三菱重工高砂製作所、世界一のガスタービンを生み出すマザー工場 ~Home of the gas turbines at the heart of MHI and the energy transition~
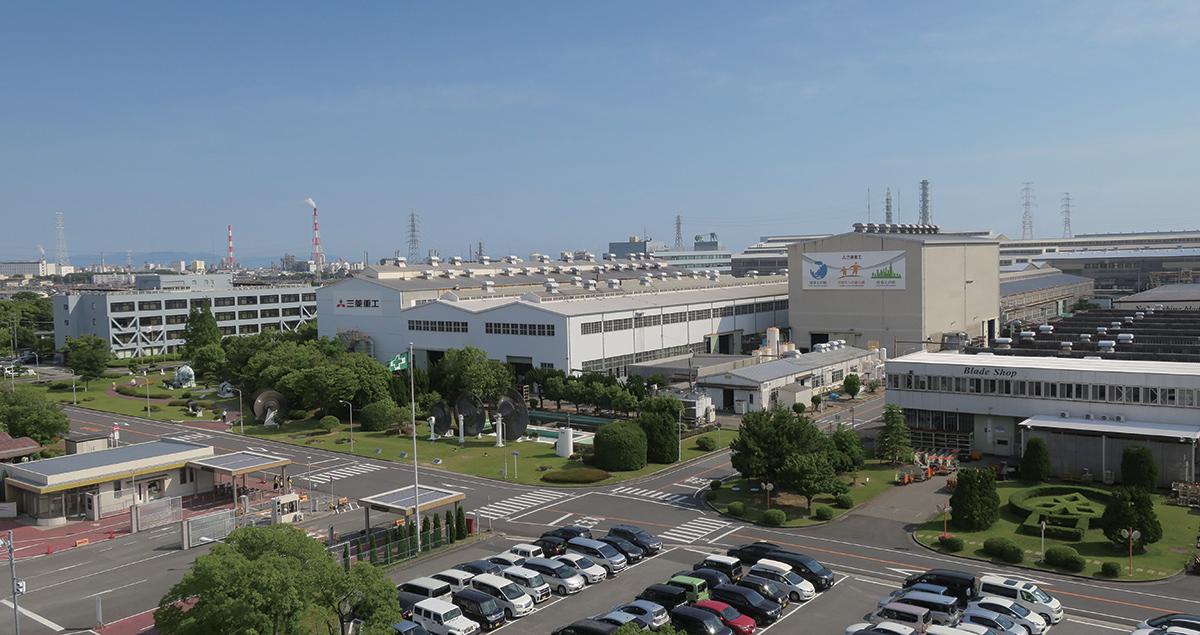
兵庫県の播磨灘沿いに立地する、三菱重工 高砂製作所。ここは、三菱重工グループが世界をけん引するガスタービンのマザー工場です。100万平方メートルを超える広大な土地には、オフィスビルの他、機械加工工場や各種試験施設、巨大な組立工場など、30棟を超える建物・施設が揃っています。
総勢5,000人。日本人の他にも様々な国籍の従業員が働く高砂製作所には、イスラム教の人々のために礼拝堂が用意されるなど、従業員のニーズを満たすあらゆるものも揃っています。そして何より、外部から訪れた私にとって印象的だったのは、工場内から絶え間なく響きわたる機械の音と忙しく働く人々の姿でした。
高砂製作所が誇るものづくり
操業開始から60年という歴史の中で、高砂製作所では常にタービンを主力として製造しています。特に現在では、発電所向けの「ガスタービン」が大半を占めています。その構造は航空エンジンと同様に、大きく3つの構成要素からなっています。まず1つ目が圧縮機です。回転する動翼と、回転しない静翼で、空気を吸い込んで圧縮します。2つ目が燃焼器です。圧縮されて高圧となった空気に燃料を噴射し、燃焼させます(現在は天然ガスを燃料として使用していますが、今後は水素やアンモニア等を含む、より環境に優しい燃料に切り替わる予定です)。そして、3つ目がタービン部分です。圧縮機部分よりも構造が複雑な動翼と静翼で構成されています。これを高温・高圧のガスが持つエネルギーで動翼を回転させることにより回転エネルギーを得て、最後に発電機で電力に変換する、という仕組みです。
これらは比較的シンプルな構造にも思えますが、そこには高度な技術が隠されています。ガスタービンを構成するのは、実に様々な部品。その一つひとつが、燃焼工学、加工工学、流体力学、材料工学など幅広い専門知識に基づいて設計・加工されます。素材もまた多種多様で、金属製もあれば、セラミック製もあります。特許化された金属粉末を調合して3Dプリンターで製作した部品の活用も増えています。
また、圧縮機には音速を超える速度で空気が流れ込んでいくため、圧縮機翼の表面に損傷を減らすためのコーティングが施されています。さらに、タービンの動翼・静翼には、最高1,650度の高温ガス流にさらされても耐えれるように、翼表面を冷却するための数十個もの小さく、かつ大きさや形状がそれぞれ異なる空気孔が施されています。メイドインジャパンならでは、そして三菱重工ならではの精緻なこだわりが、部品の一つひとつに込められていますが、これらは"設計した部品を試験し、改良し、再設計する"という終わりのない「改善」のプロセスを繰り返した結果なのです。
