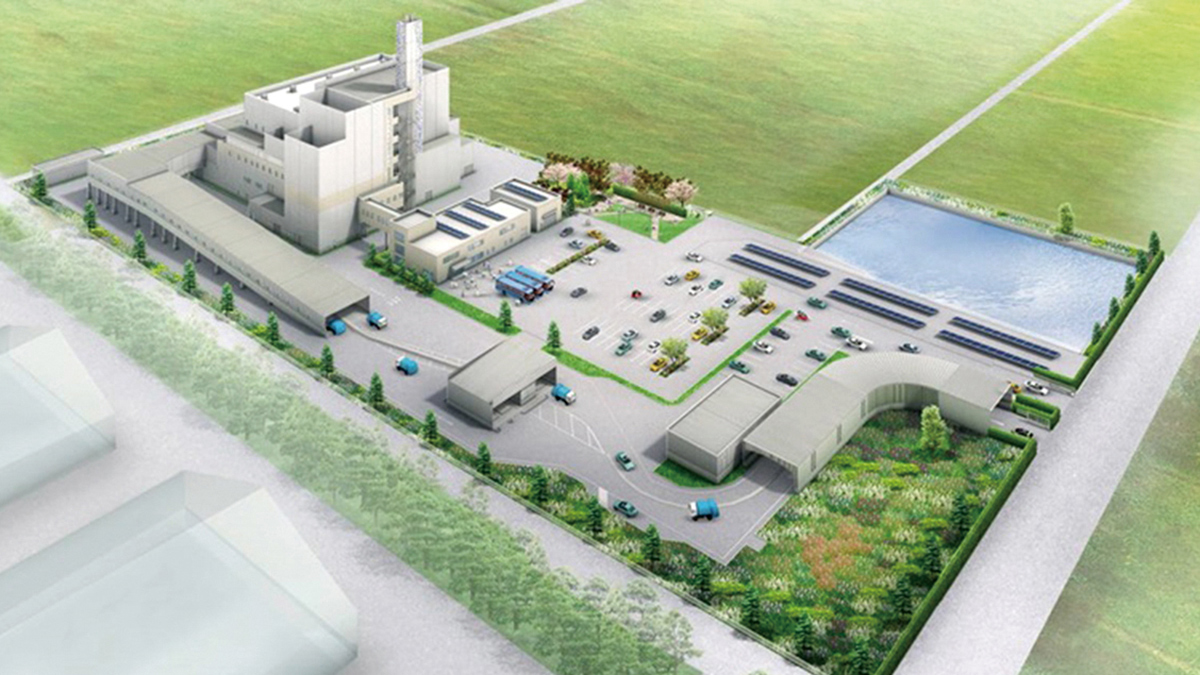
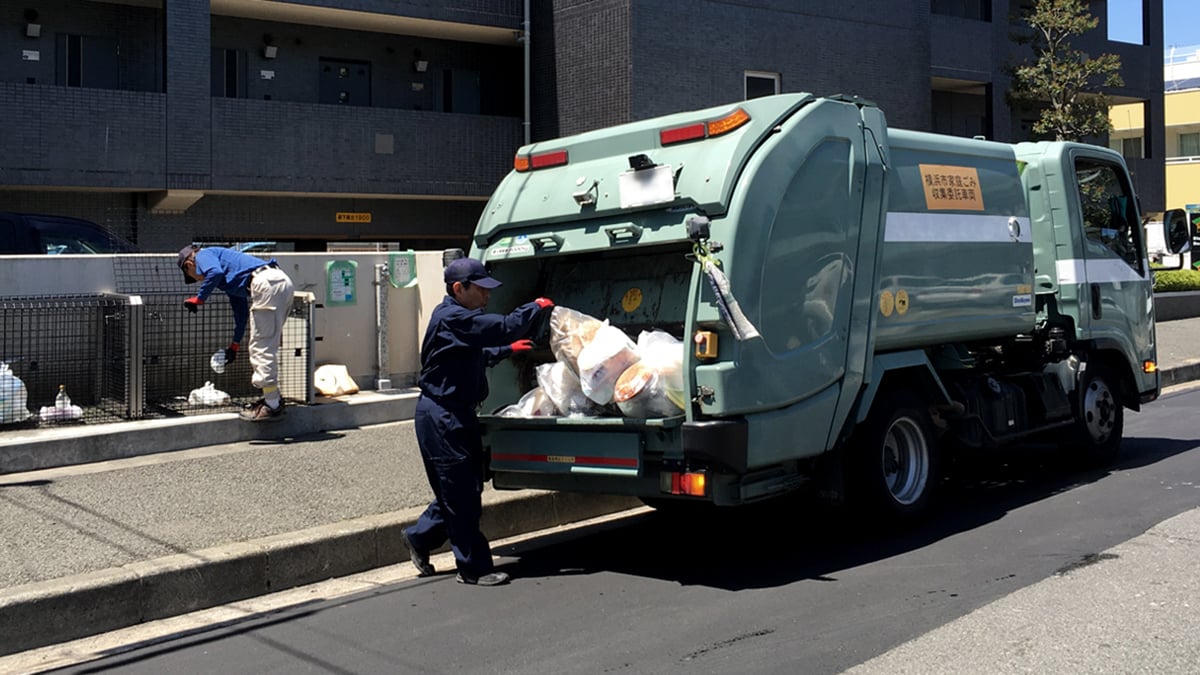
