5 innovations building a more sustainable future for cement
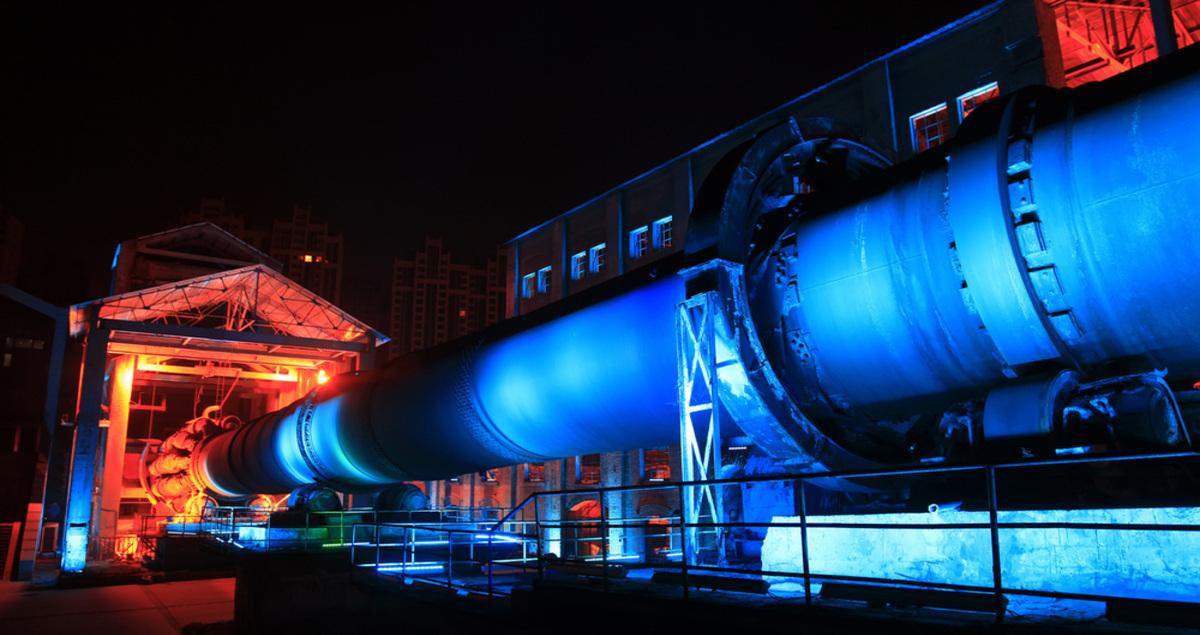
Look around you. Cement is everywhere, forming a core building block of the houses, offices, schools, hospitals, roads, bridges, ports and myriad other structures that surround us.
However, the cement industry is facing a problem. Its carbon-intensive production processes generate up to 8% of global CO₂ emissions, and while the sector has pledged to turn carbon neutral by 2050, cement demand is due to increase at around twice the rate of global population growth by mid-century.
On top of this, the direct CO₂ emissions intensity of cement production has barely changed in the past five years. Annual reductions of 4% are needed to get the sector into line with the International Energy Agency’s (IEA) scenario for global net zero emissions by 2050.
So, how will the industry become more sustainable? Here are some of the technologies that could help cement manufacturers meet their goal of a cleaner future.
Capturing cement CO₂ emissions
The IEA has identified carbon dioxide capture, utilization and storage (CCUS) as a key technology to help decarbonize cement production.
Mitsubishi Heavy Industries (MHI) Group is installing a compact pilot CO₂ capture system “CO₂MPACT” at a cement plant for Heidelberg Materials in Edmonton, Alberta, Canada. The project is expected to become the world’s first full-scale CCUS solution for the sector.
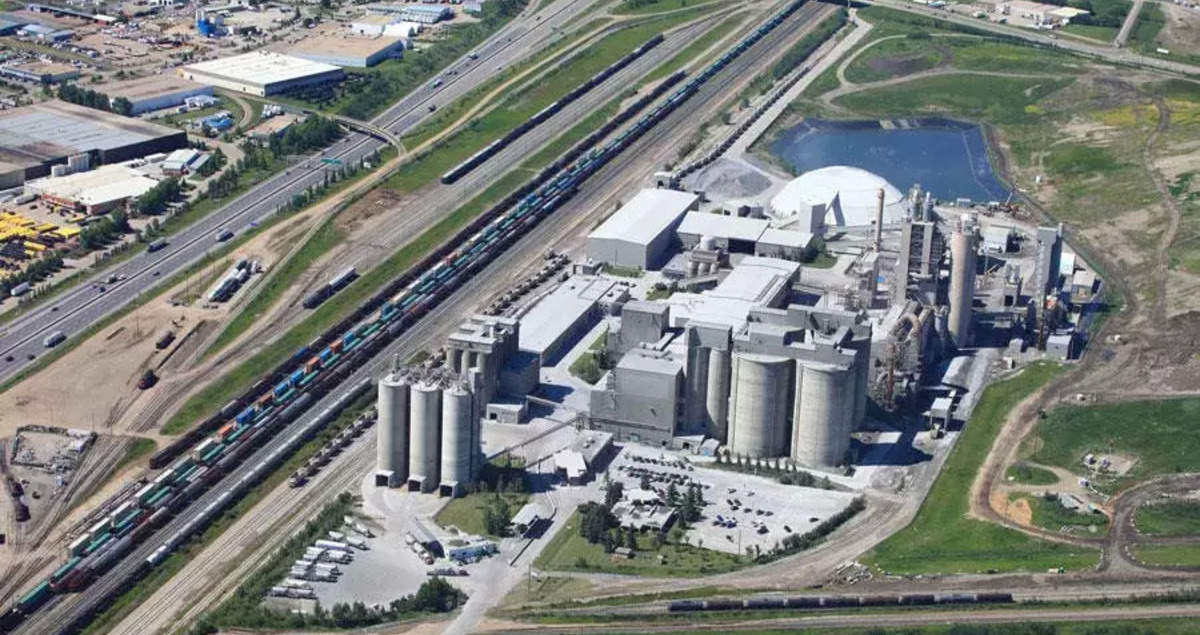
The facility is expected to be operational in late 2026 and able to capture more than 1 million tonnes of CO₂ a year from the plant and a combined heat and power system integrated into the capture process.
