ものづくりの現場へ: 三菱重工神戸造船所における原子炉製造
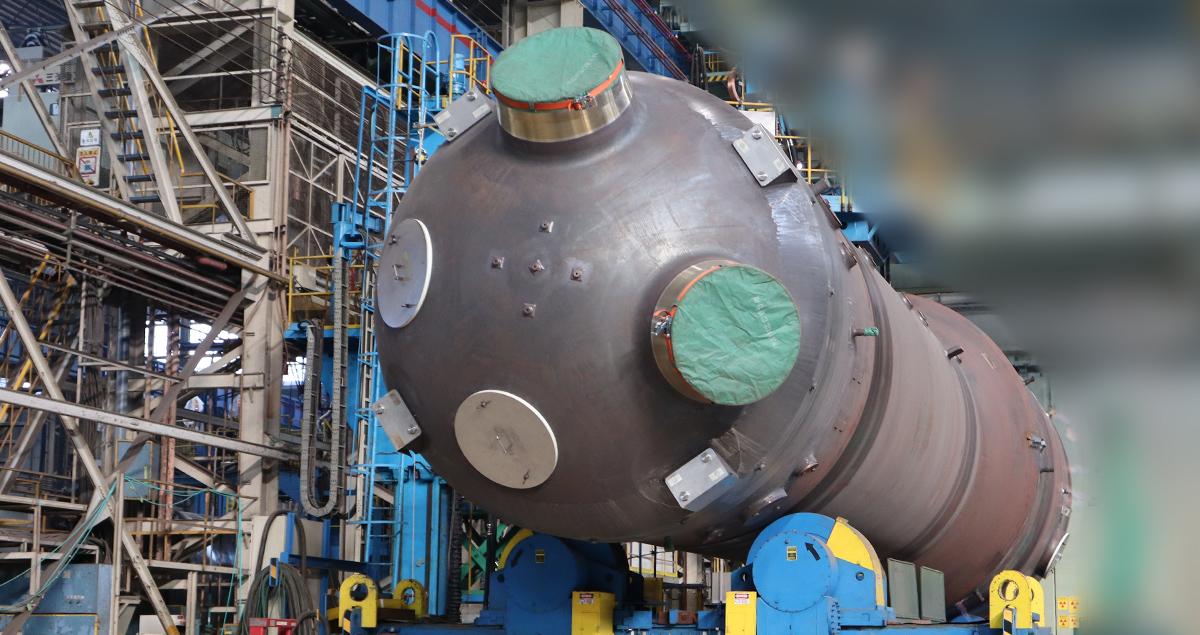
インデックス
港町・神戸にある一見簡素な工場の中には、世界でも類を見ない精密工学の粋が集まっています。工場内では、高さ11メートル、直径4メートル、重さ130トンの巨大な金属製のシェルが、設置された工作機械に沿ってゆっくりと動かされています。それぞれの機械は家ほどの大きさがあり、回転加工、切削加工、溶接などの作業を行っています。
ガイドチューブやバッフルプレートなどの500以上の部品が段階的に組み立てられますが、部品の多くは耐食性のステンレス鋼で作られており、±0.1ミリメートルの高精度で加工されます。このようにして、およそ40カ月をかけて完成するのが、原子炉の心臓部にある「炉内構造物」です。炉内構造物は「原子炉」の中に組み込まれます。原子炉にはウラン燃料が収められ、運転中は非常に高温・高圧の水で満たされます。その高温・高圧の水を使って「蒸気発生器」により、別の配管に流れる水に熱を伝え蒸気を発生させ、その蒸気がタービン発電機に送られ、電力を生み出します。
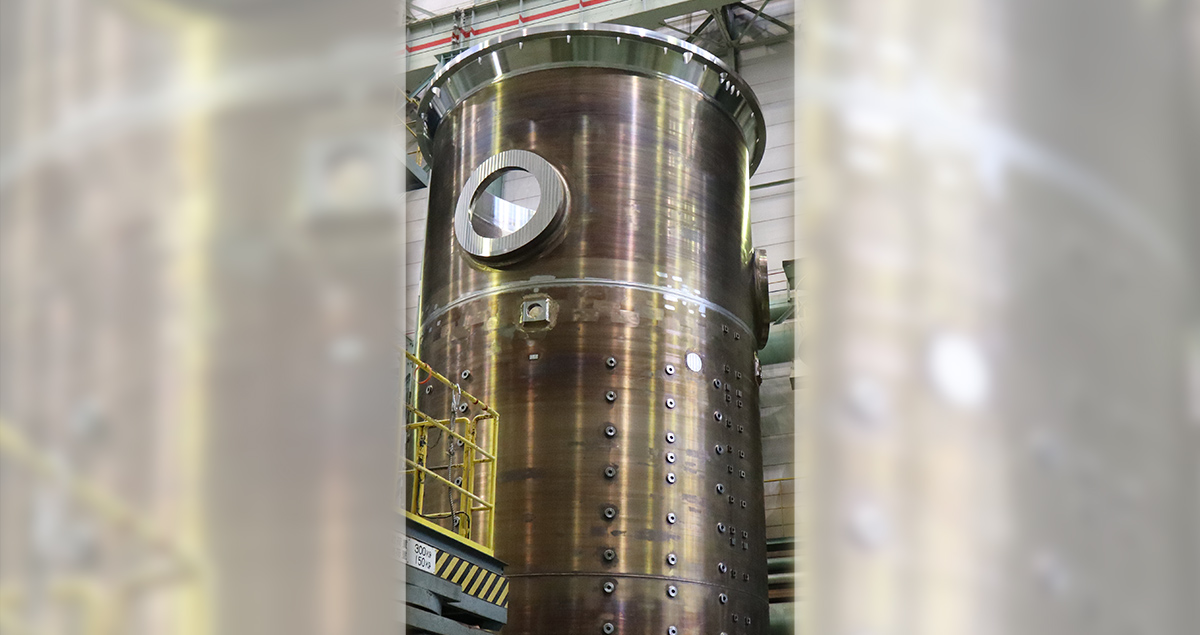
気候変動やエネルギー安全保障が世界的に喫緊の課題となっている現在、原子力発電は二酸化炭素を排出せず、信頼性の高いベースロード電源として安定的に大量に電力を供給できるという点が大きな強みです。最近では、多くの国が原子力発電所を新規に建設し、長期間停止していた原子力発電所の再稼働や、稼働中の原子力発電所の運転期間の延長を進めています。日本でも、2011年の東日本大震災以降、長らく中断されていた原子力発電所の運転が再開され始め、世論も原子力支持に傾きつつあります。