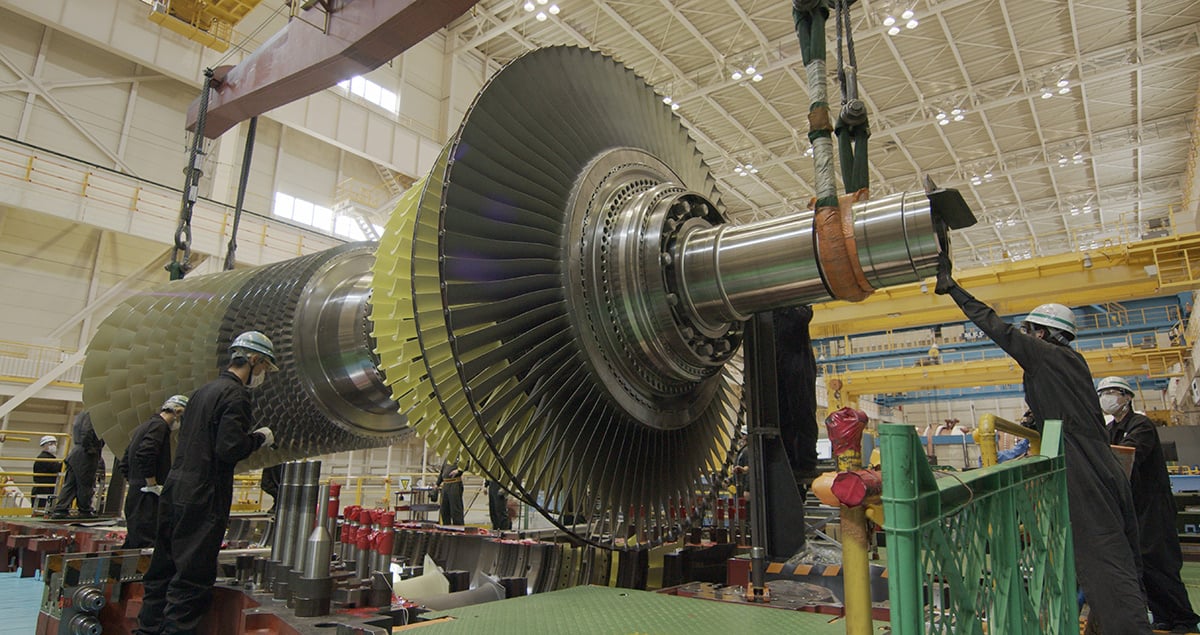
そのような技術の結晶とも言えるものが、世界トップクラスの発電効率を誇るJAC形ガスタービンです。金属製の車室に収まると、その大きさは路線バスほどになります。重さは600トンを超え、コンバインドサイクル運転によって最大84万kWという驚異的な発電能力を発揮します。これは、一般的な風力発電所や太陽光発電所を凌ぎ、原子力発電所に匹敵するほどの出力です。『Gas Turbine World(ガスタービンワールド)』によれば、このJAC形ガスタービンは、ヘビーデューティ型(一定の出力を維持して長時間運転することを前提として設計されたガスタービン)の中でも、世界で最も発電効率の高いガスタービンなのです。
しかし、世界レベルのものづくりを支えるのは、製造技術・設備だけではありません。高砂製作所には、研究や開発、設計や検証など、様々な技術・設備が同一敷地内にすべて揃っており、研究・開発の成果を設計、製造に活かし、実際に検証するというプロセスを高速で回しているのです。例えば、第二T地点と呼ばれる実証発電設備では、地域の電力網に接続された状態で、長期にわたってガスタービンの実証試験を行うことができます。実際の運用にこれほどまで近い形で、かつ長期的に信頼性を検証できる設備は世界でも他にありません。こうした仕組みがあるからこそ、高砂製作所は、効率的な開発と高い信頼性をスピーディーに実現することができるのです。
環境に優しいガスタービンの開発
高砂製作所では、今、新たな開発に着手しています。それは、ガスタービンによって発生する二酸化炭素排出量の削減です。従来型の石炭焚きボイラーに比べると、最新のガスタービンは、二酸化炭素の排出量を1/3ほどに抑えることができますが、現代社会が求めるのは、更にその上の「脱炭素化」です。三菱重工では、そうした世界のハイレベルなニーズに応えるべく、水素をはじめとしたクリーンな燃料を燃焼できる新型モデルの開発をスタートしました。現段階では、30%水素混焼の開発を完了、50%水素混焼の試験が成功しており、2025年までには4万kW級で100%、その5年後の2030年までには大型の45万kW級で100%の水素燃焼を目指して、日々開発を進めています。水素を専焼するためには、従来とは異なる燃焼器が必要となり、技術的に様々な改良が求められるため、容易ではありません。しかし、既に2022年6月に、米国にあるマクドノフ・アトキンソン発電所で世界最大となる20%の水素混焼の実証を成功させています。