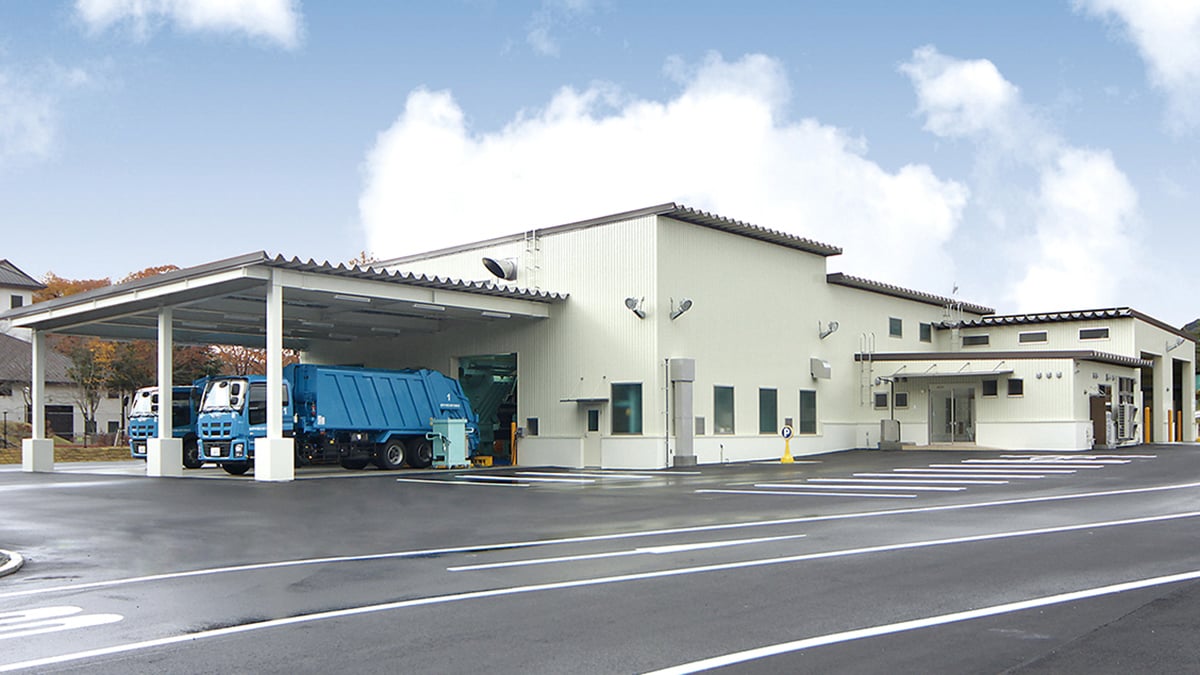