Waste heat recovery
Recovering and utilizing waste heat from cement plants helps to reduce the amount of fossil fuels needed to heat raw materials to extreme temperatures during the production process.
MHI group company Turboden is installing an Organic Rankine Cycle (ORC) waste-heat recovery system at a cement plant in Fujairah in the United Arab Emirates. It is due to start up within 2024 and could prevent 29,000 tonnes of CO₂ emissions annually, which is equivalent to a 28% reduction in power-related emissions.
Electric kilns and electrochemicals
Advances in electric kiln technologies could provide a more sustainable way of producing heat-intensive high-grade cement without relying on heavy-emitting fuels such as coal and petcoke.
Several trials are in development in the US and Europe that aim to produce quality cement at scale using an electric kiln powered by clean renewable energy. While this may require battery storage to optimize energy usage and reduce costs during peak tariff periods, it could remove an estimated 45% of the carbon emissions associated with cement production.
For this solution, electrochemical reactions are used to make the cement, rather than at high temperatures, eliminating the need to burn fossil fuels. The startup says the process can reduce emissions associated by 90% if run at scale.
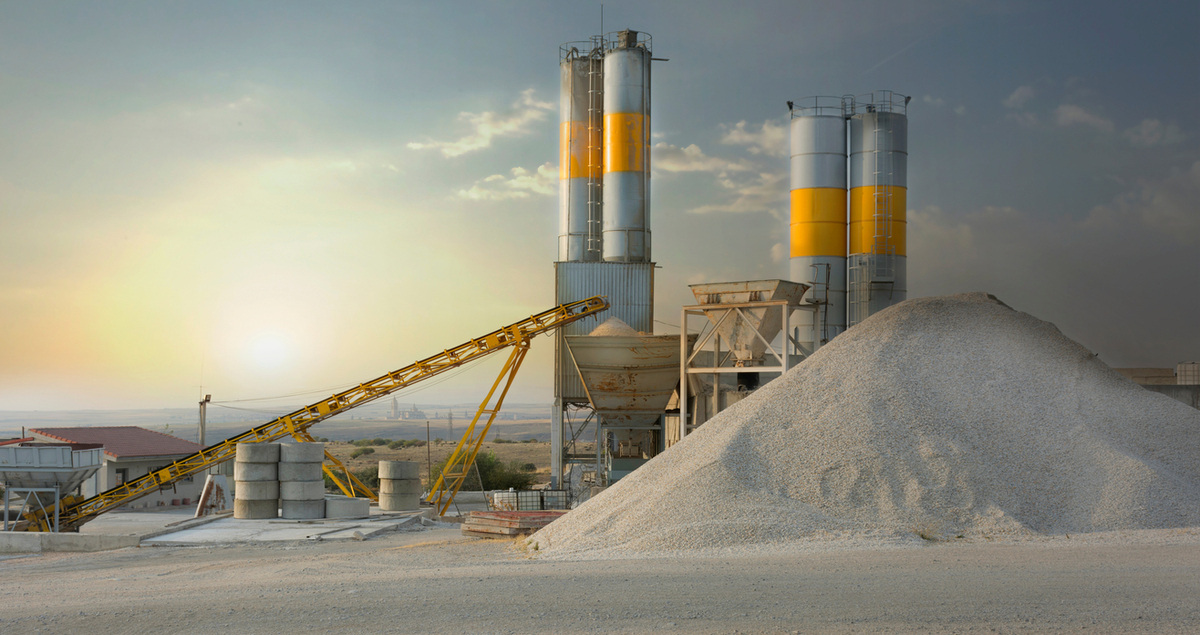
Concrete and the CO₂ ecosystem
Reducing CO₂ emissions from cement production is only part of the industry’s drive for carbon neutrality, as any emissions created will also need to be stored. That’s where clever concrete comes in.
Scientists in California are heating crushed limestone to naturally absorb CO₂ from the atmosphere. Combining this with concrete ingredients results in the captured CO₂ turning into a mineral that makes the concrete stronger. This reduces the need for cement, which is the element of the concrete manufacturing process with the largest carbon footprint.
While the solution remains at the test stage, once scaled up, it could provide a way to both remove CO₂ from the air and fix it for the long term in concrete buildings and other infrastructure.
Technologies such as this could be key building blocks in creating a sustainable cement industry that can meet the demands of a growing population in the years to come.
Discover more about various applications of MHI’s CO₂ Capture Technology
Related tags
