A Lifeline into Space
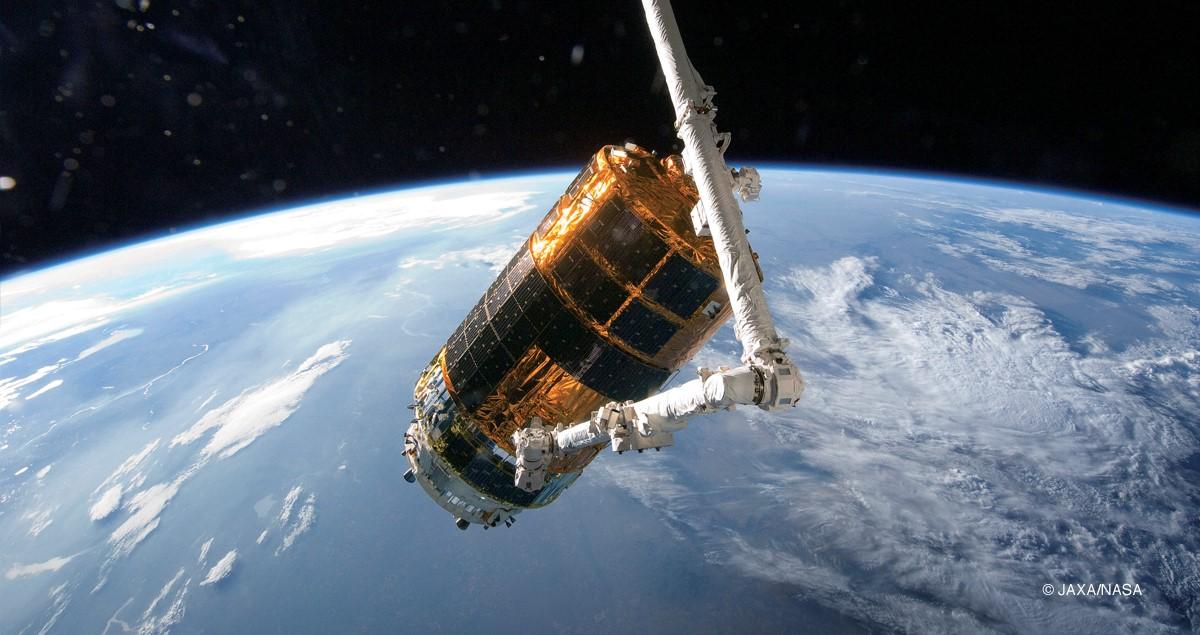
Japan’s golden, shiny resupply vehicle began with the International Space Station (ISS) project.
In 1984, the United States proposed a project to build, in concert with international partners, a “space base where people can live” for long periods of time. This ambitious proposal with the aim of furthering scientific and technical knowledge and helping improve life on earth heralded the outward trek in human space exploration on a grand scale. An alliance of 15 countries has been cooperating on the International Space Station (ISS), designed to enable experiments in space and scientific observations of our planet and other celestial bodies. Construction of the ISS in orbit got under way in 1998 and was completed in July 2011. A steady supply of goods is crucial to a prolonged stay in the ISS. Equally vital is the disposal of waste materials. To meet those critical needs, Japan independently developed the H II Transfer Vehicle (HTV), an unmanned supply spacecraft nicknamed “KOUNOTORI.” Carried aloft on the H IIB launch vehicle, the HTV transports food, clothing, and a variety of experimental equipment to the orbiting complex. Waste items, including unnecessary equipment and used clothing, are loaded onto the HTV, where they burn up along with the spacecraft upon reentry into the atmosphere. Although the U.S. and other countries questioned the HTV’s feasibility when the project began in 1995, a superb track record has since proven its capabilities. What is more, the HTV is the only cargo transfer spacecraft capable of delivering large sized experiment equipment and supplies now that the U.S. National Aeronautics and Space Administration (NASA) has retired the Space Shuttle fleet. The HTV is definitely a lifeline to the ISS. The ISS crew eagerly awaits the approach of the visiting craft, reflecting golden light in space. It is a steadfast ally for those who live and work far away from home.