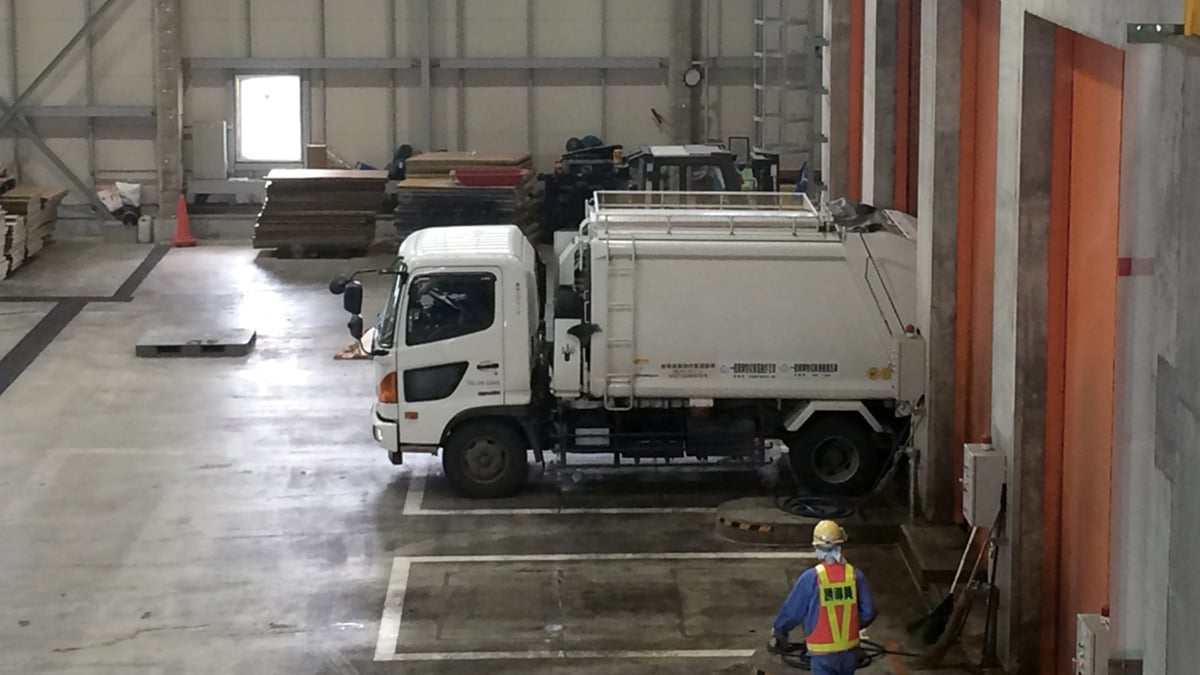
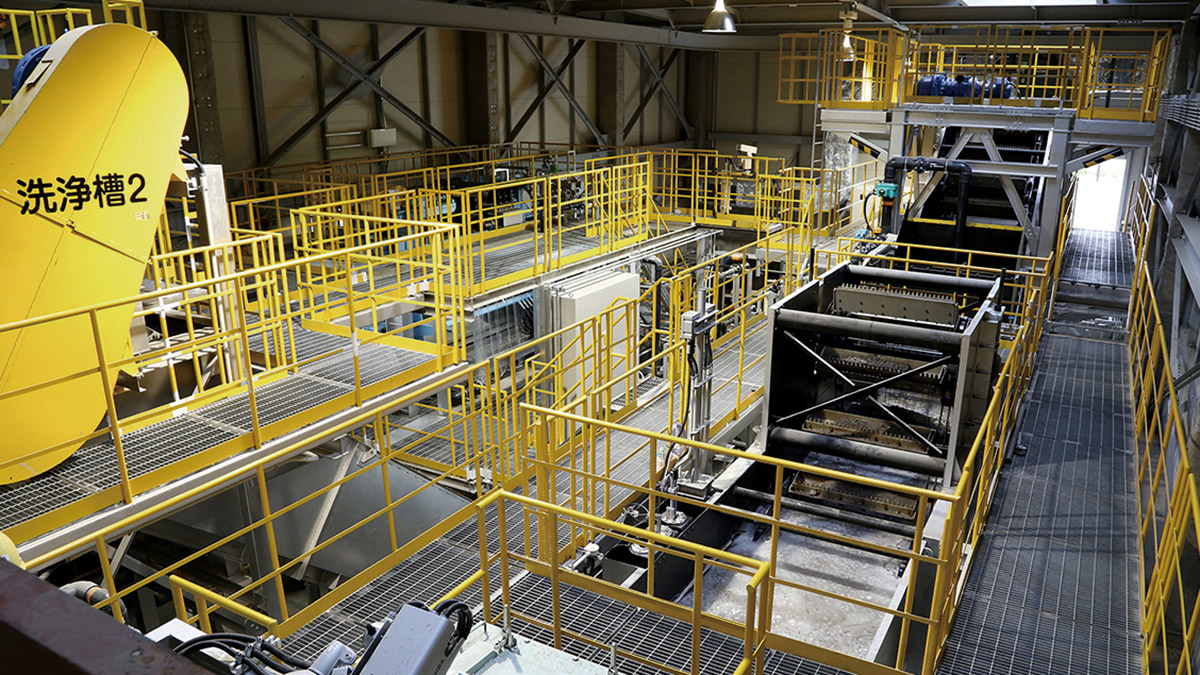