復活した原子力事業
これは、半世紀以上にわたって原子力事業に携わり、1970年に日本初の加圧水型原子炉(PWR)を建設した三菱重工にとっても歓迎すべき変化です。
三菱重工は、研究開発から計画・設計、製造、設置・試運転、定期検査・保守、プロジェクト全体の管理に至るまで、一貫したサービスを提供できる、OECD加盟国の中でも数少ない企業のひとつです。これまでに、日本国内にあるPWRプラント24基すべての建設に関与し、米国、フランス、その他の欧州やアジアの各国に主要部品を供給してきました。
日本を代表する原子力メーカーである三菱重工グループは、安全機能を強化した革新軽水炉に加え、小型軽水炉、マイクロ炉、高速炉、高温ガス炉の開発にも取り組んでいます。国内では、自社が携わったPWRプラントと他社が製造した沸騰水型原子炉(BWR)の両方の原子力発電所の再稼働に注力し、国際的には、核融合の実用化を目指すITERプロジェクトでも重要な役割を果たしています。
こうした長年にわたる技術の蓄積や、将来を見据えた原子力事業の計画の多くは、この神戸の地で進められてきました。神戸造船所と呼ばれる、67万平方メートルの巨大な工場は、1905年に造船所として操業を始め、潜水艦のほか、なんと日本初の自動車も製造しました。さらに、現在世界をリードするガスタービンなどを製造している三菱重工の高砂製作所の生みの親でもあります。(1964年に神戸造船所とは別の組織として分離)