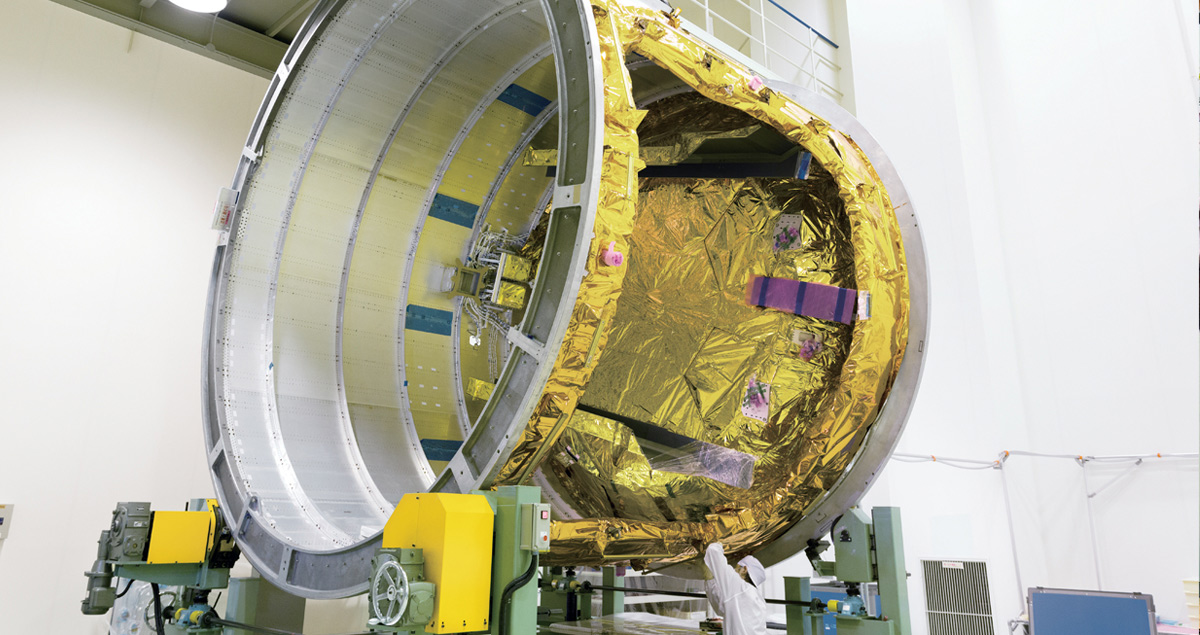
All the technologies developed for launch vehicles, space stations, and satellites are refined in the HTV.
The HTV represents the fruit of space technology developed by MHI and other manufacturers under the direction of the Japan Aerospace Exploration Agency (JAXA). It brings together knowledge of manufacturing and systems gained in the production of launch vehicles, space stations, and satellites. As the HTV prime manufacturer, MHI coordinated with more than 300 companies. MHI completed the massive, complicated vehicle within the weight that can be carried into space safely by an H IIB launch vehicle. At 4.4m in diameter, 9.2m in length, and 16.5t in weight, the HTV comprises roughly 1.2 million parts. The structural design emphasizes strength and lightness, so the HTV can withstand vibration during launch and acceleration as high as 3.2G while allowing bigger loads to be delivered. The HTV is equipped with a pressurized logistics carrier that holds daily supplies and experiment materials, an unpressurized logistics carrier for large hardware and supplies to be used outside the ISS, an avionics module, and a propulsion module. The modules are manufactured at separate factories and assembled at the JAXA Tanegashima Space Center into an enormous sized space vehicle.
HTV innovations push Japanese space technology to the forefront
The engines roar, and the H IIB launch vehicle ascends with enormous thrust. Fifteen minutes after liftoff, the HTV separates from the launch vehicle en route to the ISS. It arrives a week later. Once mated and unloaded, the space freighter accepts the orbiting station’s refuse. It then undocks and separates from the ISS. The mission ends abruptly and successfully in incineration when the spacecraft and its contents reenter earth’s atmosphere. The proposed mating method for the HTV took NASA by surprise at the outset. Called “capturing and berthing,” the new concept was totally different from the “docking method” employed by space shuttles. It involved a robotic arm capturing and maneuvering the vehicle into position for berthing. Nevertheless, this Japanese initiative excited U.S. and Canadian engineers in charge of the robotic arm. Many years of cross border collaboration and careful coordination led to capturing and berthing becoming the preferred technique. The United States, a nation steeped in space exploration history, has adopted the method for the Dragon and Cygnus unmanned resupply spacecraft. Four HTVs (HTV1 through HTV4) have embarked on missions since 2009. Each completed its tasks as scheduled. Under the JAXA contract, MHI plans to launch three additional HTVs up to vehicle No. 7. As a leader in revolutionizing space technology in Japan, MHI manages all stages, from manufacturing to launching the HTV to supporting flight operation. HTV technology will enhance Japan’s standing in the space business and open the doors to manned space flight.
Related tags