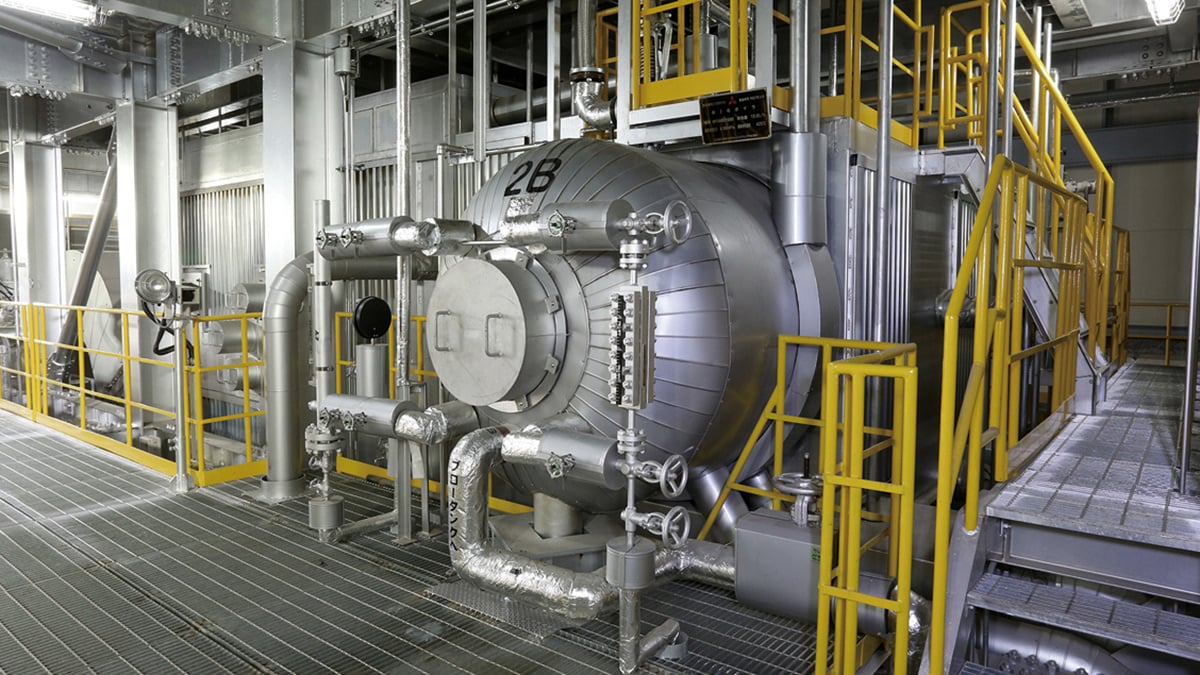
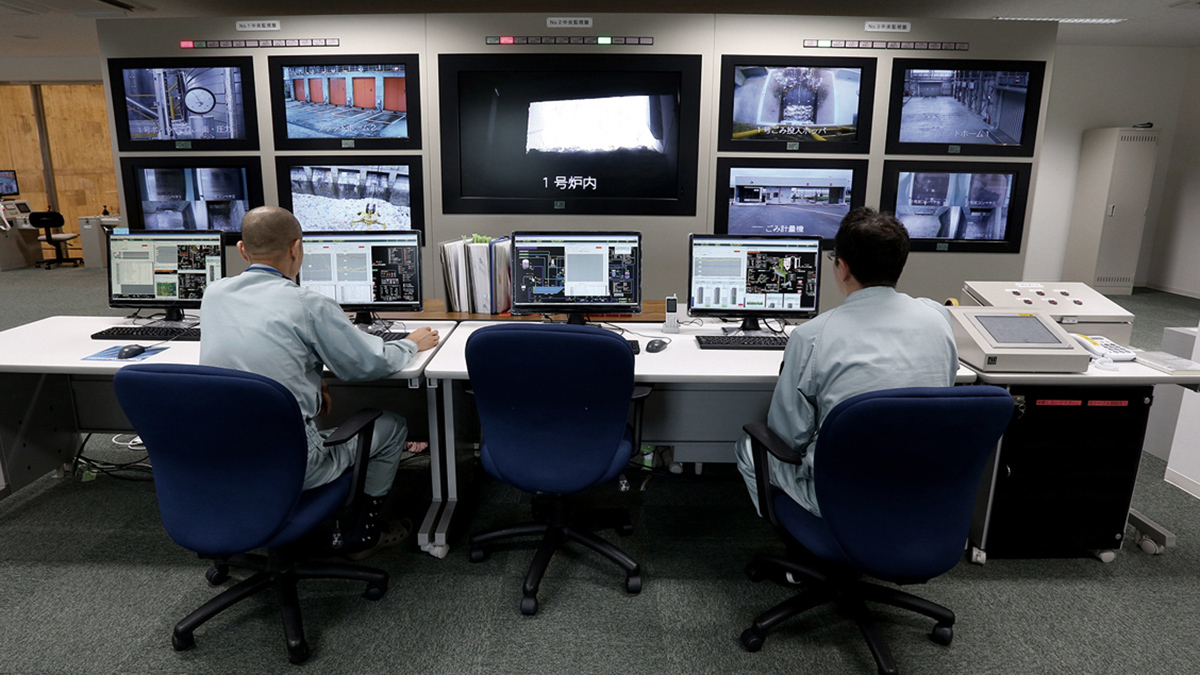