現在、神戸造船所では、潜水艦、航空機、ロケットの部品、ターボ冷凍機など様々な製品が製造されていますが、売り上げの半分以上(約2,500億円)は原子力関連事業から得られています。そこには、エンジニアリング、建設、保守サービス、原子力発電所の中核部品である原子炉容器や蒸気発生器、大小の配管やチューブの製造などが含まれています。
品質重視のオペレーション
製品の種類は多様ですが、製造されるプロセスには共通点があります。それは、細部への徹底的なこだわりと、独自開発した技術の組み合わせです。例えば、蒸気発生器に使用される4,500本のチューブは、特注したドリルを使って、ピンポイントで正確に、そして確実に滑らかにくり抜かれています。
このように高い精度が求められる工程には、最先端の設備と最新技術が不可欠です。工場内には、日本製のほか、ドイツやイタリア製の、高性能な工作機械が並んでいます。また、神戸造船所は特に溶接技術に強みがあり、厚い金属片を一度の加工で接合でき、歪みを最小限に抑えることができる電子ビーム溶接などの高度な技術を有しています。
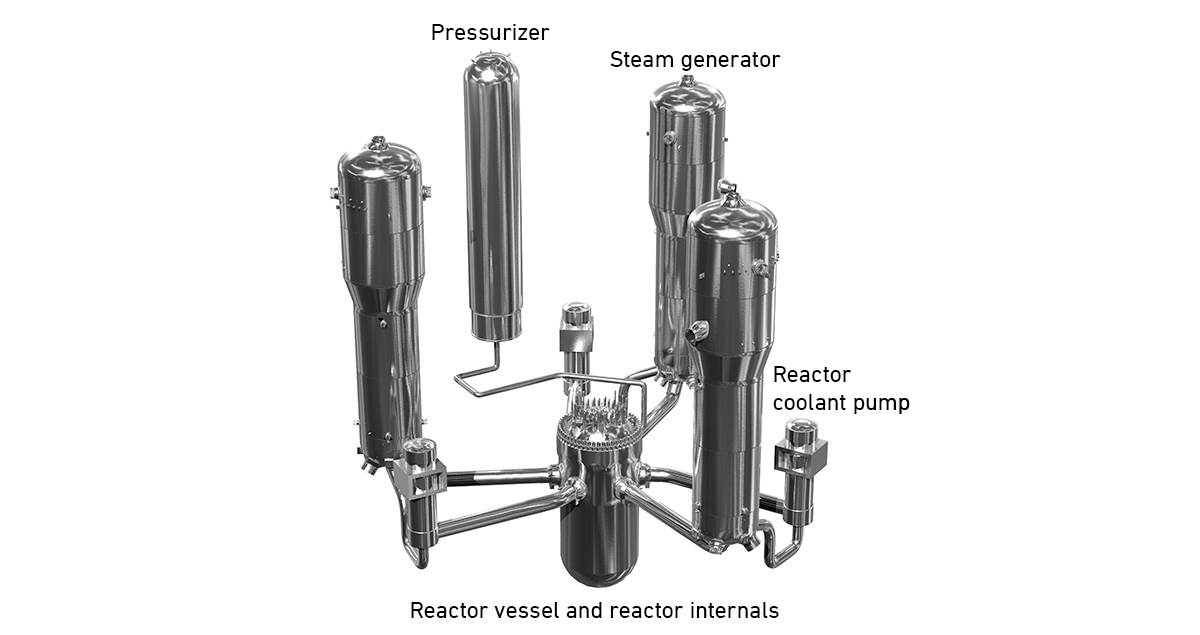
製造工程の多くが自動化されている一方で、最も難しい工程は依然として人の手で行われています。例えば、蒸気発生器の二つの主要部品の溶接作業は、3日間で行われます。外側の溶接は、サブマージアーク溶接の溶接トーチが自動で制御され、2日間で実施されます。一方で、難易度の高い機器内部の継ぎ目の溶接は、作業員が手作業で実施します。150℃を超えることから、短時間で交代しながら1日で行います。
安全を最優先に