これまで天然ガスから水素への燃料転換についてお話しましたが、高砂製作所では、アンモニア燃料のガスタービン開発にも着手しています。アンモニアは、特に日本やアジア太平洋諸国において、炭素を排出しない燃料として注目されています。しかし、水素とは化学的に全く異なる性質を持つため、それに適した別の燃焼器を開発しなければなりません。
高砂水素パークの建設
水素ガスタービン開発における当面の課題は、開発したガスタービンをテスト燃焼するための水素を十分に確保することです。現在使用している水素ローダー(水素の入った巨大な容器)では、わずか1時間の燃焼試験でも補充が必要になります。そこで、高砂製作所では、水素製造設備を新たに建設することが決定されました。電気分解装置などを用いた水素製造設備、水素貯蔵設備、水素を供給する配管などを備えた『高砂水素パーク』として、すでに建設がスタート。これが完成すれば、長期に及ぶ実証試験も滞りなく実施でき、開発が加速することが期待できます。
遠隔監視システム『TOMONI HUB』
最後にもう一つ、高砂製作所の魅力的な設備を紹介しましょう。その名も『TOMONI HUB』です。これは、IoTやAl技術を活用しプラントの運転情報を元にしたインテリジェンスソリューションの総称で、高砂製作所内に運用保守の高い知見を持つエキスパートが集まり、世界中の発電所で稼働する180基以上のガスタービンを、24時間365日監視しています。この遠隔監視システムに収集される膨大なビッグデータをもとにTOMONIのチームは、保守上の問題が実際に起きてしまう前に顧客に注意を促すことができます。また、ガスタービンの運転状況を精緻に読み解くことで、数百万ドルの節約につながる運転性能の改善を提案することもできるのです。
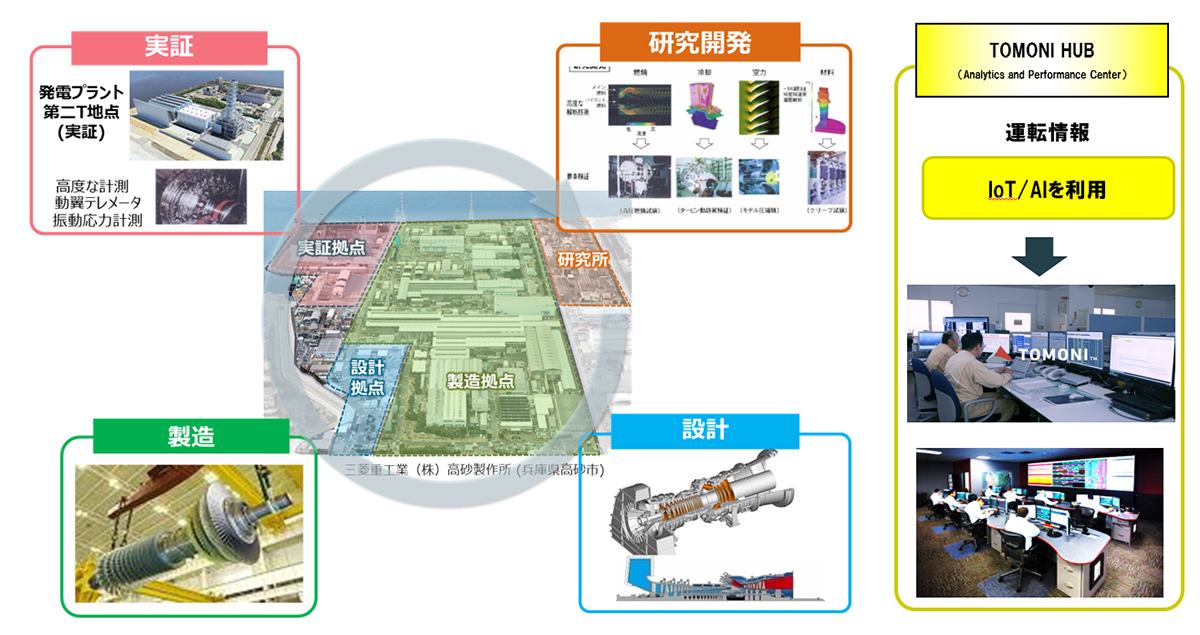
三菱重工のこうした献身的な取り組みは、同業他社との差別化を図る一つの大きな要因となります。実際に顧客からも評価されており、2022年第一四半期に三菱重工が大型ガスタービン市場で36%の世界トップシェアを獲得できたのも、こうした理由があるのかもしれません。
発電設備の主要機器であるガスタービンの購入を決断することは、大きな会社にとっても簡単なことではありません。しかし、見学ガイドによれば、高砂製作所を訪れた人のほとんどが購入に踏み切るそうです。それだけの価値が、高砂製作所にはある。その証と言えるかもしれません。
エナジートランジション専用サイト水素エコシステムの実現に向けた取り組みはこちら
Related tags