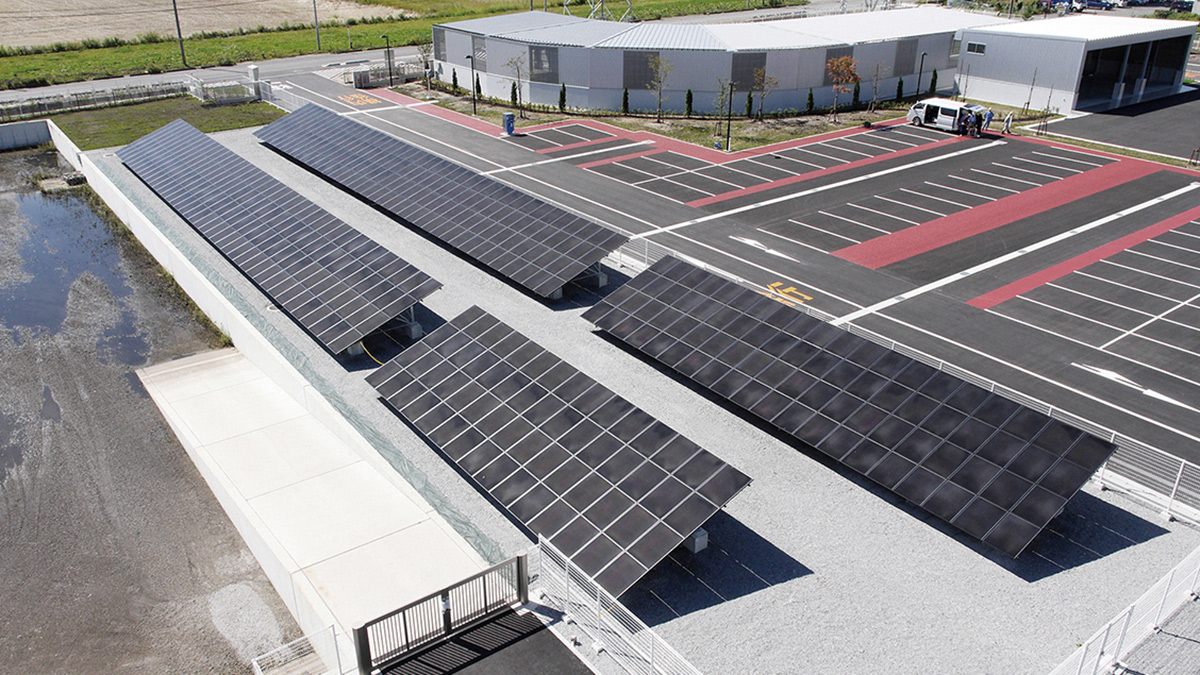
Related tags