三菱重工は、品質管理、保守、運用のいずれにおいても、安全を最優先とし、細部にまで徹底して注意を払っています。部品は製造の各段階でチェックされ、従業員の安全意識を高めるために、定期的なトレーニング、セミナー、監査が行われています。さらに、神戸造船所内には過去の事故を紹介する展示スペースがあります。従業員は少なくとも年に一度、その場所を訪れて事故の教訓を振り返る機会が設けられています。
加えて、神戸造船所には、1,000トン以上の水を注入することができる実物大の原子炉容器のモックアップを備えた独自の保全訓練センターがあり、保守作業員が実際の作業時に近い状況で訓練を受けることができるようになっています。
また、保守の面では、配管の健全性を診断する超音波センサーや、溶接継手の損傷を検査するスキャナーなど、独自の検査装置を多数開発しています。何千ものチューブを含む原子力機器は、13カ月ごとに定期検査が義務付けられています。これらの検査機器が人の指示を待つことなく、迅速かつ正確に動作することは、極めて大きな意味があります。
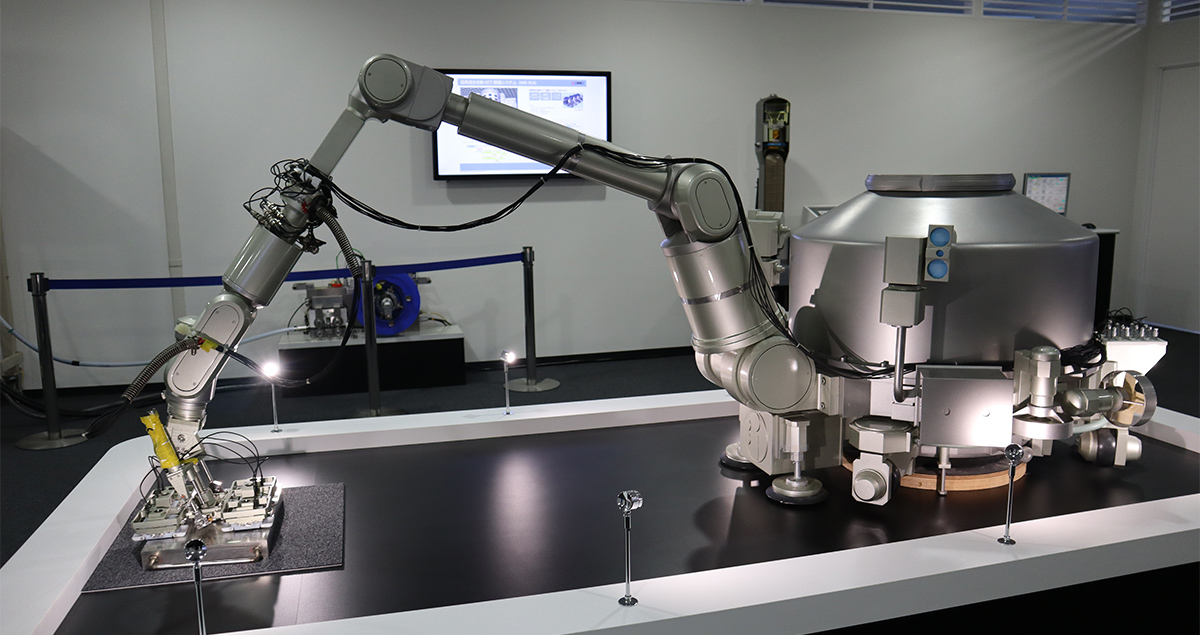
中でもひときわ目を引くのは、神戸造船所が完全に独自開発したA-UTロボットです。このロボットは、小さな金属製のキリンのような外観をしており、先端にセンサーパッドが付いた7つの軸を持つロボットアームを備えています。原子炉容器内では、潜水艦のように水中移動し、真空パッド付の脚で壁に張り付くことが可能です。
このロボットを開発するために費やした時間と労力、そしてスタッフがその機能を説明する様子からは、三菱重工が原子力事業に注ぐ強い思いと誇りが感じられました。原子力事業は、世界の脱炭素化に大きく貢献すると同時に、三菱重工グループに持続的な成長をもたらすことが期待されています。
事業紹介パンフレット 「三菱重工の原子力事業」はこちら
Related tags
